Community pools and green tech: Installing water heating systems to reduce energy and increase reliability
Implementing the design
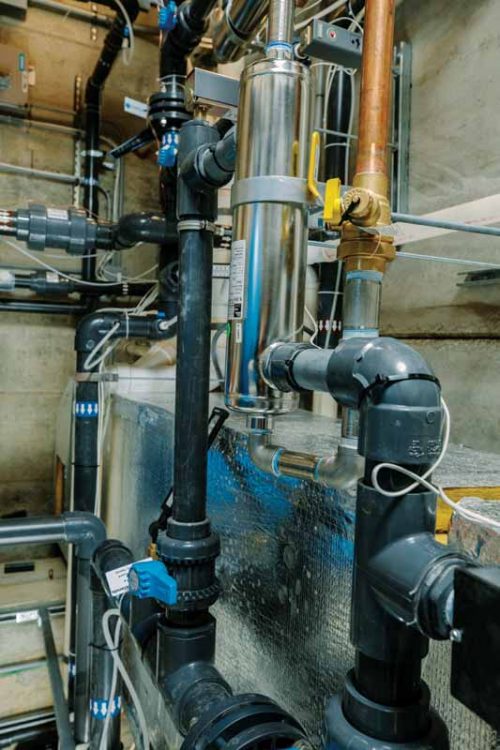
With the engineering data on hand, a special, custom-tailored design was created, which integrated the fixed and variable needs of the facility with the modern technology desired. The fuel savings were significantly high once the new heating system was installed. The gross input reduced from 750,000 to 360,000 British thermal units (Btus). This meant the system would burn 52 per cent less fuel per hour if the units were running at full capacity.
The previous units were 250,000 Btu each. The way they worked—on and off—they either produced full input or no input at all. This wasted a lot of energy as a small body of water, such as a spa, does not need full input. The units would short-cycle or continuously turn on and off, wasting fuel and creating undue stress on the mechanical systems.
While the energy savings and associated costs were integral to the upgrade, there were some other nuanced aspects that proved equally beneficial. The modern design also reduced the parasitic or wasted electric cost.
Additionally, the esthetics and equipment placement were crucial to the project. For instance, the units were no longer placed on the floor, but mounted above. Also, since the mechanical room was a wet environment with the potential of damaging leaks, it was critical to install the heating equipment off the floor to prevent the entire system from failing before the damage could be contained.
It was important the best and most commonly used products were installed, so if something were to fail, the facility would not need to wait weeks for a specific part or replacement. Being able to procure an equipment piece in a timely manner was crucial to the upgrade.
Also, maintaining a pool’s temperature requires much less energy than recovering it. With this new installation, the facility could recover the temperature of one body of water (out of the three) by simply shifting the heat energy from one zone to another.
Thinking outside the box
Heating a pool and a bathtub is the same—just on a different scale. By thinking outside the box, one can ensure customers receive better efficiency, greater reliability, and higher availability with their products. For this, one needs to move beyond water chemistry and look at other disciplines. Working co-operatively with other trades can take one’s projects to the next level. A coalition of professionals from different fields can help expand one’s horizon. For example, if one knows a local, high-quality electrician, working together might help in bringing more educated applications to the project. Just as it takes a village to raise a child, the same applies to creating truly appealing pool projects.
Conclusion
The system has now been installed for more than six months and the pool manager has reported the temperature variance has been no more than a third of a degree. The facility has noticed a significant reduction in energy usage.
Pre-planning stages are crucial to any project. By planning the design and installation ahead, Soukup was able to anticipate unforeseen issues and complete the project successfully without any delays. It saved him a large amount of on-site time. This translated into less interference of the modelling schedule and minimal downtime for the pool.
A large complaint Soukup often hears is clients having to call back companies multiple times due to a problem that cannot seem to be fixed. Forward thinking helps remove that issue.
Pool professionals must take their time to understand the project, listen to their client’s needs, and plan accordingly. The more communication and preparation one can bring into their project, the better the results will be. Finding the best solution to a client’s needs is fundamental to the success of any project. Not only do the results help build a customer’s confidence in the brand, but also guarantee their loyalty.
Eliatt Di Lieto Jr., works as a content writer for Patriot Water Heater Co., and reports on its interesting and unique hydronic projects. With 15 years in information technology (IT), he aims to bring into focus the impact of new technology into the hydronic field. He studied journalism and electronic media at Long Island University (LIU) Post and runs an IT consulting company on Long Island, NY. He can be reached via e-mail at eliattd@patriotwaterheater.com.