How GFRC was used to create Windjammer
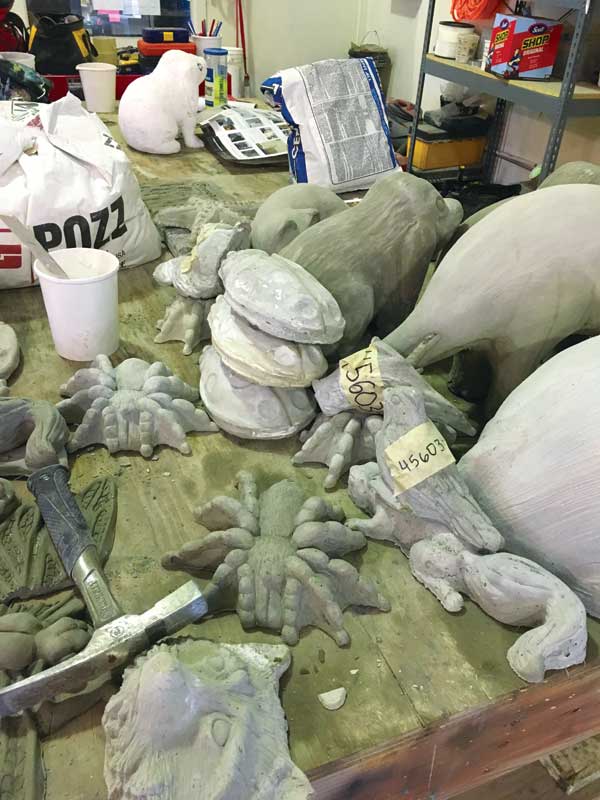
GFRC is significantly lighter in weight and higher in tensile strength than conventional concrete, making it highly adaptable. The chopped strands of glass-reinforced fibres added to the mix give the concrete added strength and durability. It can be sprayed or poured into a mould and adapts to nearly any complex shape—from rocks to fine ornamental details. By using a unique blended concrete mix with fine glass fibres for reinforcement it allowed the team to quickly transform concepts into finished GFRC products.
This project started with a 3D rendering to show where each of the components would be positioned in the project. This allowed the client to visualize how the pieces would be placed together and spaced on the splash pad. An animation also includes water features in action to illustrate how they would operate. Included in this process was creating colour concepts to ensure the palette was in line with the client’s expectations for the overall look they wanted to achieve. Once the client was happy with the design, scale, and colour scheme, it was time to construct the GFRC components.
Production
The first step was creating the frame drawings and hydraulic layouts for each of the project’s components. For all splash pad features, the structural framework is made entirely of stainless steel to safeguard against corrosion by water and chlorine, knowing the pieces were being installed in a wet environment. In this case, specialists who are trained in bending re-bar created the basic shape of each component. Placement of the plumbing within the stainless-steel framework was required before beginning the ‘lathe’ application. This design had many little jets throughout the perimeter of the ship, so there was a fair amount of internal plumbing that needed to be placed before applying the lathe and GFRC. Much of the primary plumbing runs at the bottom of the framework in 1.2-m (4-ft) channels running the width of each component. These channels are what make the structure quite heavy; the front of the ship weighed approximately 1814.4 kg (4000 lbs) and the smaller section, or back of the ship, weighed roughly 453.5 kg (1000 lbs).
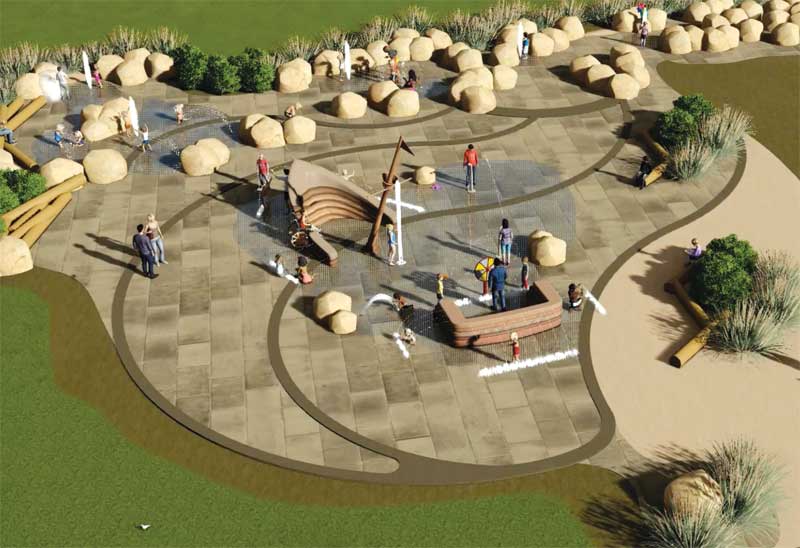
Once the plumbing was arranged in the framework, the team applied diamond-wire mesh and lathe around the frame. The lathe, which comes in sheets, was completed by hand. After placement of the lathe, the stucco—or the fibre-reinforced concrete mix—was applied to cover the steel and lathe.
With the frame, plumbing, and lathe complete, the next step was sculpting the stucco; this is where the real artistry happens. First, a shell of concrete was placed over the steel and lathe—sometimes the concrete can be shot, like gunite or shotcrete, but in most cases, it is applied by hand. There are usually three to four people involved in this process who spend many hours creating and adding the texture, line cuts, and details to give the product its final look.
For the Windjammer project, making the concrete look like old, weathered wood was a time-consuming and involved a lot of hand-sculpting.
Once the desired look was achieved, the final step was colouring and painting. This process took the team about two to three days alone just to complete the authentic appearance of the ship. The rocks and boulders were painted much faster. Once the components were painted and dry, they were packaged for shipment with all the other non-GFRC components, including the sprayers, cannons, water features, ground water features, bubblers, nozzles, and fountain features that were to be integrated into the splash pad design.
Installation on-site
Once the splash pad components arrived on-site and were installed, a specialist helped facility managers program the water features. Their liaison uses the plumbing diagram to show how each element in the splash pad has its own plumbing and solenoid valve, as well as its own electrical fuse on the control panel. There is a controller for these water features that has a program for the sequencing of solenoid valves to each sprayer. In this case, the specialist programmed the features on-site and spent time teaching the client how to adjust the water features should they want to do so in the future to accommodate for any feedback from patrons.
Kent Walker is the glass-fibre-reinforced concrete (GFRC) design and creative manager for Water Odyssey/Fountain People for wet play, and Gametime/Playworx for dry play. He has worked for the company for 10 years and has 35 years of experience designing and creating GFRC and other products for the waterpark and playground industries. He can be reached at kent.walker@fountainpeople.com.