Education, training, key in preventing accidents on the jobsite
By Steve Goodale
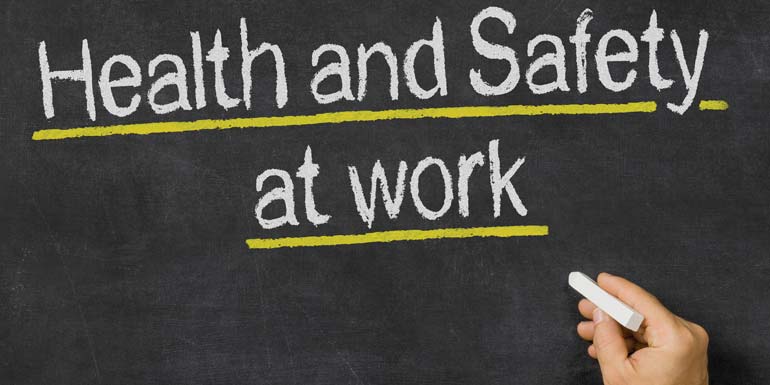
Building, renovating, and servicing pools and spas/hot tubs is a dangerous occupation and one that puts workers in close contact with potentially hazardous situations daily. Machinery, tools, water, electricity, chemicals, and confined spaces are all common in the workplace for those in the aquatics industry. No matter the company’s size—whether a large firm with hundreds of employees or an entrepreneur operating out of their truck—the importance of safety at work is equal.
There is nothing more important to any company than avoiding a serious or fatal injury on the job, and smaller injuries at work are detrimental to the efficiency of the company as well as being detrimental to the health of the injured worker. It is in the best interest of all parties to reduce the likelihood of
a workplace accident. An accident can happen to anyone, at any time. The statistical likelihood of experiencing one can be reduced with proper education, training, and the right frame of mind. To create a safe working environment, this article will discuss a few things that need to come together.
Education
Proper education to identify and reduce the potential for dangers at work is paramount in establishing a solid, long-term approach to avoiding accidents. Understanding the nature of how quickly accidents can happen and the severity of not following established safety protocols is something all new employees must be taught.
In the pool and spa/hot tub industry, many new, untrained workers can be added to the roster in a short period of time due to the seasonal fluctuations of the job. This can create a logistical problem with respect to bringing everybody up to speed when each worker is starting from a different level of base knowledge.
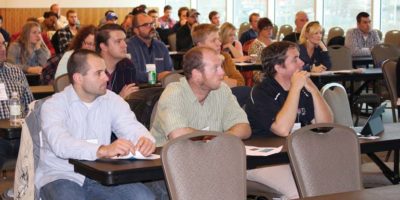
In some cases, many seasonal workers are experiencing employment for the first time and need special attention with respect to the basics of workplace safety. What might appear to be common sense to one person may not be the same for another. Among the many job-specific dangers new employees must be educated about, there are some fundamental safety rules employees should follow.
For instance, if something looks dangerous, or it is not understood how to proceed safely on the job, then work should be stopped immediately to seek the advice of a supervisor.
Do not shortcut established safety protocol to save time either. The cost of doing business is such that a job takes as long as it does to do it safely.
If someone else is working in an unsafe manner, regardless of who they are in relation to their position within the company, ask them to stop or report the situation to a manager or supervisor.
To say an employee should report unsafe work to a manager may likely ruffle a few feathers with more experienced workers who have developed their own internal tolerance for what is and is not considered safe on a jobsite. After many years in the same position, complacency of experienced staff is one of the biggest dangers on a jobsite, and something that must be sought out aggressively by management.
In most cases, when a serious injury occurs at work, there is an established safety standard that was not being followed at the time of the accident. Education for employee safety is more than teaching individual rules; it is an opportunity for managers to affirm the importance of safety within the company with the employees. This will assist greatly once the employee is in the field, far from view of the management team, where the opportunity for uncertainty or pressure from other workers to do something unsafe exists.