Renovating pools using heat-welded PVC membranes
By Aimée Samuelson
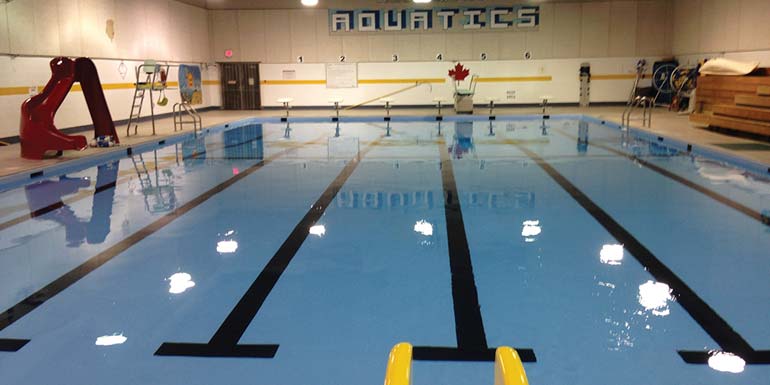
Outdoor commercial pools located in regions where severe freeze-thaw cycles occur are perpetually plagued by the effects of freezing winter temperatures and extreme heat in the summer. From peeling plaster and paint to cracks and leaks, most pools typically require a fair amount of refurbishing each spring to ready them for the summer. These facilities are typically hit the hardest as the funds to repair these pools is often difficult to obtain due to municipal or operator budgets. To avoid the vicious cycle of annual repairs and patches, one construction option that is prevalent of late is the use of 60-mil reinforced polyvinyl chloride (PVC) membranes.
The concept first started in Europe more than 30 years ago and came to the Americas shortly after. However, in the last five years, this construction/renovation method has gone from novel to mainstream.
“Commercial proposals for pool renovations now specify PVC membranes when repairing the pool structure,” says Ron Melbourne of Membrane Concepts in New Bedford, Mass.
Pools that are continuously exposed to freeze-thaw conditions will almost always crack and eventually start to leak due to the resulting ground movement. Aquatic facility managers are then forced to repair the pool before it can be opened for the season. Coming up with funds every spring for this repair work can quickly add up in a few short years.
Today, an increasing number of outdoor and indoor aquatic facility operators are being introduced to the concept of installing PVC membranes to solve hidden issues and, more importantly, make the pool vessel watertight without having to pinpoint the exact area of the pool structure where the problem is occurring.
“Once you have eliminated the leaks in the lines and plumbing, many older pools continue to lose water due to hairline cracks that are virtually impossible to find,” says Troy Fleetwood of Watson Pools in Edmonton, Alta. “A PVC liner membrane can immediately solve this problem.”
The installation process
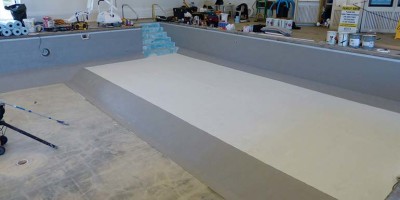
The installation method is relatively simple. Before the pool is lined with the PVC membrane, it is prepared by fastening a series of flexible, PVC strips along the perimeter, under or over the coping, depending on the deck configuration. Then a felt-lining is applied to the pool’s floor and walls using an adhesive. This lining protects and smooths-out the surfaces before the PVC membrane is installed (it also makes the pool more comfortable for users by giving the floor and walls some cushion, which is pleasing to bathers’ feet. After the felt lining is in place, the PVC membrane, which typically comes in 1.8-m (6-ft) wide rolls, is rolled out and positioned within the pool. The material is basically ‘tailored’ to the pool on-site.
Once the pieces have been measured, cut, and positioned, a ‘tack weld’ or ‘pre-weld’ is used to keep the material in place. Each seam is heat welded on-site using a heat gun, which uses hot air to essentially melt and seam the material together. The material needs to be overlapped by 51 to 76 mm (2 to 3 in.) and seamed using the heat gun. The membrane that comes up the pool walls is ultimately ‘terminated’ by being welded directly to the PVC band along the pool perimeter. To add another waterproofing measure, many installers also apply a sealer along the seam edges to ensure water does not seep into the scrim of the material over time. This sealer also rounds out the seams and adds an extra layer of waterproofing to the liner. Areas such as steps, beach entries, and safety ledges are also cut, fitted, and welded in place. PVC membranes are also available with a slip-resistant emboss, which is typically used on steps. Generally, standard pool fittings and returns are compatible with PVC membrane installations.
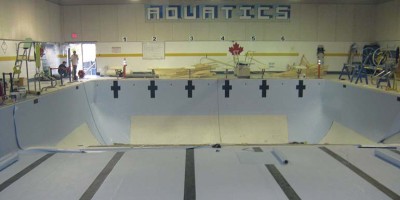
“The work does require training to ensure a precise fit, its true craftsmanship, like a tile-installer,” says Fleetwood. “This is especially true when installing the membrane on steps, beach-entry pools, safety ledges, etc.”
Membrane installation on an average commercial pool takes approximately four to five days. For some facilities, this short-term shutdown is well worth the cost to eliminate the need to re-plaster and paint the pool structure every year.
Most pools can be prepped in one day (or less) before starting the membrane heat-welding process, explains Melbourne.
“We do run across pools that are in really bad shape and have spent three to four days patching the pool, fixing returns, etc., before laying down the felt and welding the liner in place, but this is not the norm,” he says.
There are also several different approaches to installation, says Tommy Nachmann, international sales manager at Haogenplast, a supplier of PVC membrane material located in Israel.
“I have seen many different installation techniques used based on the different craftsmanship styles of the installers” he says. “Therefore, techniques may vary from country to country and installer to installer. The end result is still a water-tight pool in which the 60-mil PVC has quickly repaired problems in existing pools.”