By Peter Vamvakaris
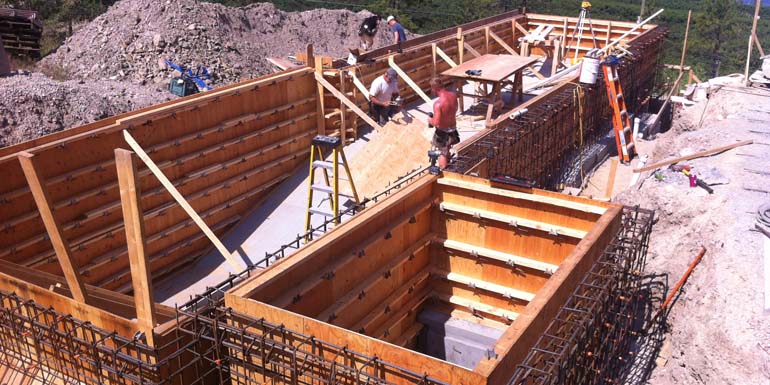
When a client requests a concrete pool, spa, or water feature design, what they are essentially asking for is a vessel constructed of a mix comprising aggregate, sand, cement, and water that is placed over structural steel. One of the great benefits of designing a concrete vessel is the only limitation is the builder’s imagination. The execution of building the design may vary, and here begins the use, or possible misuse of terms that has continued for decades between pool designers, builders, and customers. Terms such as gunite, shotcrete, and cast-in-place, are used interchangeably and are all viable options in the construction of pools and spas. And, although each method used the same primary ingredients, each one is uniquely different.
Whether a pool is built using either one of the three methods mentioned above, in the end, it is constructed of steel and concrete and, therefore, it is a concrete pool. Customers often refer to their pool as a ‘gunite pool,’ or ‘shotcrete pool,’ although the placement technique and mix design vary, they are all concrete vessels.
Cast-in-place
Some of the top pool builders in Canada use this technique as part of their construction process, referring to similar technology used to build today’s contemporary skyscrapers with pinpoint accuracy. This technique requires skilled tradespeople to fabricate on-site forms and to place the ready-mix concrete in between the forms, while agitating it to remove any voids. Once the concrete sets, the forms are removed and the surface is prepared to receive the selected finishes (e.g. tile, stone, and/or cementitious coatings such as aggregate finishes). Other methods for cast-in-place vessels include the use of pre-fabricated panels that are connected, with concrete placed between them.
The use of cast-in-place to construct watertight vessels requires the use of various water-stop products, concrete additives, and waterproof membranes as multiple pours create cold joints (i.e. joints that are formed when two batches of concrete are placed at different intervals and the first batch, which has already been compacted, has started to set).