Fabricating safety covers
Decks
Decks do not seem like they would factor heavily on safety cover design, but they do. In fact, almost every cover is dependent on the deck to tightly secure them in place all winter.
At one point, pool decks were almost always constructed of poured concrete and were a standard 1 m (3 ft) around the pool’s perimeter. Today, however, decks are built using various mediums—from concrete to interlock and then garden space.
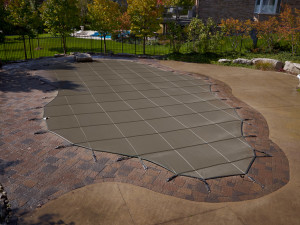
It is important to know about any deck discrepancies to ensure the safety cover is designed with the proper anchoring system. Standard 76-mm (3-in.) concrete anchors cannot be used on decks comprising interlock brick or loose stone, and paver rods are not optimally effective in garden beds or sod. Each strap placement can also vary on the pool surrounding. For instance, designers will limit the number of straps going into a garden as this can become a potential weak point in the cover.
Noting the deck’s width is also important. Unless otherwise stated, most manufacturers will design their covers to have a standard amount of overlap—typically 305 to 406 mm (12 to 16 in.) around the entire pool perimeter. Once adding a 152-mm (6-in.) spring, 102- to 152-mm (4- to 6-in.) strap, and a couple of inches to drill the anchor, installers will find themselves approximately 0.76 to 0.8 m (2.5 to 2.6 ft) away from the pool’s edge. In some cases, this can be problematic if the deck is only 0.6 m (2 ft) as the cover will need to go back to the manufacturer for alterations.
In situations where the width of the deck varies, there are a few design methods commonly used to ensure the cover fits properly. In most cases, the cover’s overlap can be reduced, shorter springs can be used, and in some situations, special rings can be sewn onto the cover.
Rocks, waterfalls and walls
Jump (i.e. dive) rocks are the most common obstruction safety cover manufacturers face today. These rocks are typically incorporated into the deck in the pool’s deep end. Depending on the pool’s design, these rocks vary in depth, height, and triangulation (i.e. location). As stated previously, if the design team is not aware of the rock, nothing will be done to avoid it.
Once the rock’s location and angle is determined, a proper cut out will be incorporated into the cover design to ensure it fits snug around the rock face. Some manufacturers also sew a plush vinyl bumper around this area to plug up any gaps that may exist.
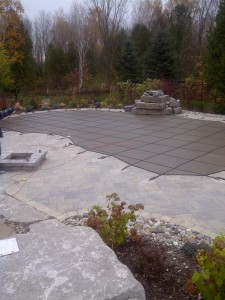
In most cases, safety cover manufacturers also try to avoid the need for installers to drill and install anchor points into smaller rock faces. It is appreciated that many pool owners do not like the look of a bold, stainless-steel anchor drilled into these features. Further, all rocks are not equal and some could crumble or crack under the pressure of a hammer drill. Anchor points, however, will need to be installed on waterfalls typically every 0.45 m (1.5 ft).
Manufacturers also need to know exactly where every obstruction starts and stops along the pool’s perimeter as the goal with every cover is to eliminate potential gaps or open areas. If measurements are off, the cutout may be too big (allowing for gaps) or even worse, too small, which would force the cutout to bunch up on the obstruction.