Aluminum framing materials offer many advantages for aquatic venues
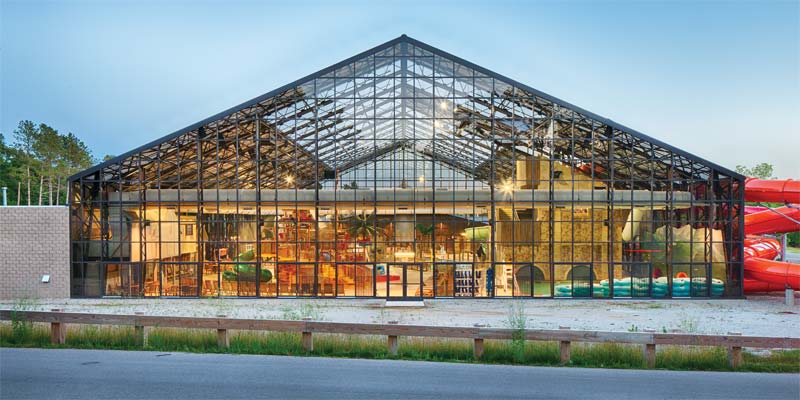
To streamline the planning process for venue owners, a good firm will already have experts on staff from all of these professions who are ready to design and build an indoor aquatic park with a retractable enclosure. These firms also provide dedicated project managers for each job, along with a team of in-house architects, engineers and suppliers who are capable of custom designing and fabricating a retractable enclosure.
The team starts by consulting with the venue owners and managers to determine the project’s precise goals and specifications through the stages of concept, schematic design, design/development and, finally, construction/shop drawings. As soon as the shop drawings for an enclosure have been approved, the project manager starts the production process, including fabrication sheets for each and every component that will be fabricated for the retractable enclosure. During this process, the project manager and fabrication team can take advantage of 3D design software to model and test each component virtually before sending them to the production line. Once a design reaches the manufacturing centre, the fabrication process can be completed quickly and precisely using advanced computer numeric control (CNC) machining tools. A CNC machine then fabricates the design in aluminum alloys, performing routing, drilling, tapping, thread milling, notching, sawing, and many other operations efficiently and economically. Afterwards, professional welders who are specifically trained and certified to work with aluminum weld the components together to complete the assembly.
Once the structure’s components are built and have passed inspection, they are shipped to the building site. Here, an experienced team of installers assemble each component according to the approved shop drawings. The result is a fast and highly accurate installation process that keeps the project on schedule.
Throughout the design, engineering, and manufacturing processes, quality control professionals, third-party inspectors, independent welding engineer consultants, and other professional inspectors ensure all components are compliant with local and international standards. If the construction team includes experienced, skilled installers, a project can be completed on schedule. Further, facility owners can be assured the retractable enclosure will fit the project specifications precisely.
Quality design and engineering
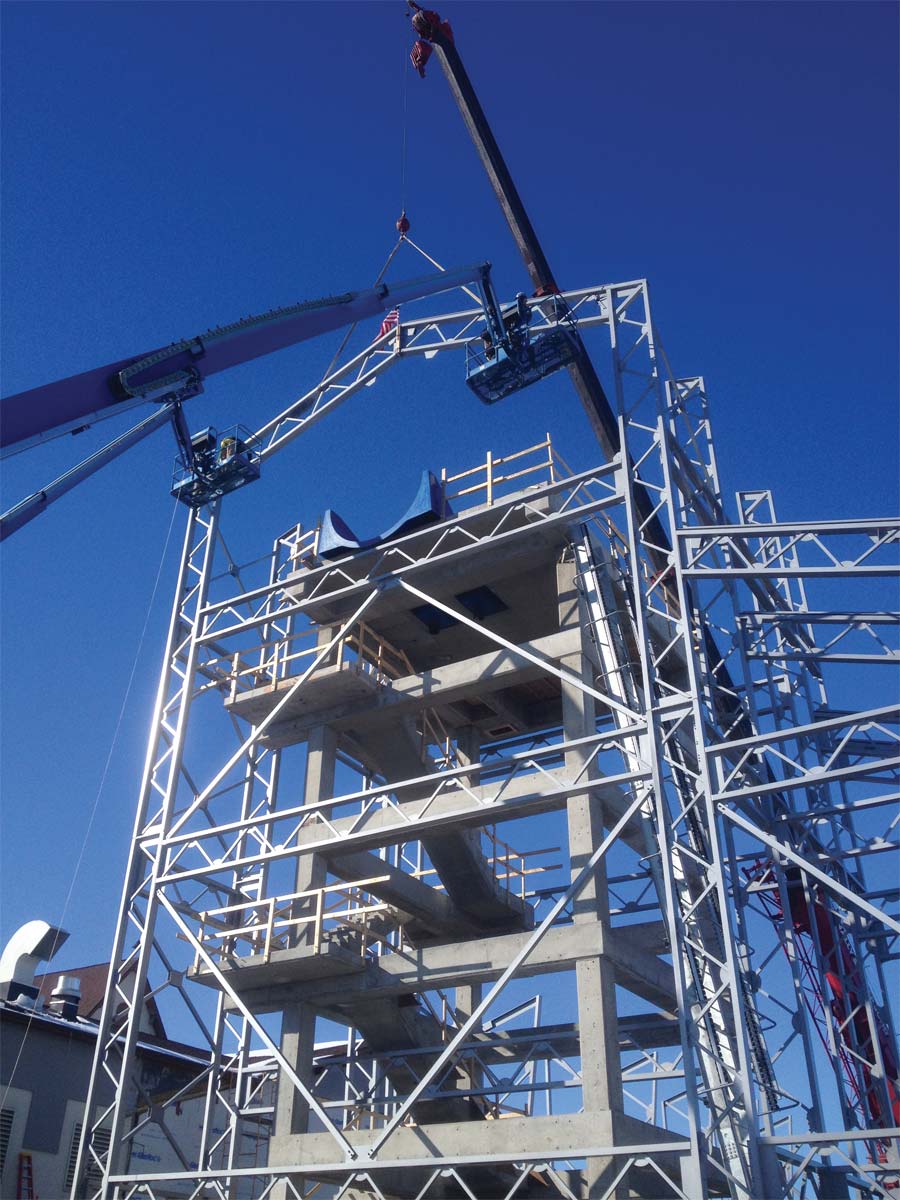
