Designing a ‘green’ therapy pool
Green aspects
Although therapy and long-term recovery were important considerations, sustainability and ‘green’ design parameters for long-term cost control also played a large role in the project’s design.
Heat and water management
The client’s home was converted from electric heat to a ground source conventional geothermal loop system, which, in conjunction with the wasted heat generated by the pool room HVAC system, is used to maintain the temperatures in the pools. This type of heating is ideal for indoor pool environments. Radiant geothermal in-floor heating was also installed in the pool deck.
All aspects of the HVAC system were fully engineered to handle the loads generated by an indoor pool of this nature. Waste water from the dehumidified air is captured from the HVAC system and returned to the pool system via the surge tank. This resulted in an interesting scenario whereby the pool actually gained water over time. As such, to monitor the water level, the pool was equipped with an auto-fill system connected to the surge tank.
The source water for the pool came directly from a well with low water quality. To avoid using this water, a secondary cistern for storing clean water trucked to the site was considered. Fortunately, however, the HVAC system generated more clean water than the pool required, resulting in the installation of a waste/overflow line being installed from the surge tank to the internal bunker drainage system.
Supplemental disinfection systems (SDSs), such as a copper ionizer and ultraviolet (UV) system, provide effective water treatment. By using these systems, the client only needs to periodically add a very small amount of chlorine to maintain the proper sanitizer level.
Insulation and waterproofing
Technically, the most energy-efficient pool can be compared to a vacuum thermos. Water and heat is contained and evaporation is eliminated. There are no pumps, water features or any fun and relaxation. In reality, however, pools are used, water features are added and covers are non-existent or not used efficiently.
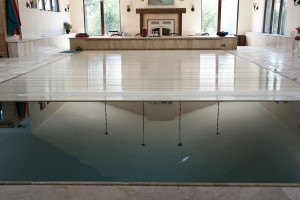
The first line of defence for any pool is to prevent heat and water from escaping to the surrounding environment. Insulation is the answer and, in all cases, the greater the temperature difference between the body of water and its surroundings, the more valuable it is. Pool owners located in northern climates see a quicker return on investment (ROI) when an automated cover is installed and the pool shell and plumbing are insulated.
For this particular project, the underground bunker was a fully engineered component of the pool, deck and building foundation. Constructed of cast-in-place concrete, the bunker’s walls, floor and roof were fully insulated with rigid foam. It wraps around the entire pool shell, separating it from the earth’s cool constant temperature (12.7 C [55 F]) via an air barrier. Comprising 125-m2 (1,350-sf), the bunker houses the pool’s mechanical equipment, electrical panels, automation system and HVAC and geothermal systems.
The therapy pool also has several layers of insulation (the walls, floor and plumbing are fully insulated) to help maintain and sustain the energy inputs (i.e. the heated water created by the geothermal and HVAC systems).
The floating, automated-slatted cover not only insulates the pool but also prevents heated water from evaporating into the atmosphere. Pool covers are critical to the long-term energy sustainability of an indoor pool.
Concrete is permeable and not waterproof; therefore, the pool shell interior, along with the pool deck, was coated with a combination waterproofing agent and pool interior finish to add to the water-saving aspects of the indoor pool environment. Unlike a conventional pool, however, the entire shell perimeter of this pool is visible because it is surrounded by the walk-around pool bunker, so any leaks would be highly visible.