Flexible versus rigid coatings
Once the decision to use a deck coating system is made, there are additional factors to consider. The next decision, which will probably have the biggest impact on the end result, is whether a flexible or rigid coating system should be used.
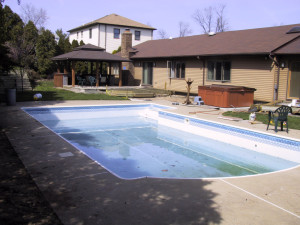
The major difference between the two types of coatings is cost. Rigid coatings are generally less expensive because they do not have as many polymers and additives in the product and are easier to clean. Flexible coatings, on the other hand, are able to ‘move’ with the substrate, providing some significant advantages.
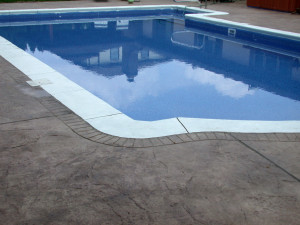
For example, the ability to bridge cracks, as mentioned earlier, is a huge advantage in terms of cosmetics, performance and protection. Flexible coatings also tend to have superior bonding characteristics over the rigid variety, which allows them to conform as the pool deck shifts and moves. Rigid coatings can potentially move in different ways, whereby causing delamination issues. Increased polymer content in flexible coatings also provides increased adhesion properties.
Certain flexible coatings with elongation rates of 50 per cent or greater can also be applied to wood substrates (i.e. decks). This is a unique advantage because it allows contractors to take an ordinary wooden deck and give it a completely different look and appeal for a fraction of the cost of tearing it out, pouring new concrete and either stamping or staining it.
Increase safety around the pool
By using different aggregates in deck coating systems it is possible to create surfaces with increased slip-resistant characteristics than plain concrete. This is an important consideration when selecting a deck coating system to help eliminate or reduce potential slip and fall accidents—especially on wet surfaces—which account for billions of dollars in injuries and insurance claims each year.
Slip resistance is measured by the American Society for Testing and Materials (ASTM) Standard C1028–Standard Test Method for Determining the Static Coefficient of Friction of Ceramic Tile and Other Like Surfaces by the Horizontal Dynamometer Pull-Meter Method and the Americans with Disabilities Act (ADA) guidelines, which recommend a coefficient of friction (COF) of 0.6 or higher in dry and wet conditions, and 0.8 on ramped surfaces, to provide safe surfaces for all people to traverse across. Slip-resistant characteristics are graded using a COF scalar value, which describes the ratio of force of friction between two bodies and the force pressing them together. These guidelines and local requirements should be evaluated when selecting a pool deck coating, especially since slips are more likely to occur where splashing and puddles are common.
There are various coating systems available today, which approach the solution in different ways.
Aggregates
Some deck coating systems (generally epoxy and urethane based) allow different sized aggregates to be broadcast into the coating’s surface, while it is still wet, to vary the degree of slip resistance. Other products, such as cement-based coatings, already have a mix of aggregates in the product. This allows applicators to select a coating system with varying degrees of slip resistance, such as ‘heavy duty,’ ‘regular,’ ‘fine,’ or ‘ultra fine’ to achieve the desired surface.
Both methods work, it is simply a matter of budget and preference of application, as broadcasting an aggregate is an additional step that requires more labour hours.