Thermal bonding
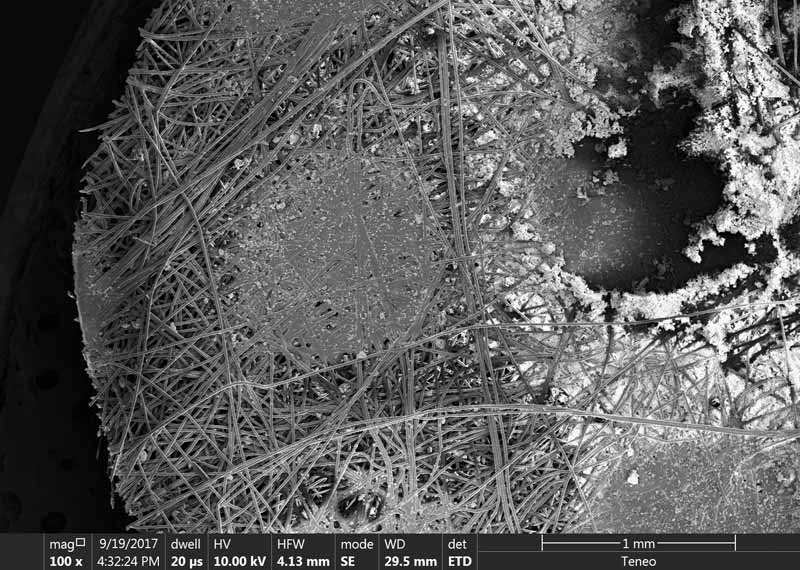
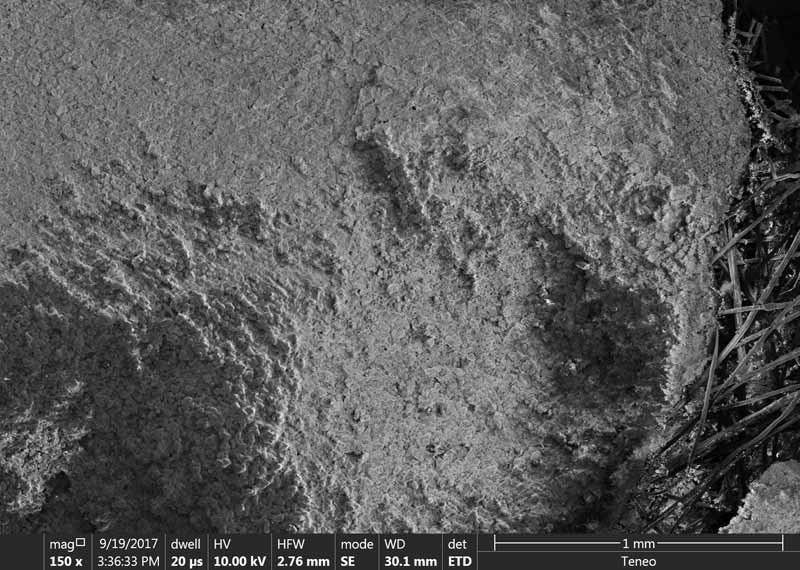
This fabric comprises low-melting thermoplastic fibres that can be thermally bonded to consolidate the web. There are four different ways thermal bonding can be performed, including:
- Calendaring or embossing—The heated web is squeezed between two rolls (smooth or patterned) which forces intimate contact of the molten fibres with other fibres in the web. Often the calendar rolls are heated; if the rolls are smooth, the web is uniformly bonded. If the rolls are patterned, an embossed web results typically seen as a very even pattern of small points across the web.
- Air bonding—The web is thermally bonded by passing it through an air dryer or heater. The result is a bulkier and loftier media.
- Ultrasonic bonding—This is a relatively new technology that uses high-intensity energy to melt and form bonds from thermoplastic fibres.
- Hot melt bonding—The hot melt thermoplastic is extruded onto the web and, while still in the molten stage, it penetrates and bonds the web.
- Chemical bonding—A chemical binder agent or resin is used to bond the web.
The mechanics of a cartridge filter
Cartridge filters rely on the surface area of the filtration fabric, unlike a traditional sand-type filter, which relies on the diameter of the tank, as well as the depth of the sand bed. As water passes over a cartridge filter, it starts building a layer of dirt and debris on its surface, which is commonly referred to as filter cake. Over time, the filter cake continues to accumulate on the surface of the cartridge trapping smaller and smaller debris.
