Fabricating safety covers
Appendages
It is also essential to let the cover manufacturer know if there are any appendages (e.g. steps and/or spill-over spas) outside of the main pool body, which also need to be covered.
Here, simple start and stop points may not provide enough information as these features are available in many different sizes and shapes.
The most common pool steps are French curve and rounded Roman. If the manufacturer is not aware the pool incorporates one of these types of steps they may in turn design the cover to include a square flap as opposed to it being fitted. In these cases, the step flap will be too large and may not even fit on the deck; therefore, A/B triangulation or measuring the entire perimeter of the steps with the rest of the pool is recommended. This will notify the manufacturer whether to trim or square off the cover’s corners.
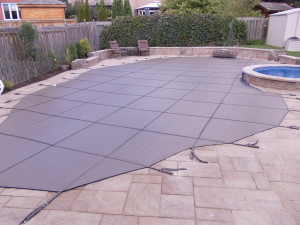
When it comes to spas and spill-overs, it is important to measure their diameter as well as their height. Not knowing the spa’s height can be problematic for cover designers as they may think the spa is flush with the pool and nothing further is required.
Many spas are now raised—even a few inches—and must be treated differently by manufacturers. For example, even a spa that is slightly raised will require a few inches of extra material to be added to the length of the appendage to ensure there is enough at the back end, allowing the cover to be fastened to the deck. If nothing is done to account for the raise of the spa, there will be gaps around the perimeter of the back end. Further, if the height is more than 152 mm (6 in.) most manufacturers will sew diagonal darts (folds sewn into fabric to help provide a three-dimensional shape) on the side of the appendage cover to pull it down to deck level.
Standing up to wear and tear
Smooth aluminum coping systems are not intrusive and should not harm a safety cover. However, some design techniques used today, which involves using abrasive flagstone and/or rock/brick capping to cover the pool’s coping, can destroy a safety cover over the course of its first year.
Also, under the weight of snow, water and/or debris, a safety cover is pulled into the centre of the pool. Once the weight is relinquished, the cover is pulled back tightly onto the deck. Although safety covers are designed for this, constant movement can become burdensome; therefore, manufacturers try their best to protect the cover by sewing specially designed plastic rub strips on the underside of every perimeter-based strap. These rub strips safeguard the cover’s straps and stitching; however, they do nothing to protect other areas of the cover, which drag on the deck. Therefore, on projects that have a rough deck and/or coping, manufacturers can sew vinyl padding on the bottom of the entire safety cover to absorb the abrasiveness of the deck. Initially it may be more expensive, but it will pay for itself several times over by adding many years of life to the safety cover.
Installations made easier
As one can see, designing and manufacturing safety covers has changed significantly. As part of this evolution, most manufacturers offer technical support via phone to assist builders with measuring and/or installing safety covers, and, in many cases, they also offer onsite assistance where trained personnel and/or field representatives meet with builders/installers to assist on extraordinary projects. Finally, there are also dedicated companies available, which focus strictly on measuring and installing safety covers.
Leigh Hinsperger is the Canadian sales and marketing director for Hinspergers Poly Industries Ltd., manufacturers of Yard Guard swimming pool safety covers in Mississauga, Ont. He has held this position for 10 years and has extensive knowledge in safety cover manufacturing and installation. Hinsperger can be reached via e-mail at hinsperg05@hinspergers.com.