Aquatic facility enclosures with retractable roofs are built with materials to meet today’s architectural standards. To make a client’s retractable roof structure a reality, architects rely on a proven, effective design and construction technique. This involves the use of non-ferrous thermally broken aluminum for framing structures; glazing consisting of polycarbonate (PC), insulated glass, or ethylene tetrafluoroethylene (ETFE), custom motorized roof components; and other design and fabrication technologies that can be adapted for almost any location or climate. These specialized design and engineering methods have not only produced some of the world’s most impressive structures for aquatic venues, they have often done so with lower-maintenance costs than the industry average.
The heart of the design is a thermally broken aluminum frame. This material offers many benefits over traditional steel construction: it is lighter in weight and can be easily shaped for custom designs, yet it offers comparable strength and durability. These properties reduce the load of the enclosure or skylight on existing structures, giving the planning team flexibility when designing projects with long spans for a more expansive atmosphere. Aluminum alloys have been used successfully on retractable enclosures of many sizes—from local pools and recreation centres to some of the world’s largest waterparks.
Thermal breaks within the aluminum frame are important to prevent the transfer of exterior cold air through the frame where it can mix with the warm interior air and form condensation. Exterior metal is separated from the interior metal by a neoprene spacer to form this ‘break.’
While this break is critical for all aluminum frame designs, it is especially important for aquatic facility enclosures due to the warmer than usual atmosphere of an indoor pool. The air temperature in an enclosed pool must be kept two degrees warmer than the water, which creates a greater temperature difference between the inside and outside air temperatures. As such, it is important to not only have a thermally broken aluminum frame, but the entire enclosure envelope should consist of a thermally broken design. Further, an interior and exterior skin separated by a 25-mm (1-in.) thick rigid core should be used to form an insulating panel at all transitions rather than a single piece of sheet metal. Transitional areas include: where the enclosure changes direction from the slope to the vertical at the eave; at a jamb condition from slope to gable end; or against an adjacent structure.
Aluminum alloy 6061 T6 and 6063 T5/T6 are commonly used in the construction of retractable enclosures and skylights as they can be created to meet specifications for many different designs. Pure aluminum is too soft and reactive to be used in architectural applications.
According to industrial standards, aluminum alloys with a numeric code beginning with six possess far greater strength and durability. The ‘T6’ suffix denotes a higher temper (hardness) than average, which is obtained with heat treatment and artificial aging, making the alloy well-suited for commercial architecture. Many metallurgy experts say 6061 T6 aluminum has a high strength-to-weight ratio, “making it ideal for large parts that need to be very light.”