Evolution of pool filtration
By Bob Hawken
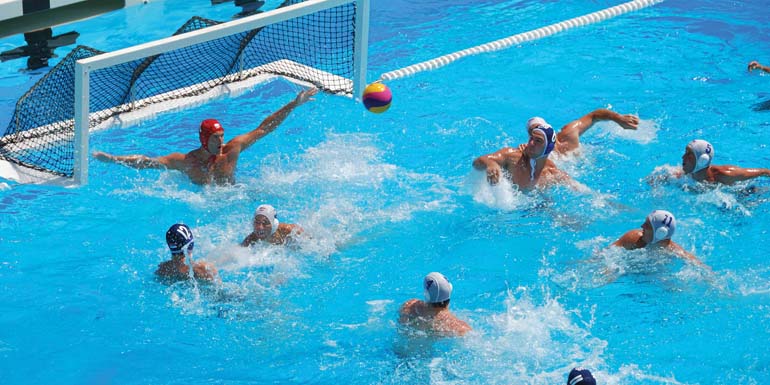
Commercial swimming pool filtration has evolved significantly over the past six decades, encompassing many changes in methods, materials and technology. Many earlier filtration systems were similar to what was used for municipal water treatment, as that was the prevalent knowledge at the time. Gravity sand filters and open-top vacuum diatomaceous earth (DE) filters were among the methods used. As the commercial and municipal pool market grew, filtration products were developed to better satisfy these needs.
A discussion about filtration systems can not take place without realizing the filter is but one major component of the overall recirculation system. The proper sizing of commercial pool filter(s) is done in concert with the sizing of the other components in the system, such as piping, pumps, etc.
First, however, it should be determined what type of pool a filtration system is going to be used on. Over the years, many engineering changes have been made with regards to sizing a recirculation system. Most of these changes were made in conjunction with health department codes governing commercial swimming pool design.
Older commercial and municipal pools typically had one body of water, which was mainly used for recreational swimming. In most cases, these were large bodies of water that incorporated one filter/recirculation system, with the entire water volume being recirculated approximately every eight hours.
As the industry progressed, facilities were built with multiple pools to satisfy different needs for various water activities, e.g. competition and toddler pools, as well as whirlpools. Each new development required modifications to the size of the recirculation system, as well as turnover rates.
Challenging filtration needs
Today’s aquatic facilities are more challenging than ever, with the incorporation of lap, activity and slide pools, as well as lazy rivers and splash pads. A recirculation system for a competition/lap pool should be sized to provide a six-hour turnover rate, whereas the recirculation system for an activity pool or lazy river should provide a one to one-and-a-half hour turnover rate. Although the water volume in an activity pool may be less than a competition pool, filters, pumps and piping may be designed larger due to the faster turnover rate required.
The early years of the waterpark industry provide a great example of how recirculation system design has evolved. Most original waterparks were built with a common filter plant to handle the filtration needs for all bodies of water. However, operators soon realized this was not the best way to design a waterpark, as inconsistencies with water and bather volumes in the different pools gave rise to water clarity and sanitation issues. Also, if there was a fecal accident in one pool, the entire park was at risk. As such, waterpark design parameters were improved to provide a separate filter/recirculation/sanitation system for each body of water.
Sand filters: An early favourite
As design parameters in the industry improved, sand filters were the product of choice for most facilities. They progressed from earlier rapid-rate filters, which had a 7.33-m3/hr/m2 (258.8-cf/hr/sf) maximum filtration rate, to current day high-rate sand filters, which offer a 48.89-m3/hr/m2 (1,726.5-cf/hr/sf) maximum filtration rate. (The filter rate is the velocity at which water passes through the filter media.)
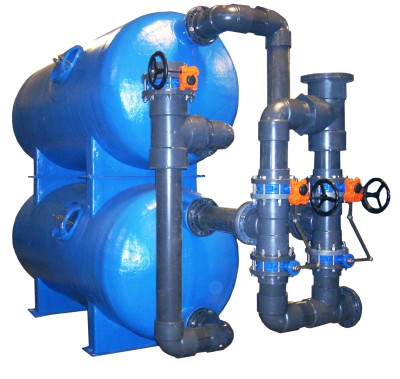
High-rate sand filtration works on the premise of bed depth penetration; the faster the filter rate, the further the particulates will be driven into the sand bed. Vertical sand filters have a deeper sand bed than horizontal sand filters, so a higher filter rate can be utilized.
Most sand filters are National Sanitation Foundation (NSF) listed up to 48.89 m³/hr/m² (1,727 cf/hr/sf); however, this is the maximum. Good design practices (and most health department codes) limit this rate to 36.67 m³/hr/m² (1,295 cf/hr/sf). As horizontal sand filters have a shallow media bed depth, the target filtration rate is between 24.44 to 29.33 m³/hr/m² (863 to 1,036 cf/hr/sf).
As pool design and engineering requirements changed over the years, filter manufacturers responded to accommodate the new challenges by offering sand filters in different configurations, sizes and materials.
Larger bodies of water and faster turnover rates required larger filters, which also meant bigger equipment rooms. As construction costs increased, mechanical room space was at a premium; multi-cell sand filters were developed to overcome this challenge. These are single-tank units, which incorporate two to three filter cells within the tank. This doubled or tripled the basic filter area without increasing the footprint required in the equipment room.
Horizontal sand filters were also used to increase filter area in a smaller space, as a cylinder on its side provides a far greater filtration area than a vertical-oriented cylinder. Horizontal filters can also be stacked in pairs, which allows the filtration area to be doubled without increasing space requirements in the filter room.