Pool plaster finishes
Pool plaster finishes are simply a mixture of cement, aggregate, and water that is applied to the pool substrate via trowel. Depending on the finish, the thickness of the application will vary between 9.5 and 19 mm (0.375 and 0.75 in.). It is applied by a team of skilled workers (between five to eight or more depending on the pool size). It is important not to be understaffed with qualified applicators during the process. If this happens, the likely result will be a pool finish where the aggregates are not compacted properly, making it more susceptible to chemical wear and tear. These finishes are applied in an uncontrolled environment of wind, sun, heat, cold, or potential rainfall; therefore, it is advantageous to erect a tent over top of the pool prior to application should weather be a concern.
As plaster finishes are constantly submerged in water it means they will be exposed to water conditions which vary over time, more so if the pool is improperly maintained. This unavoidable interaction between the pool finish and water will, over time, likely result in a change of its appearance. Therefore, maintaining balanced water will greatly increase the life of the pool surface. Poorly maintained water will cause the finish to deteriorate slowly, potentially causing unsightly discolouration, roughness or, in rare cases, compromise the finish.
Marbelite (marcite)
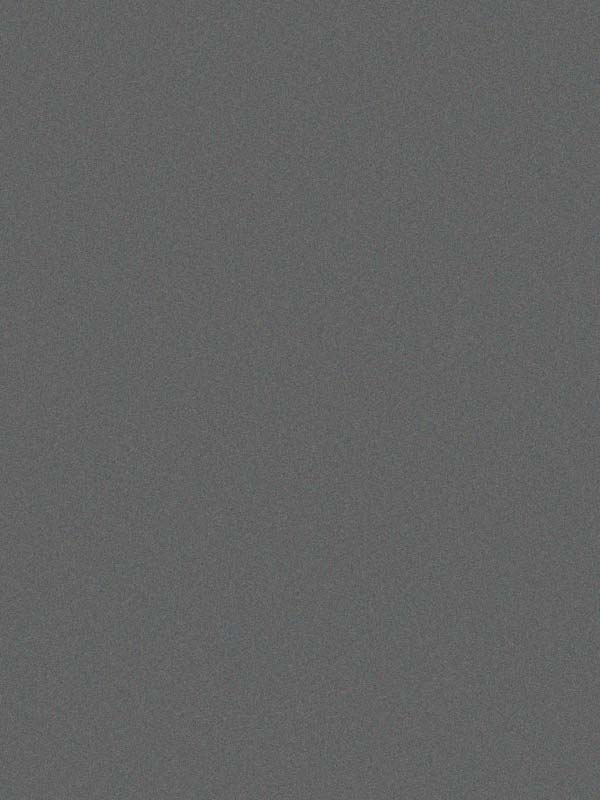
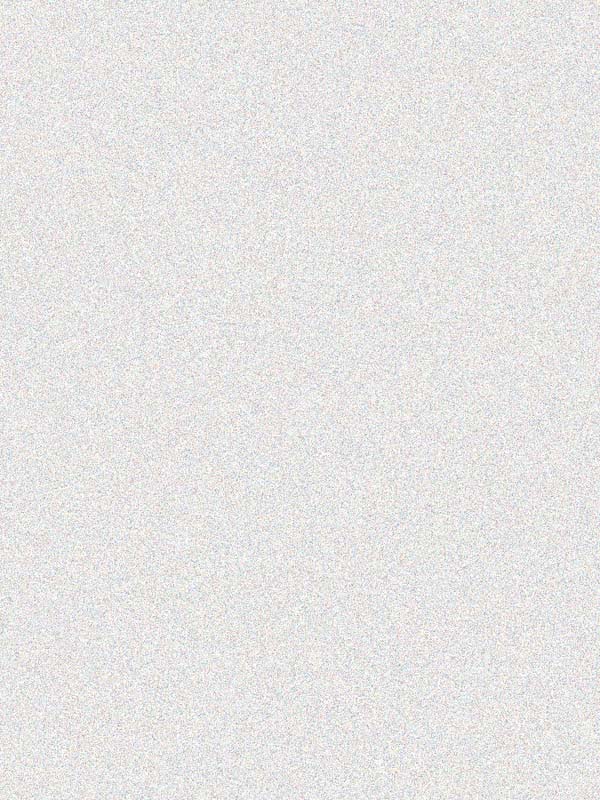
Marbelite (marcite) is the most economical of pool finishes. Standard white marbelite is a simple mixture of two-part white marble dust aggregate, one-part white cement, and water mixed together in a mortar or drill mixer for a minimum of six minutes to a consistency of a thick milkshake.