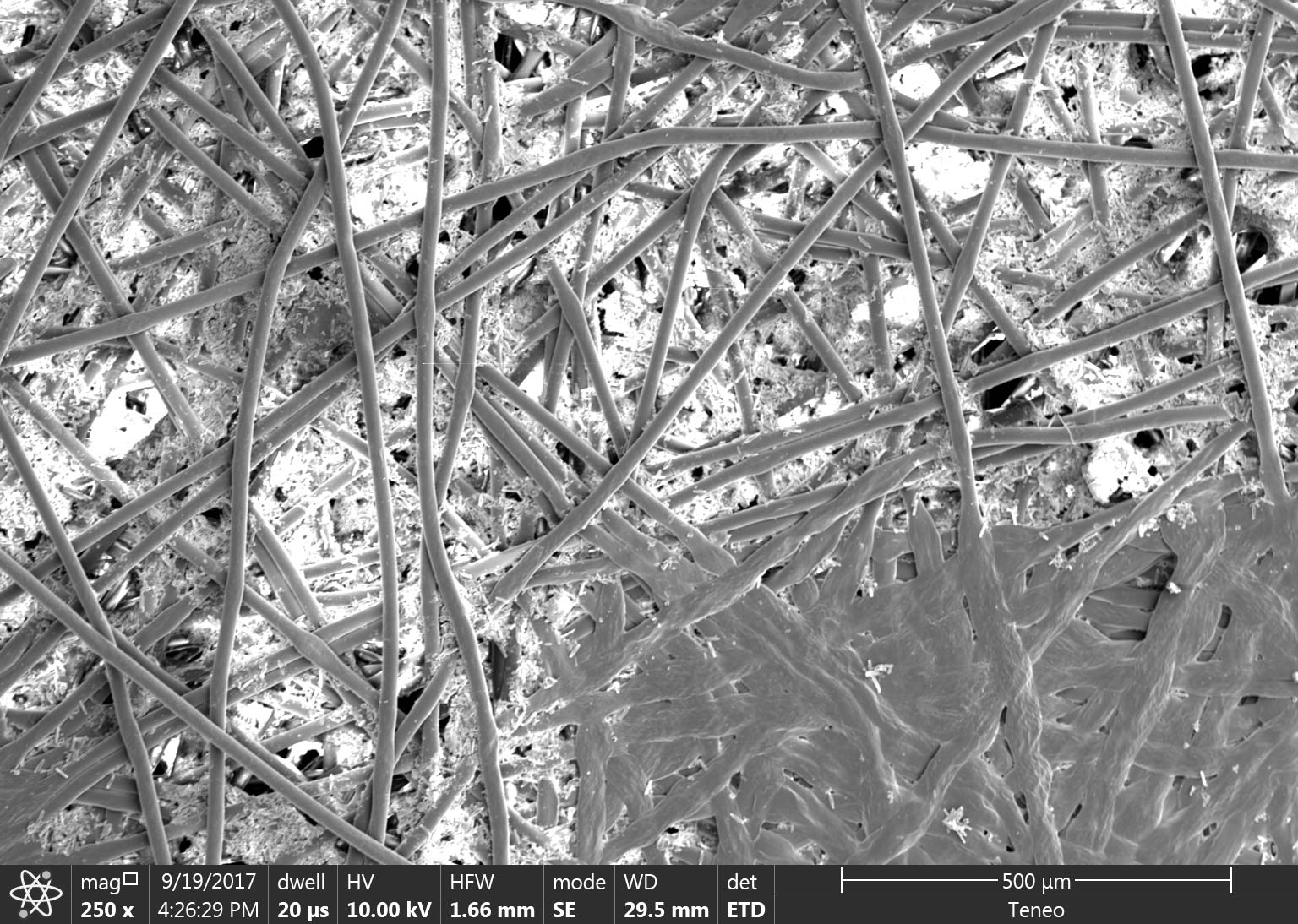
As the filter loads, the throughput (flow) of the system begins to diminish, resulting in an increase in pressure on the filter system. Field service technicians and end users monitor a pressure gauge on the filter tank to judge how far along the cleaning cycle is.
Drawing upon the different ways to manipulate a fabric during its formation, certain characteristics can be tweaked to improve the performance of a cartridge filter without creating a dramatic spike in the system’s operating pressure. Again, by reducing the diameter of a fibre, it can increase the number of fibres in a fabric. Smaller fibres offer more cross-over points, which creates finer pores in the fabric. Filter cake then begins to form on the fabric sooner. As mentioned, all polyester media must be bonded to ensure the fibres stay together. Through observation, a uniform bonding pattern also encourages the formation of a filter cake more so than randomly bonded fabrics. This has a positive impact on the cartridge’s dirt holding capacity, as the debris is more evenly distributed.
Regardless, there will always be smaller particles that become trapped in the depth of the fabric’s web and cannot be released from the filter, even after washing the cartridge. As the cartridge continues to provide service, a shorter operational cycle can be expected between washes than when the cartridge was originally installed.
These seasoned cartridges offer the benefit of finer filtration, albeit in shorter periods of use. Some service technicians prefer to use these older filters when vacuuming dead algae (smaller than 4 microns) from the pool or at the start of the pool season.
When is it time to clean the filter?
The industry rule of thumb is to clean/service the cartridge filter element after the system pressure increases by 8 psi; however, the U.S. Center for Disease Control (CDC) states: “A typical-use pool should have a pump and filtration system capable of pumping the entire contents of the pool through the filters every six hours.” This is generally interpreted as four turnovers per day to ensure the pool does not become cloudy or experience other water quality problems.
To maintain filter cleanliness, there has been a growing trend in the number of homeowners who use flow meters on their pools as a standard to determine when their filter needs to be cleaned. In some cases, an increase in pressure by 10 psi would still ensure four turnovers a day and a trouble-free pool; however, in some instances, an increase in pressure by 4 psi could result in less than four turnovers a day and a cloudy, problematic pool situation. This could always be balanced by plumbing modification and sizing the pool equipment correctly.