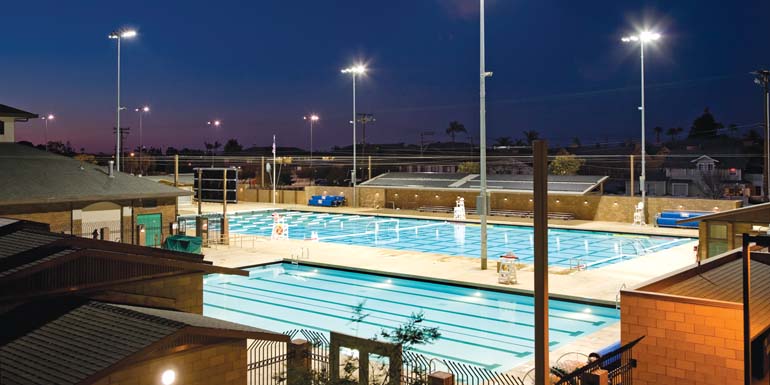
By Randy Mendioroz
With the increasing costs of energy, selecting equipment and systems to provide better operating cost efficiencies is extremely important to the long-term financial viability of any commercial aquatic facility.
First, the bad news. The annual operating cost for a typical 50-m (165-ft) outdoor commercial pool, including water, power, heating and pool chemicals, is about $307,538* per year. The largest expense is natural gas at $216,972 (71 per cent of the total cost). Electricity is next at $43,275 (14 per cent), followed by pool chemicals at $31,698 (10 per cent) and finally, water and sewer costs at $15,592 (five per cent).
In California, over the past few years, the cost of natural gas has increased from an average of $0.55 to over $1.00 per therm and the cost of electricity has jumped from $0.10 up to $0.15 per kilowatt hour. This means operating costs for a typical outdoor commercial pool have increased by more than $123,000 annually. Prices have risen similarly across North America, though not as severe.
What’s the good news? Today’s basic pool design strategies and cutting-edge energy alternatives are excellent at maximizing operating efficiency when planning a new aquatic facility or renovating an existing one.
Keep it pumping
At times, commercial aquatic consultants and contractors select the facility’s pool pump based on the primary factors of initial cost and availability. For example, a cheaper, readily available self-priming pump, which runs at a relatively high 3,450 revolutions per minute (RPM) may only operate at 55 to 60 per cent motor efficiency. However, if a lower RPM pump motor is selected, which runs between 1,750 to 1,150 RPM, motor efficiency of up to 85 per cent can be achieved.
One goal of energy-efficient design is to select pumps with a minimum 75 per cent motor efficiency. These pumps will initially cost more and must be installed at an elevation below the static water level of the pool being served. Another benefit to low RPM pumps is motor longevity, which can be twice that of their harder working counterparts.
Account for the variables
In addition to selecting more efficient pumps, the use of variable frequency drives (VFDs) can significantly reduce energy use associated with electric motors operating over extended time periods.
For example, in many jurisdictions, state and local health departments mandate the sizing of swimming pool circulation pumps for the worst possible condition (i.e. dirty filter conditions and a pump strainer full of debris). This means, when conditions are optimal, the circulation pump is oversized for the actual design condition. In some cases, health regulations mandate a 20-horsepower (hp) pump, when the actual design condition for 95 per cent of the operating hours would only require a 15-hp pump.
By connecting a VFD package to the pump motor and utilizing a highly accurate, digital flow meter that feeds back to the VFD, the operator can adjust the required flow rate as required by the health department. This allows the VFD to control the voltage to the pump motor based on the actual design condition.
If the filter is clean and the pump strainer is empty, the pump motor does not have to work as hard to deliver the required flow rate. Similar to a dimmer switch, the VFD can increase or decrease the horsepower as the conditions require, resulting in considerably higher motor efficiencies. VFD pump motor packages in the 10- to 20-hp range cost approximately $3,000 to $5,000; however, many pool operators have reported electricity cost savings between 30 to 50 per cent as a result.
In a recent case study, Chowchilla Union High School District (in California’s Central Valley) received an energy audit from Resource Solutions Group through their School Energy Efficiency (SEE) program for using a Smart Pump Control System (SPCS) advanced VFD package manufactured by H2O Technologies. The table below shows the final costs, calculated energy savings and rebate amounts for the system. It also includes information on the simple payback (SPB), internal rate of return (IRR) and net present value (NPV), and shows the project will pay for itself in less than two years by providing the school district with significant utility cost savings.
Variable Frequency Drive Systems: Costs vs. Energy Savings |
|||||||
---|---|---|---|---|---|---|---|
Measure | Installed | Rebate | Net | Annual | SPB | IRR | NPV |
Name | Cost | Received | Cost | Savings | |||
Pool VFD | 29470 | 6880 | 22950 | 12900 | 1.8 | 0.61 | 157174 |