This material is then applied to the pool substrate by hand or pneumatically sprayed by plaster pump to a thickness of 9.5 to 19 mm (0.375 and 0.75 in.). It is then trowelled to a smooth texture, smoother than 220 grit sand cloth. It is considered the smoothest of all other finishes and creates a crisp, clean baby-blue appearance. It is a reliable product when properly maintained and applied by a quality plaster company. Marble dust aggregate is characteristically soft in nature, so in an effort to strengthen the density and longevity of the product, silica (quartz) coloured aggregates can be used as a replacement for a percentage of the marble dust in the mix ratios to enhance its look and durability. The use of pozzolans and silicone chemistry additives can also be integrated into the mix for the purpose of reinforcing the cement and binding the aggregates together. These additives have been proven to help minimize problems with the pool finish caused by fluctuating water chemistry over long periods.
Coloured marbelite (marcite)
When adding pigments to white marbelite, many different shades can be achieved to satisfy the homeowner’s preferences. However, it is important to note, coloured marbelite finishes are naturally mottled (marbled) in appearance. Darker shades like black or grey have the greatest contrast to the white mottling, compared to lighter colour tones such as blue or teal; therefore, the client should be educated on this prior to the application. This way they know it is a normal product characteristic and not a deficiency. Many homeowners embrace the mottled effect, as it adds character to their backyard theme.
Quartz exposed finishes
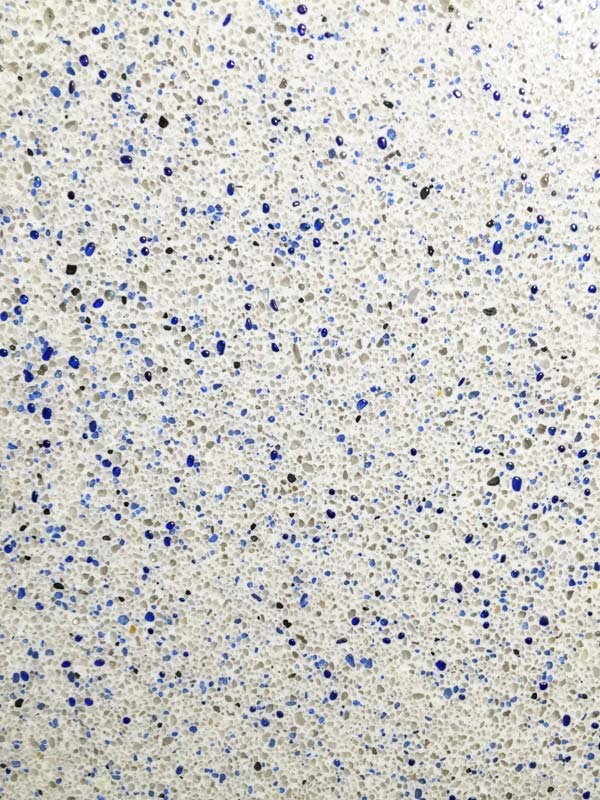
Quartz finishes are similar to that of marbelite when it comes to how it is mixed and applied. That said, there are a few differences in terms of the type of aggregate used and the final steps of exposure to create a uniformly exposed durable, dynamic, quartz finish. Often referred as a commercial-grade finish option, exposed quartz is often specified for use in waterparks, gyms, hotels, and recreational centres because of its resistance to fluctuating water balances.
Many homeowners have been selecting this option for their pools because of its appearance and durability; however, it does not come without an increased cost. The advantages of an exposed quartz finish is that it comprises a durable 100 per cent quartz (silica), not marble dust aggregate and white cement, which is applied to the pool walls and floor at a thickness of 9.5 to 19 mm (0.375 and 0.75 in.) and trowelled smooth similar to marbelite finishes. The next step, after the product has hardened, is the exposure process which involves removing the paper-thin cement cream which was left at the top of the surface. The temperature during application will dictate when the exposure can begin, as premature exposure of the top cement cream in cooler temperatures will result in unsightly overexposed areas.
Types of exposure methods include water washing (with brushes and water the same day as it is applied), or acid washing the finish the next day. Water washing the same day will achieve the best consistent results compared to acid washing the finish the day after, once the cement cream has hardened.
The added advantage of exposed quartz is if the customer selects a coloured finish, mottling (marbling) is drastically reduced or eliminated since the cement cream that exhibits the mottling is removed.
I didn’t realize that concrete pools are considered “the Cadillac” of pools. Since it is one of the best ways to get a natural looking finish, this is the style I would want for my pool. We have plenty of space in our yard to have a pool installed, we just need to work out the budget and start contacting contractors. http://diamentisteel.com/services.html
Great information. This is one of the best blog I had ever read. Keep doing this amazing work.