A lengthy build
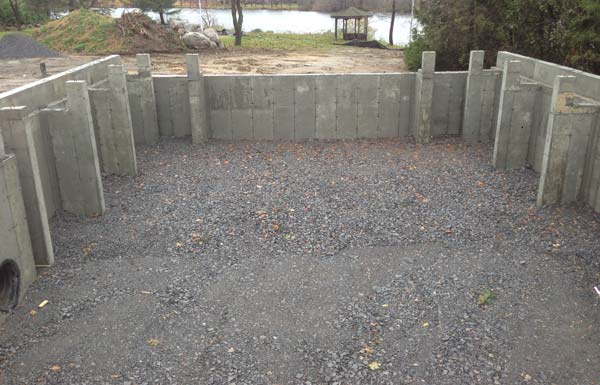
The overall construction process for this project was lengthy, spanning over three years from the client’s purchase of the property to the finished product. The design phase alone took close to a year to complete. In fact, the client demanded comprehensive plans and drawings, which are generally reserved for the trade workers and craftspeople who are overseeing the project’s construction. In the end, it was beneficial for all involved as even the most minor detail had been determined, ‘almost’ eliminating the possibility of error. Having the proper details on hand early on aided in avoiding budget overruns, unexpected delays, and general organizational issues. Large-scale projects such as this require detailed designs, extensive planning, diligent organization, and methodical project management.
The general contractor selected to handle the construction and management of this custom project was DC Snelling of Prescott, Ont. Their task was to keep all trades in order and oversee each component of the project from beginning to end. Not only did they oversee project management, but also contributed their own crews to complete the framing, roofing, and much of the interior finishing. Construction of the residence commenced in late fall 2015 and continued throughout the winter months, at which time the concrete foundation was poured and the wood framing for the walls and roof of the home were completed.
Due to the poor soil conditions found on-site, the pool room required extensive concrete foundation details and additional pilasters to support the structure. The pool was to be built inside the foundation structure of the pool room before the building was constructed; however, due to the uncertainty of the late fall weather, the forming of the pool was postponed until summer 2016. With the pool room having no overhead structure and exposed to the winter elements, the home’s footing and foundation was infilled with granular aggregates to provide frost protection. In the spring, it was reutilized as backfill around the pool during construction. Further, it also avoided having to truck the material to the site during seasonal load restrictions that are typically imposed in the spring.
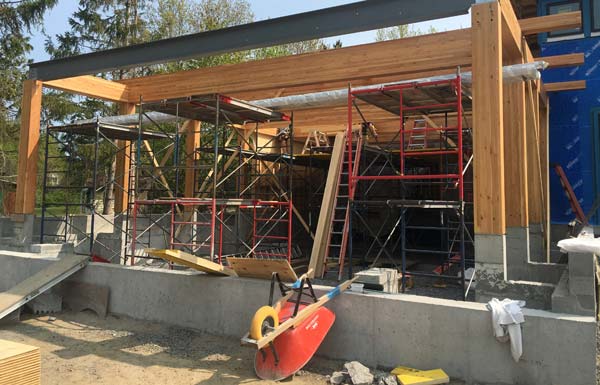
When spring arrived, along with the warmer weather, large laminated pine beams from Western Canada were delivered to the site. These beams, along with co-ordinating support posts, would bear the weight of the entire pool room structure and roof. With the beams on-site, the general contractor decided to proceed with the erection of the pool room structure, instead of starting with the forming and construction of the pool. By rescheduling these construction phases, it allowed the structure and pool to be built concurrently. Having the structure overhead was also a great benefit for the crew building the pool, as it sheltered them from the sun and allowed them to work more comfortably during the summer months.
With the building’s structure well under way, Roger Willis Contracting, an Ottawa-based watershape design/builder, completed the construction of the 5.5- x 11.1-m (18- x 36.5-ft) pool. It was built using cast-in-place concrete, which incorporated the use of insulated concrete forms (ICFs). By using this technology, the pool and hot tub walls would be completely insulated, which would reduce the amount of conductive heat loss through the pool and hot tub shells to the backfilled areas around them. Another benefit to using the cast-in-place forming method, in comparison to shotcrete construction, was the ability to form the structures to a more precise tolerance. This allowed the pool walls, infinity edge, troughs, and automatic cover bunker to be formed and poured as a single monolithic structure. Further, this ‘exact’ construction also meant minimal preparatory work was required when tiling and coating the pool and hot tub.
The pool’s footing, similar to the one supporting the house, was engineered to distribute the weight of the pool structure on the site’s poor soil conditions. Adding to the excessive engineering was the fact the pool floor was to span overtop massive ductwork for the pool room’s dehumidification system. Therefore, the pool’s floor was engineered and constructed to ‘bridge’ the gap where the ductwork sat beneath the pool.
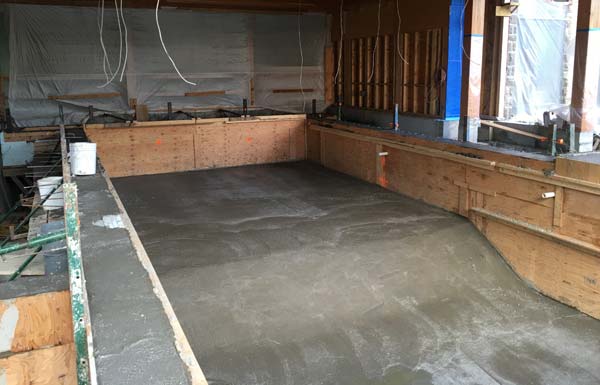
The pool and the hot tub share a connected overflow trough and surge tank due to their infinity edge and perimeter overflow design. The collection tank was formed adjacent to the pool structure, beneath the pool deck, and was made accessible via a concealed hatch. The purpose of this tank is to collect and recirculate the water that passes over these edges, as well as collect any water from bather displacement or wave action. A bunker was also formed at the shallow end of the pool to conceal an automatic safety cover. By incorporating the cover in the pool’s design, the humidity level in the pool room is decreased, allowing the home’s dehumidification system to operate more efficiently, which, in the long-term, conserves energy and reduces heating and cooling costs. Further, the cover helps reduce evaporative heat loss, as well as decrease chemical consumption, overall maintenance costs, and the need to top up the pool.
With the forming complete, the walls, floor, and other components of the pool and hot tub were finished in a single concrete pour. A standard boom pump was used to place the concrete, which turned out to be quite the challenge. The operator’s skill was put to the test, as there was no room for error when navigating the boom between the exposed laminated beams protruding from the ceiling above. Thankfully, no beams were damaged and all 100 m3 (3531 cf) of concrete was successfully poured-in-place. Once the concrete had cured sufficiently, the pool and hot tub, troughs, and surge tank were sealed prior to applying tiles and finish coatings.