Benefits of using heating system booster pumps
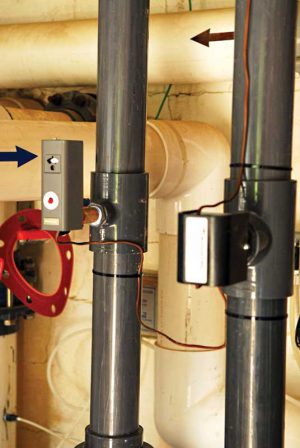
For example, the installation and operation manual of a pool heater may specify that no more than 4.5 m (15 ft) of developed pipe length can be accommodated. Some installers may use no more than 4.5 m of pipe, but when elbows and fittings are accounted for, the real head pressure of the loop equals about 18 m (60 ft) of developed pipe. In a real-world application, it is difficult to fall within manufacturer specifications when the pump is supplied with the heating unit. The manual rarely reflects a real-world application.
Custom solution
The author’s company customizes all their systems by hydraulically separating the filtration loop from the heating appliance loop and accurately sizing the pumps for each.
Instead of using a diversion valve to supply water to the heating appliance, the company provides hydraulic separation through closely spaced tees, so the flow rate through the heater loop does not affect the flow rate through the filtration system or vice versa. The independent heating loop is circulated with a variable frequency drive (VFD)-powered pump. The company calculates the developed pipe length and heat exchanger pressure drop to select a pump. This gives a number very close to the actual performance needed, but actual pump performance is perfected through one final step.
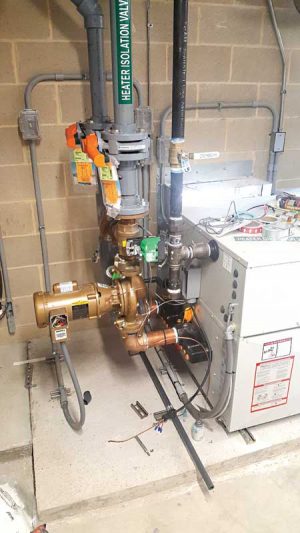
By installing a flow meter on the effluent side of the heat exchanger, the VFD on the pump can be calibrated to perfectly match the specifications provided by the heating appliance manufacturer. If the heat exchanger is not getting enough flow, the speed of the pump is increased; if it is too high, the speed is reduced.
Through a unique control strategy, the company only runs the booster pump when there is a call for heat. As a fail-safe, they also provide secondary flow-proving, to ensure the heaters will not fire without flow through the heat exchanger.
Through the controls, a cool-down period is programmed after the call for heat, and it protects and extends the life of the heat exchanger. Often, a procedural problem in the field occurs when maintenance personnel backwash filters or turn off the pump off any reason, without either shutting off the heaters or giving them a cool-down period. A safe cool-down period can be determined by the temperature differential between the supply and effluent side of the loop, but five minutes is typically sufficient.
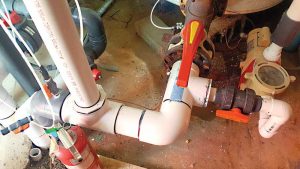
Conclusion
Installing a heating system booster pump, hydraulically separating the filter loop and heating loop, and using a well-designed control system provides many significant benefits. Appliance heat exchangers are protected from corrosion, sooting, and mineralization, service life of the system’s filter pump is increased, electrical consumption is reduced, fuel efficiency is increased, and maintenance is reduced.
A vast majority of existing pool heating systems are not designed or installed as effectively as possible—this leaves a lot of room for improvement in the pool and spa industry.
Author
Tom Soukup is the principal of Patriot Water Works Co., with more than 20 years as a hydronic designer and installer. He specializes in high-efficiency and green technology and brings his expertise to custom commercial work, pool heating, and agricultural projects. He can be reached at twsoukup@patriotwaterworks.com.