Automatic chemical controllers
Evolution of the chemical controller
Automatic chemical controller technology has evolved considerably over the past 40 years. They started as very large analog units that were not very accurate, susceptible to the aggressive pump room environment and in need of constant calibration.
Today’s microprocessor-based controllers, however, are quite different and have revolutionized pump room automation by offering facility operators new benefits, as well as improved reliability and accuracy. This technology has allowed manufacturers to add self-calibrating capabilities, along with user-programmable options to help maintain healthy pool water.
Additional inputs and outputs were added in conjunction with the microprocessor, which extended the controller’s capabilities far beyond its original duties. To further assist commercial pool operators, these devices are now equipped with the following features:
- Over-feed timers, which protect against over-shooting pH and sanitizer levels;
- pH priority, which protects new plaster or gunite applications during the curing process;
- pH and ORP high/low alarms, which protect bathers from unsafe water conditions;
- True free chlorine readings;
- Conductivity sensors, which measure total dissolved solids (TDS) or salt concentration;
- The ability to turn on/off salt chlorine generators;
- Water level control;
- Litres/gallons per minute (lpm/gpm) flow rate sensing;
- Water temperature control, with the ability to turn a heater on/off;
- Backup chlorination with secondary set-points for use in any application, especially salt chlorine generation;
- Auto backwash;
- Solution tank level sensing, with alarms;
- Safety vacuum release system (SVRS) alarm sensing;
- Alternative sanitizer control (e.g. supplemental systems, such as ultraviolet [UV] and ozone technology);
- Langelier Saturation Index (LSI) calculations;
- Pump room flooding sensors with alarm and protection; and
- Remote alarm notifications for all statuses.
One of the most important advancements microprocessor technology has given automatic chemical controllers is the ability to communicate with external peripherals and personal computer interfaces.

First-generation chemical controllers were equipped with digital communication capabilities limited to data ports with telephone or local area network (LAN) lines. This enabled the controller to communicate with a computer using designated software, which allowed users to download water chemistry parameters and other readings to their computers for logging purposes. Installing telephone and/or LAN lines in a commercial pump room was not always an easy task, while keeping software updated was difficult due to the rapid changes in applications.
As the communication industry advanced, so did automatic chemical controller technology. Today, pool operators and service companies can communicate with these devices via a variety of wireless protocols (e.g. cellphones, wireless network [Wi-Fi] and satellite), thus eliminating the need for telephone and/or LAN line installations.
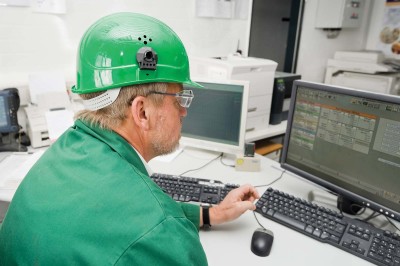
Wireless communication has further reinforced the importance of automatic chemical controllers in the pool industry, as it gives the pump room a ‘voice.’ With the addition of web-based software applications, which eliminate the need to install/update software on individual computers, these technologies allow anyone to monitor water chemistry and other important parameters from any computer terminal in the world, simply by typing in a designated user name and password.
Newer controllers can also be programmed to automatically send remote alarm notifications to any e-mail or cellphone to notify an operator of a chemistry-related issue or operating problem.
The job of today’s automated chemical controllers is progressing from pH and ORP control and slowly migrating into full pump room monitoring, operation and communication. This progression will allow facility operators and swimming pool service companies to be more proactive and efficient while maintaining safe, healthy swimming pool water.
M. Troy McGinty is the water quality management consultant, Poolcomm administrator and product instructor for Hayward Commercial. He is a Certified Pool Operator/Instructor (CPOI), Aquatic Facility Operator (AFO) and has led numerous seminars and training sessions across North America on the topic of pH and ORP automation, communication and business development. He can be reached via e-mail at mtmcginty@haywardnet.com.