A one-of-a-kind water feature is a collaborative success
Under pressure
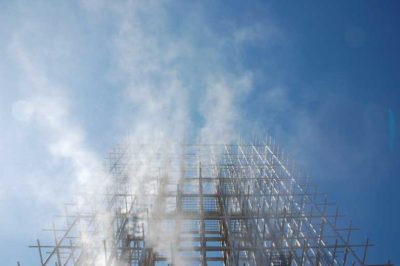
To produce the desired effect, the fog system operates at approximately 6895 kPa (1000 psi); therefore, the plumbing had to withstand this type of pressure. In this regard, only stainless steel braided hose rated for 17,236 kPa (2500 psi) and compression fittings with a pressure rating of 41,368 kPa (6000 psi) were used.
During the winter, when the ice system is operable, a significant amount of ice forms on the drip cables, which eventually comes crashing down to the base of the structure where all of the plumbing and lights are located. In fact, this happens every time a natural thaw event occurs. Therefore, to manage the falling ice, a grid was provided by the steel fabricator to break it up into smaller, less damaging pieces, while a special stainless steel-covered trough was constructed to protect the plumbing in the base of the water feature.
All of the braided hose used to plumb the water feature had to be ordered to exact lengths with adjustable ridged portions so it could be routed in an organized fashion to fit the troughs. They also had to be protected from chaffing within the structure, so Mariani Metal put a small radius on every opening the hoses pass through. Further, every valve and fitting had to be stainless steel to resist the aggressive nature of the reverse osmosis treated water.
Power down
Another major concern was figuring out how to protect the plumbing from freezing in the event of a power failure, as no backup generator was in the plan and draining the plumbing was complicated for a number of reasons. First, the elevation of the pit where the plumbing enters the Weather Catcher is lower than the equipment room. Therefore, it was not possible to simply let the water drain to the heated equipment area, as it would get trapped in the low spot at the base of the feature. Second, the individual nozzles for the fog and ice systems acted like check valves that could prevent the water from draining out of the plumbing system in a timely manner.
Therefore, three things were done to manage these challenges. First, a compressed air purge system, which can be controlled by the automation system, was incorporated into the design to evacuate the plumbing whenever a system shutdown occurred. For example, if the temperature were to drop toward 0 C (32 F), the rain system is stopped and high-pressure air, delivered through a solenoid valve, forces water out of the system. Instead of relying entirely on the purge system, a redundant system was also installed to ensure all of the water is removed.
This secondary system comprises a ‘solenoid dump box,’ designed collaboratively with Atomizing Systems, which allows the plumbing lines in the water feature, as well as the lines between the equipment room and the low point, to drain completely.
The solenoids have 120V coils to avoid any low-voltage drop, and are normally open (energized to close) so if there is a power failure, the valves would fail to the open position, allowing the system to drain. The fog system was one exception to this in that a normally closed valve had to be used in the dump box because of the pressure involved. So in the event of a power failure, this valve would remain closed and could potentially trap water. As a failsafe, a normally open valve was installed in the air-feed line to the fog purge system. If the power is unexpectedly lost, this air valve fails open and delivers the entire contents of the compressed air system to the fog system to remove all water.
Resolving one problem leads to another
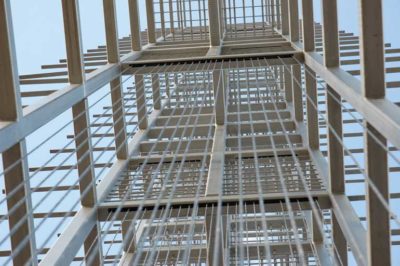
Although the compressed air system resolved one problem, it created another. The ice drip manifolds comprise several low-volume nozzles that are extended to make contact with the stainless steel ‘substrate’ cables (as described earlier) using small 6.35-mm (0.25-in.) poly tubing. This system worked great until it went through a compressed air purge cycle, as surges—created by the intermittent flow of water and air—dislodged the tube extensions from touching the cables. In fact, this was quite disruptive to the system as a significant number of interfaces between the nozzle and cable were lost after each purge cycle.
As it turned out, the resolution to this dilemma was quite simple. To prevent the tube extensions from being dislodged, they were merely anchored using stainless steel aircraft safety wire by twisting it around the cable and inserting it into the poly tubing. When the surging air and water tries to move the tubing around, the wire insert anchors the tubing in place.
The heat is on
Heat tracing was required because the water velocity in the system is so low it could potentially freeze at low temperatures even though it is moving. The status of the heat tracing system also needed to be known for decision-making purposes. For instance, if the heat trace is not working, the water should not be turned on.
Current transformers were added to the design and installed on each heat trace branch to constantly measure the current flow to the heat tracing for each system. If the current drops below a baseline level, the system will not run and an alarm is sent to the HMI as well as operator tablets, which can be used to control and monitor the Weather Catcher remotely. If the heat trace fails during operation, the system automatically shuts down and generates a purge cycle of the affected system. After the purge cycle is complete, the ‘dump’ solenoids in the pit open, and remain open until the issue is corrected.