The case for pool pump upgrades
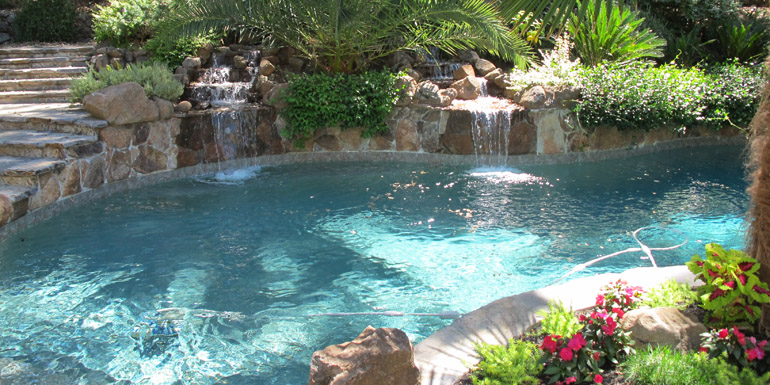
By Steve Easley and Jeff Farlow
When people talk about home energy efficiency, the conversation seldom leads to pool pumps and that needs to change. One of the most significant energy-consuming devices in homes with swimming pools is the pool pump. Pumps keep pools clean and safe by circulating water through filters. They often also circulate water through heaters, cleaners, water features or fountains. Depending on the pool, some use one pump to perform all these jobs, while others use multiple pumps. Traditional pumps typically have one- or two-horsepower motors that run at least five to six hours per day, sometimes around the clock, consuming energy.
Understanding electrical consumption
The average swimming pool pump draws approximately 1,500 to 2,500 watts. If the pump runs 4.5 to six hours each day, it can add up to 10.5 kilowatt hours (kWh) per day or approximately 1,400 kWh per year—considering the average swimming season in Canada occurs between May and September. If the pump runs all day, as is common practice in many regions, these numbers can be significantly higher.
If the homeowner also operates a pool cleaner equipped with a booster pump, it can add another 1,200 to 1,500 watts. If the cleaner operates roughly 3.5 hours per day, the total combined consumption for these two pumps could exceed 2,500 kWh per year. Electricity rates vary by region, season, time of use and total consumption. For example, the on-peak summer rate in Ontario is 10.8 cents/kWh; using the numbers above, it would cost approximately $300 to operate the pool over a four to four-and-a-half month period. Loads like this can have a dramatic impact on both the electrical grid and pool owners’ wallets. In addition, pools typically run during electric utility peak load times, further straining the electrical grid.
One way to reduce this load is to replace older, single-speed pool pumps with a high-efficient, variable-speed pump with electronic controls. A traditional single-speed pump has an induction motor with typical efficiencies of 35 to 70 per cent. By comparison, variable-speed pump motors can achieve efficiencies above 90 per cent. The special permanent magnet synchronous motors (PMSMs) used in ultra-high efficiency pumps is similar to the motors used in hybrid cars. They can vary their speed, generating only as much flow as is required for each application.
High vs. low flow
In the swimming pool environment, high flow is required for some water features, pool cleaner cycles and spa jets. High flow, however, is not required for routine filtration, the mode in which a pool pump operates most. In fact, low flow helps pool filters operate more effectively. When a traditional single-speed pump is performing all those varied tasks, it has no choice but to run at high speed, effectively producing more flow (and consuming more energy) than is needed for simple filtration cycles.
A variable-speed pump running at a low speed will draw between 120 and 400 watts and consume, on average, about 2 kWh per day. By comparison, a single-speed (high only) pool pump consumes approximately 10 to 12 kWh per day. A variable-speed pump uses very little energy for low-speed/low-flow tasks like filtration. Therefore, it is possible, depending on energy rates, to spend 10 cents filtering a particular amount of water, while it would cost a full dollar to filter the same amount of water using a standard pump.
The role of physics
Some of these savings are a result of motor efficiency; however, another significant factor is that power consumption drops at a nonlinear rate as pump (motor) speed and water flow is reduced. In fact, when motor speed and flow rate is reduced by half, the power demand is reduced to 1/8 of the original power, at least in a laboratory setting.
Actual results in the field vary but often are around 1/7. Also, with less flow, the pump needs to run longer to achieve the same turnover for filtration purposes. As a result, the energy consumed will not be 1/8 when using half the flow, but can easily be 1/4. This is because the pump needs to run twice as long while consuming 1/8 of the power (i.e. 1/8 x 2 = ¼).
In other words, by running the pump slower, even though it will be operating longer, the lower speed translates into dramatic savings in energy consumption and operating costs. Plus, variable-speed pumps have higher quality motors—not only are they remarkably quiet, they also last longer, putting less strain on the filter, plumbing and other parts of the system.
When determining the ideal run time for the filtration system, it is important to make sure sanitizer levels are monitored and maintained and that water clarity is acceptable.