Installation procedures
Once the design stage is complete, construction can commence. By this stage, the facility’s opening date should be set and the construction schedule created working in reverse from this date. The installer and general contractor’s timelines will be dependent on the manufacturer’s delivery of product, so it is imperative to understand their lead times and shipping schedule up front.
Work crews should also be selected at this point, with each designated a set of responsibilities for different aspects of the project. Prior to project initiation, it is in the contractor’s and project owner’s best interest to hold a preliminary meeting to clarify key roles and responsibilities. It is also a good time to review the construction drawings to ensure there are no missing items that could result in unexpected expenses or time delays.
It is imperative the contractor understands the unique parameters surrounding the project, as each installation has its own set of variables that will affect construction and the end result.
The manufacturer will provide preliminary drawings, but these are typically ‘not for construction,’ as they are based on general experience and rules of thumb with no consideration for the site-specific requirements. The contractor should work from engineer-approved and stamped drawings. Skipping this step could result in unforeseen challenges and greater expense down the road, while also negating any upfront cost savings.
For example, it is important to ensure adequate space is allocated for the overspray zone, which comprises a 2.4- to 3-m (8- to 10-ft) concrete strip that extends beyond the wet deck of the pad. This design element is often overlooked or cut out by a contractor to save money; however, an inadequate overspray zone can result in unnecessary costly maintenance. On windy days, water will travel off of the pad and land on surrounding vegetation. This can cause grass clippings, mud and debris to enter the pad and possibly clog strainers, drains and nozzles, while potentially ruining expensive landscaping.
Ensuring the contractor fully understands the importance of the overspray zone will help the installation succeed.
“I have certainly heard of work being demolished and redone due to lack of appropriate approvals and inspections,” says Perkins. “If in doubt, ask the local jurisdictions what is required.”
While the general contractor may or may not play an active role in the actual completion of the project, they will oversee the entire project through each stage, including:
- slope preparation;
- pipe trenching;
- footing layouts and sub aggregate compaction; and
- concrete pouring and backfilling.
The contractor is also responsible for scheduling and co-ordinating appropriate subcontractors and other experts to ensure the project stays on track. Some common subcontractors that are involved in aquatic play pad construction include concrete contractors, plumbers, pool contractors and electricians.
Concrete contractor
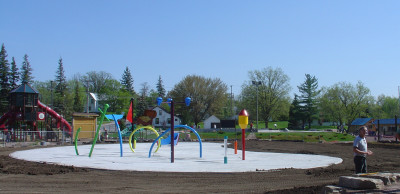
The concrete contractor is typically responsible for the creation of footings, rebar placement and pouring the concrete slab to the specified slope once all underground pipelines are completed. The contractor should also produce a proposed sample of the final concrete finish to the owner. While a light broom finish is typically suggested, this can be interpreted differently. Therefore, it is important to ensure the finish is not too slippery or abrasive for children’s feet. If coloured concrete is used, they will be responsible for creating the colour mixes as well.