Building swimming pools
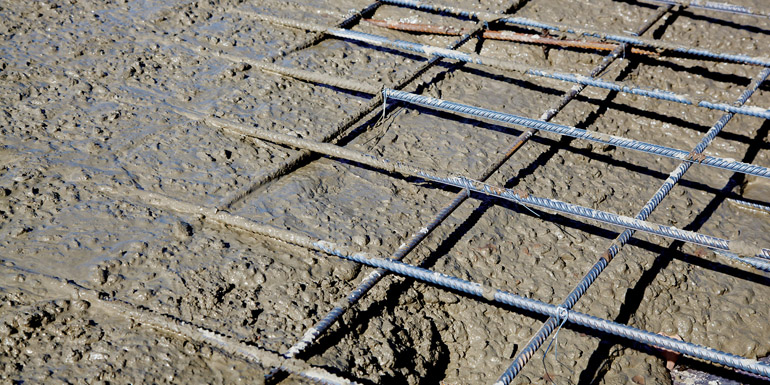
By John Petrocelli
Concrete is undoubtedly one of the most widely used materials in construction. It is used in everything from sidewalks and skyscrapers to swimming pools and landscapes. Much of this is due to its relative abundance, ease of use, portability, and cost effectiveness. Due to its physical properties, concrete is best suited for applications where it is loaded axially in compression (i.e. columns, slabs on grade, etc.). Concrete has an extremely high compressive strength with a normal range of 15 to 32 MPa (2,175 to 4,641 psi) in the pool and landscaping industries. This is perhaps the most popular and well-known property of concrete and is often the only one used to specify a concrete mix in pool and landscape projects.
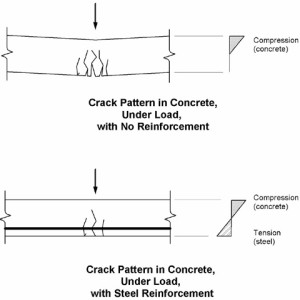
Unfortunately, this heavily utilized building material has its limitations. While concrete is strong in compression (pushing forces), it is extremely weak in tension. Therefore, it will crack easily if exposed to ‘pulling forces.’ In most structures, tension forces are present; therefore, plain concrete is not a suitable building material. However, by incorporating steel into the concrete, a hybrid building material is created, which offers strength in both compression and tension (see Figure 1).
When structural steel, in the form of reinforcing rods (rebar) is added to the plain concrete, the resulting hybrid material is called reinforced concrete (RC). The rebar is positioned where the structural member will experience tensile stresses, and in doing so, will provide the tensile strength needed. Engineers use structural analysis to calculate the magnitude and location(s) of stresses within each member of a reinforced concrete structure.
History of steel
The development of steel traces back 4,000 years to the beginning of the Iron Age. Before iron (Fe), bronze was used for everything from construction, architecture, jewellery, and weaponry. Its major flaws, however, was that it was relatively weak and hard to find.
Eventually, bronze was replaced by iron simply because it was harder and stronger. By the 17th century, the properties of iron were well understood and it became the most abundant material used in civilization. As more and more uses were found for iron, its popularity as a building material continued to grow.
By the 19th century, its use peaked due to the incorporation of steel to build the railway systems; however, it was far from being a perfect material as it was still fairly brittle and expensive to make. As a result, governments created monetary incentives to improve the properties and processes of steel. Metallurgists (someone who examines the physical and chemical behaviour of metals and alloys) were highly rewarded for developing ways to make metal less brittle and cheaper to produce. As a result of these incentives, in 1856 Henry Bessemer developed an efficient way to use oxygen (O) to reduce the carbon (C) content (responsible for the brittleness) of iron, and hence, creating the modern day steel. With its more ductile properties and its less expensive processing, steel eventually found many more uses.
Modern day steel
Today, there are many different types of steel, e.g. alloy, stainless steel, tool steel, and the most common, carbon steel. The latter is widely used in construction as structural steel and to create reinforcing steel or rebar. The main alloying constituent of this steel is carbon.
The American Iron and Steel Institute (AISI) defines carbon steel as the following: “Steel is considered to be carbon steel when no minimum content is specified or required for chromium (Cr), cobalt (Co), molybdenum (Mo), nickel (Ni), niobium (Nb), titanium (Ti), tungsten (wolfram [W]), vanadium (V), or zirconium (Zr), or any other element to be added to obtain a desired alloying effect; when the specified minimum for copper (Cu) does not exceed 1.04 per cent; or when the maximum content specified for any of the following elements does not exceed 1.65 per cent manganese, 0.60 per cent silicon, and 0.60 per cent copper.”
Carbon steel is classified as either:
- Mild/low (structural steel)
- Medium (automotive parts)
- High (springs and high-tensile wires)
- Ultra-high (knives/cutlery, axels, etc.)
Steel grades and types
There are approximately 3,500 different grades of steel. They are composed of iron and carbon and other impurities and alloying elements. It is the variation of these impurities and alloying elements that result in all the different varieties of steel grades. The carbon content also varies to form different grades of steel. It typically ranges from 0.1 to 1.5 per cent, with the most widely used range being 0.1 to 0.25 per cent. The properties required or the application will dictate the composition of each variety of steel, each having its own benefits.
Carbon steel properties
The following are some of the most popular physical properties of steel that result in its use as a reinforcing material for reinforced concrete:
- Density 7,850 kg/m3 (490 lb/cf)
- Elastic modulus 190 to 210 GPa (27,500,000 to 30,000,000 psi)
- Poisson’s ratio 0.27 to 0.3
- Thermal expansion 11 – 16.6 (10-6 /K)
- Tensile strength 276 to 1,882 MPa (40,030 to 272,961 psi)
- Yield strength 186 to 758 MPa (26,977 to 109,938 psi)
- Per cent elongation 10 to 32 per cent
- Hardness 86 to 388 HB (Brinell 3,000 kg)
Of the above physical properties, the most significant in terms of the creation of reinforced concrete are the coefficient of thermal expansion and the tensile strength in comparison to concrete. The upper limit of the coefficient of thermal expansion of plain Portland cement concrete is approximately 13 (10-6 /C), which is similar to that of steel, eliminating large internal stresses due to differences in thermal expansion or contraction.
This is important since the effects of temperature will not create additional ‘internal’ forces that need to be accommodated in addition to the physical loading conditions of the reinforced concrete member. As mentioned above, reinforcing steel is placed into concrete in the areas where tensile stresses will be present as a result of design loading. As the tensile strength (resistance to tensile loads) of steel is between 30 to 50 times greater than that of concrete, it is ideally suited as reinforcement in tension areas of the structural member. Both of these properties help reinforcing steel work in unison with concrete to create a super building material that is strong in both compression (concrete) and tension (steel).