It is all about efficiency
In the past few years, some manufacturers have increased equipment efficiency by nearly 16 per cent, with efficiency measured as the moisture removal capacity per compressor kW input.
That said, there is efficient and then there is exceptionally efficient dehumidification equipment. The difference—some units may have low-energy-consuming components, while others also include operational strategies, which help further reduce energy consumption and costs.
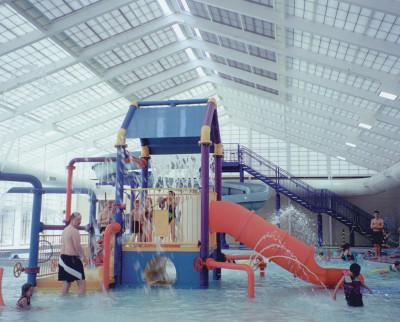
First and foremost, a mechanical dehumidification system must have the ability to recycle energy removed during the dehumidification process back to the pool water and air. A majority of indoor pools, regardless of their geographic location, require heating 70 to 90 per cent of the year. Selecting a system with a high-thermal coefficient of performance (COP) can satisfy dehumidification and heating, while almost eliminating fossil fuels for auxiliary heaters.
All new refrigerant-based equipment must now use R-134a and/or R-410A; the former is a high-temperature refrigerant, while the latter is used as a refrigerant in air conditioning applications and produces more cooling and dehumidifying capacity per kW. Both do not contribute to ozone depletion and are becoming more widely used. Older systems using R-22 refrigerant cannot be upgraded.
Large dehumidification equipment used for commercial operation and natatoriums must have ample cooling capacity to deliver moisture control and seasonal cooling. Efficient refrigeration systems operate using multiple compressors and allow multi-stage modulation to manage the electrical load. This feature yields maximum system efficiency and lifespan, while assuring the best quality indoor air and pool water conditions at the lowest cost.
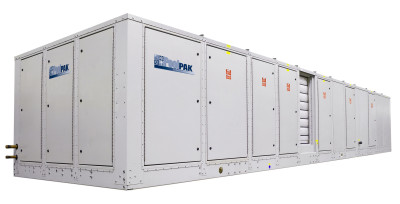
All dehumidification systems require blowers to circulate conditioned air and ventilation throughout the facility; however, not all blower motors are built alike, with some being expensive to operate. Equipment built to National Electrical Manufacturers Association’s (NEMA’s) standards for totally enclosed, fan-cooled (TEFC) motors are quite efficient, as they require less energy for equal loads and have a longer service life. Even the fan’s design can affect efficiency. For example, backward inclined airfoil-type fans (BIAF) move air more effectively, which also results in reduced energy requirements.
It is a little known fact that a properly operating dehumidification system can, in one year, remove an entire swimming pool worth of water from the air. As such, look for systems that can recycle extracted water back into the pool, thus saving the facility costs on water consumption.
Built for the pool environment
The discussion about dehumidification systems for indoor pool facilities would not be complete without touching on the equipment’s fabrication. The indoor pool environment is highly corrosive, as chloramine off-gassing attacks all metallic surfaces, causing corrosion. However, the use of high-performance coatings and copper parts and components help ensure the long equipment life. This, in turn, reduces the environmental impact caused by disposal.
Some manufacturers also powder coat the equipment’s sheet metal sections to meet or exceed U.S. and European standards for minimum volatile organic compounds (VOC) air pollution emissions. The coating process is an environmentally friendly commercial painting technology that protects sheet metal against the corrosive effects of highly concentrated chemical- and humidity-laden air. Critical components such as compressors should not be located in the corrosive air stream (the path through the dehumidification system where the facility’s supply and return of conditioned air travels, which more than likely contains chloramines), as this decreases life expectancy, reliability and uses more natural resources. Items like compressors, electrical components and actuators will eventually reduce in efficiency or fail prematurely. A dehumidification unit is not designed to remove chloramines, this must be controlled through proper water chemistry management.