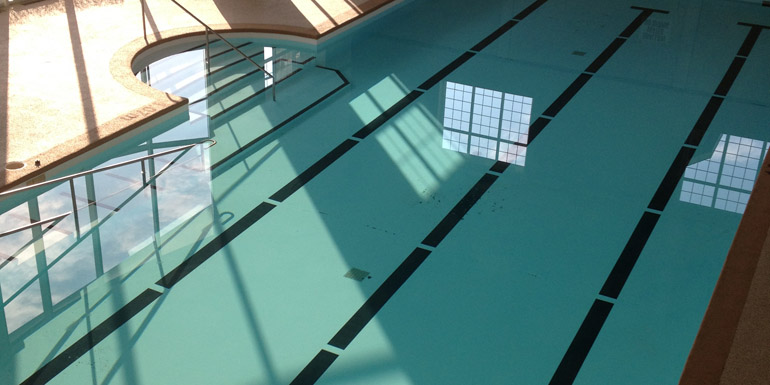
By Peter Gibson
The commercial construction of swimming pools typically started after the Second World War, when urban sprawl was underway and families moved from the cities to the suburbs. Before that most pools were large, poured-in-place concrete vessels that were finished with chlorinated rubber paints.
With the advent of the gunite process, builders could design and install custom-shaped pools much faster and in larger volumes. This brought the price down, making swimming pools more attainable for the average homeowner. Also at this time, the decision had to be made on how to finish the raw gunite. More often than not, white Portland cement with a fine marble aggregate was the best choice as it is a cement-based product compatible with gunite. The rough nature of gunite ensured the marble plaster would bond quite well. The plaster’s function was to waterproof the gunite and provide an esthetic finish that enhanced the pool’s appeal.
As the pool industry matured, manufacturers offered new pool owners a number of different options for pool construction (i.e. metal/polymer wall pools with vinyl liners, tile, and prefabricated fibreglass). Today, these construction alternatives are very versatile in their range of materials and shapes.
Pool surface restoration
A common trend among these different pool construction methods and finishes is they eventually deteriorate and need replacement or restoration. As a steel-wall pool is constructed to receive a vinyl liner, it is typical to install a new one once the old liner reaches the end of its useful life. Poly(vinyl chloride) (PVC) liners are also used to line cracked and leaking concrete pools. Finally, another popular renovation system, predominantly used in Europe, uses vinyl fused to metal.
Today, when it comes to refinishing plastered gunite pools, there are many cementitious options available (e.g. basic white plaster, specialty plasters, and an array of aggregate plasters). High- grade plasters incorporate many additives and modifiers to enhance the service life.
There are essentially two methods used to prepare a pool for re-plastering: applying a bond coat, which roughens the surface so the new plaster adheres; and chipping the old plaster down to the gunite, and applying new plaster. The former method has some mixed results; while the latter method is preferred as it significantly improves the bond and eliminates many of the ‘pop-off’ problems. The latter method is more costly, but this assures enhanced bond promotion.
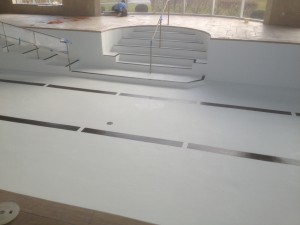
Cement-based materials do not offer any structural benefits and should not be considered for cracked and/or leaking pools. Historically, however, before fibre-reinforced plastic (FRP) linings were an option, many owners with cracked pools installed vinyl liners, but installation problems were encountered with this method. For example, inaccurate cutting and sizing of the liner, and the need to alter the pool structure for liner attachment purposes. Prefabricated fibreglass pools were also used for cracked pools, but this was impractical and expensive.
A FRP lining system is applied as a liquid and on curing it conforms to the shape of the concrete structure. There is no need for special sizing and fitting or deconstruction of the vessel. Elastomeric membranes like polyureas and glass-fibre reinforced linings are a viable option when structural considerations are required. Polyureas and glass-fibre reinforced plastic (GFRP) linings have some flexibility and crack-bridging properties.
In essence, warranties for cement-based pools cover the application and not the material performance itself, due to the nature of the material and its deterioration over time in pool water. The type of cementitious material chosen for a project will determine the service life.
Plaster products are not suitable for use in steel pools; therefore, polymeric materials are the natural choice. Polymerics are also a better option for commercial spas where the water temperature is maintained at 40.5 C (105 F). Higher water temperatures can be aggressive on cement finishes; causing spalling, roughness, algae growth, staining, and loss of esthetics, not to mention an uncomfortable experience for bathers. Tile is also a good choice for refinishing spas.