Differentiating stains and determining treatment
Oxidation
Corrosion of metal components is an oxidation process. The most important corrosion related staining is from system components containing iron (Fe) or copper (Cu). When the metals in these components are in their elemental state (e.g. refined copper in a heat exchanger or processed iron in steel) they have an oxidation number of zero (Fe0 or Cu0).
Corrosion occurs when these metals are oxidized to a divalent state by an oxidizing agent present in the water, such as hypochlorous acid (HClO) or oxygen (O), yielding Fe2+ (ferrous ion) and Cu2+ (cupric ion):
Fe0 + oxidizer → Fe+2
Cu0 + oxidizer → Cu+2
These divalent ions are water soluble, meaning they will dissolve and dissociate into the pool upon oxidation. It is important to note that oxidation of system components is largely driven by oxidant concentration. Whether it is dissolved oxygen or hypochlorous acid, typical concentrations found in pools are very slow to oxidize copper from a heat exchanger or iron from a steel impeller. Normally, oxidation of such components is caused by improper water balance, which is discussed in the following section.
Alternatively, metals can enter a pool through source water or from products applied for treatments, such as copper-based algaecides. When dissolved in water, copper and iron are in a divalent state, as shown above. Incidentally, ferrous iron has the capacity to oxidize further to form trivalent ferric iron:
Fe+2 + oxidizer → Fe+3
The trivalent product of the reaction (Fe+3) is insoluble. As pools operate in slightly alkaline (AT) conditions, trivalent iron will react with excess hydroxides (OH−) in the water to form iron hydroxide precipitate, as shown below:
Fe+3 + 3 OH− → Fe(OH)3
Though divalent copper will not oxidize further, it too can undergo a similar reaction in alkaline conditions to form copper hydroxide (Cu[OH]2) precipitation:
Cu+2 + 2 OH− → Cu(OH)2
This is the reason why applications of alkaline products, such as calcium hypochlorite (Ca[ClO]2), bleach or even the byproducts of electrolytic chlorine generation tend to exhibit a greater oxidizing effect to create staining. Due to the high pH, such products create localized areas in the water that are high in hydroxide concentration. This relative increase in hydroxide accelerates the reaction rate that forms the metal hydroxide precipitate, which then creates surface staining.
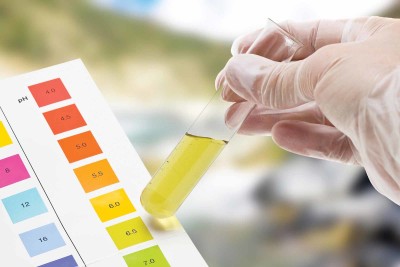
Another mechanism where oxidation can contribute to staining is through the interaction with metal containing products (e.g. copper-based algaecides). It has been established that elemental copper dissolved in water can react in alkaline conditions to cause surface stains. To help prevent this, some copper-based algaecides incorporate a chelating complex to inhibit the precipitation reaction. However, many chelants are themselves susceptible to hypochlorous acid oxidation. Once oxidized, they will degrade and eliminate the chelation effect on the copper. Once free, the copper is available to react to form staining. Common chelants, such as triethanolamine (C6H15NO3) and ethylenediaminetetraacetic acid (EDTA) contain nitrogenous (N) groups that will react with chlorine to form chloramines (NH2Cl).
Therefore, products that use these chelants are less effective at preventing copper staining. Alternatively, chlorine resistant chelants, such as polyacrylate are much more stable in a chlorine environment. They will not degrade under normal pool conditions and are more effective at preventing copper staining.