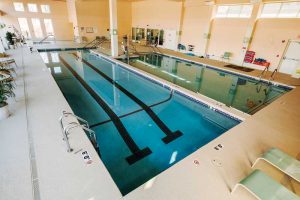
Using process of elimination to diagnose and repair heating equipment
By Tom Soukup
Troubleshooting pool heaters is not rocket science; however, it does take experience and several specific tools. Companies with a background in residential and commercial boiler systems must be well-equipped, and technicians should be well-trained to install, diagnose, and repair a variety of gas-fired equipment. Since pool water heaters are only one portion of the industry, some technicians may find themselves working on heating equipment in which they do not have the right tools to carry out the job properly.
Aside from the pool heater manufacturer’s installation and operation manual, the two most important tools for diagnosing heater issues are a multimeter, which allows a technician to check voltage and resistance, and a gas monometer for checking gas or liquid petroleum (LP) pressure. These are the essential minimum requirements for any professional pool heater service technician to have when on a troubleshooting call.
Upon arriving to the facility
When a service technician is sent out on a troubleshooting visit, the first thing they should do is inspect the installation of the heating equipment to make sure it meets the manufacturer’s requirements in addition to the local prevailing code requirements.
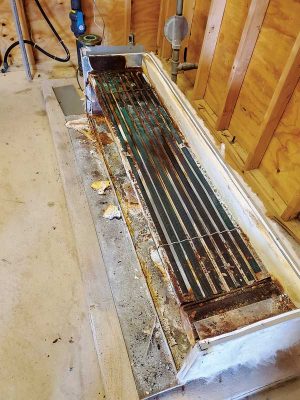
Technicians should then ask the customer what the issue or complaint is. Further, it is important techs also ask the client if other people have looked at it and, if so, what work have they performed. The initial inspection, along with the answers to these questions, will help technicians gather the information needed to direct their diagnosis.
For instance, if the heater does not come on, no lights are illuminated, and the display screen is blank, the prognosis is an electrical issue. When faced with this problem, technicians should check the circuit breakers, as well as to see if the heater is on a timer or if it is also included as part of an automation system. If all these things are absent or functioning, the next step is determining if there is voltage at the heater. If there is, this is when a technician should refer to the manual to begin the rest of the troubleshooting procedure.
If the heater is on but will not fire, the problem could be caused by a fuel supply issue. Although it can still be an electrical problem, technicians should start by inspecting the fuel supply. If the heater uses propane, check to make sure the tank has sufficient fuel. If it uses gas or LP, check to make sure all valves are open.
After performing these basic checks, a technician must ensure there is sufficient water flow through the heat exchanger. In doing this, make sure the pump is running and, if not, determine why.
Heaters either have a pressure switch or a flow switch to ensure flow is established. To protect the heat exchanger, most heaters will not fire if water flow is not established. As a result, low flow can be attributed to clogged filters or valves in the wrong position.
Power, fuel, and water flow are the external requirements that must be met first. If these needs are met and the issue prevails, it is now time for the technician to troubleshoot the heater.