Variable speed pumps
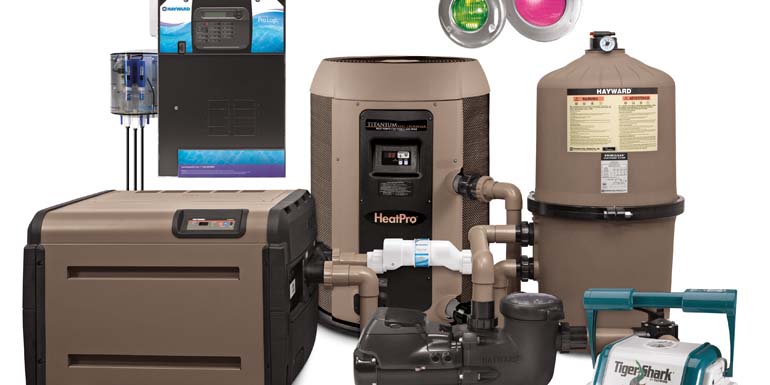
By Scott K. Petty
With the advent of various legislation aimed at improving the energy-efficiency of appliances and similar products, energy-efficient pumps have become a popular topic within the pool and spa industry. Every pool and spa circulation system requires at least one pump; many have multiple units. As a result, pumps represent the largest aggregate consumption of energy on the equipment pad. Some studies have estimated pool pumps to be the second-largest energy consumer within an entire household, following only heating, ventilating and air conditioning (HVAC) systems.
Variable-speed pumps provide a great opportunity to reduce this energy consumption while also lowering operating costs for the homeowner. While energy efficient single- and two-speed filtration pumps have been available for many years, variable-speed pumps are a relatively new addition to the equipment pad. These pumps often represent the latest in motor technology, with advanced features specifically designed to reduce energy consumption while still providing the flow needed to operate sanitization, heating and other equipment necessary to maintain and enjoy pools and spas.
What makes variable-speed pumps so efficient?
A variable-speed pump has three primary components: the motor, the hydraulic wet end and the variable-speed drive. As with common single- and two-speed pumps, the motor’s primary function is to convert electric energy into mechanical energy, in order to spin the shaft connected to the impeller. However, there are two important distinctions with respect to motor construction typically used in variable-speed pumps:
- The use of permanent magnet technology; and
- The use of totally enclosed fan cooled (TEFC) designs.
Compared to the standard induction motors used in most single- and two-speed pumps, permanent magnet motors are more energy efficient, especially at reduced loads that occur at lower speeds. The totally enclosed design prevents debris and water from accessing the windings, which improves the reliability and service life of the motor and, by extension, of the pump itself.
The wet end of the pump converts the mechanical energy from the motor into hydraulic energy, providing the flow and pressure needed to operate and maintain a pool or spa. While much emphasis is often given to the permanent magnet and totally enclosed motor technologies, the wet end design should not be ignored. After all, it is the combination of electric and hydraulic efficiency that drives the pump’s overall energy efficiency.
As hydraulic efficiency improves, the pump can move more water for the same amount of electrical work. When combined with a variable-speed drive, the pump can achieve the necessary flow at a lower operating speed. This energy savings is a result of the Pump Affinity Law. With the impeller diameter as a constant, this law states the following three relationships:
- Flow is proportional to shaft speed (typically expressed in revolutions per minute [rpm]);
- Pressure (head) is proportional to the square of shaft speed; and
- Power is proportional to the cube of shaft speed.
The most common example given when reviewing the Affinity Law is describing the change in flow, pressure and power when motor speed is reduced by 50 per cent.
Take, for example, a 3,450-rpm pump (the speed of a single-speed pump, or high speed of a two-speed pump, operating at 60 Hz). When the speed is reduced by half (1,725 rpm), the flow is also reduced by roughly 50 per cent. In turn, the pressure is reduced by the square (0.5 x 0.5 = 0.25); power is reduced by the cube: 0.5 x 0.5 x 0.5 = 0.125 (actual savings may be less since the impeller is typically optimized for a particular speed). Even if the pump is operated twice as long in order to maintain the same turnover rate, the energy consumption is up to 75 per cent less (0.125 x 2 = 0.25 energy consumption or 75 per cent savings) than when operated at high speed.
To put this example in financial terms, using an average cost of electricity of 15 cents per kilowatt-hour (kWh), a single-speed pump operating at 3,450 rpm and 2,000 watts would consume 16 kWh over an eight-hour period, resulting in a total cost of $2.40 per day. If the speed was reduced to 1,725 rpm, power consumption would drop to approximately 250 watts and total energy used would be 4 kWh over a 16-hour period (run time doubled to achieve the same turnover) at a total cost of $0.60 per day. This would translate to savings of $54 over the course of a month and as much as $648 per year based on a 12-month season. While actual savings will vary based on a comparison pump model, hours of operation, electrical rate and other hydraulic factors (e.g. plumbing size and length), the savings can be quite significant.
The key benefit of variable-speed pumps is that the speed can be reduced beyond half speed (1,725 rpm), which, according to the Affinity Law, will result in even greater energy savings. When combined with an energy-efficient permanent magnet motor and a hydraulically efficient wet end, variable-speed pumps have been proven to save as much as 90 per cent compared to ordinary single-speed pumps, often translating into savings of more than $1,000 per year.