By Brian Field
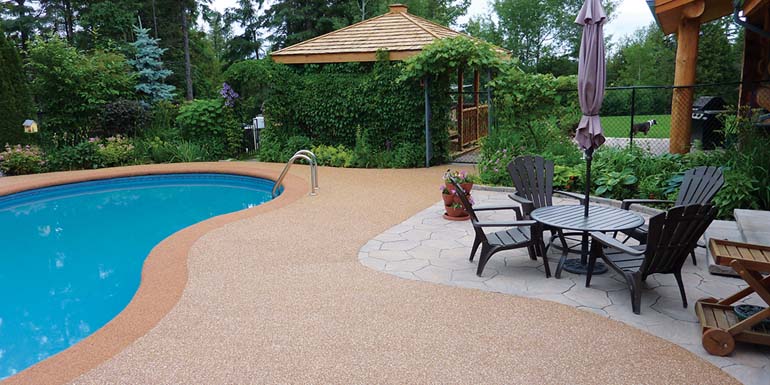
Rubber has been used as an anti-slip surface in and around wet areas for much of the past century. It is proven to be a great performer in providing excellent grip and preventing falls, which can turn nasty very quickly on hard, wet surfaces such as pool decks. The problem, however, was rubber always came in the form of a mat or other temporary surfaces and only provided safety in a localized area.
Everyone is familiar with the term ‘necessity is the mother of invention,’ and what was necessary in the pool environment was the need for a non-slip seamless surface, which could be easily adapted and customized to fit any area.
Cue the poured-in-place rubber surfacing market. In a trial back in 1983, granules of rubber were mixed with a high-tech polymerized resin and trowelled over the surface of a pool deck in Garland, Tex. Since then, rubber surfacing has become a popular and efficient way to cover existing decks. In some cases, it is specified on many new construction projects—commercial and residential.
Lay some rubber
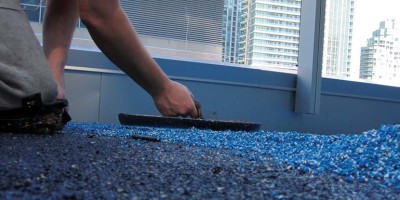
With applications ranging from low-use residential backyard pools to the extreme durability requirements of a major theme park, the composition of the rubber and binder is critical to achieving long lasting success. For someone in the market for a rubber surfacing installation, they will likely encounter a number of different options before making a final decision for what works best for their project. The first selection, however, is the type of rubber to use.
Many different types of rubber can be used for surfacing, all of which are synthetic polymers. Rubber surfacing does not use any natural rubber, which also means it is latex free. Synthetic rubber is cheaper and easier to produce than natural rubber; therefore, with many applications already in use in the automobile industry, it was an easy decision when it came to the materials used on that first pool deck in Texas. That said, there are many different types of synthetic rubber to choose from. The following is a look at which type of synthetic rubber should be used for different applications.
Styrene-butadiene rubber (SBR)
The most common and cheapest type of synthetic rubber available is called Styrene-butadiene rubber (SBR). The basic elements that make up SBR—styrene and butadiene—are byproducts from the petroleum industry. Most commonly used by tire manufacturers, SBR can also be found in shoe soles, hoses, and other applications requiring a cheaper durable rubber.
In the rubber surfacing business, SBR has a wide variety of applications. Almost all of the SBR used comes from the recycled-tire market. This also means it is almost always black. In playgrounds, SBR is the key element in providing the shock absorption layer. It can also be used as a topcoat for a playground surface and running tracks. To achieve different colours when using SBR, it is typically painted with
an acrylic coating or by using a tinted binder. Painting the SBR granules is a less expensive way to achieve a colourful poured-in-place rubber safety surface; however, it does have some drawbacks.
For instance, the colour will wear away, depending on the amount of use the surface gets, revealing the black granule. This creates the need for periodic re-coating of the surface, which can quickly offset the initial cost savings, not to mention the inconvenience of the shutdown periods.
Typically, an SBR surface will be recoated every two to three years. If installed properly and maintained, an SBR surface will last a long time, but it might be worth considering other options.
One comment on “A guide to non-slip coatings”