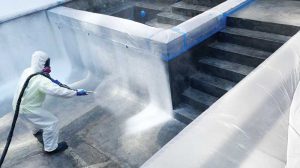
By Peter Gibson
Most pools before the Second World War were rectangular in design and constructed of formed concrete. Often, these pools were unfinished or adorned with clay tiles. After the war, rudimentary pool paints were used to finish pools, but did not last long, and needed constant reapplication.
Later, rubber-based paints were introduced; also at this time, huge housing developments were afoot, creating suburbs—this is when commercial pool construction began. To speed up the construction process, the idea of gunite and shotcrete was introduced. A large portion of these pools were freeform and did not promote the use of tile, and using paint meant an additional process to smooth the gunite for paint. At this stage, it was decided basic white cement with a marble aggregate would be used in it for strength, which was then trowelled over top the gunite.
Gunite and plaster then standardized the construction process. Over the decades, various other cementitious products were introduced (e.g. specialty plasters such as quartz and pebble aggregate plasters). As a result, cement-based materials came to dominate the pool industry, with construction companies widely adopting them. As time went on, the performance of these cement products was deteriorating. At this point, pool professionals began thinking of other materials to finish pools, and coatings companies started developing coatings specifically for pools. This also became a way to sell into the DIY market, as in, not requiring professional application. The types of coatings sold were simple pool paints that homeowners and pool operators could apply, as it did not require a high level of skill or spray equipment. These products are rolled on, as opposed to industrial-grade products, which require a high skill level and sophisticated plural component equipment.
What are polymeric materials?
Polymeric materials are made of long, repeating chains of molecules that have unique properties depending on the types of molecules employed and bonded together, and the types of bonds. These molecules and bonding types will determine the polymer produced. In the coatings industry, there are hundreds of coating chemistries that will determine the end use of the product. For example, pool coatings are types with subgroups of chemistries that determine the performance and longevity of the coating. Some polymers bend and stretch, while others are hard and tough, such as epoxies and acrylic.
There are three primary groups of polymers:
- Thermosetting—base resins used in the coatings industry. Curing systems are chemical cure or initiators for free radical initiated chain growth polymerization.
- Thermoplastic—plastics for hot tubs and formed plastic products.
- Elastomeric—adhesives and sealants. These are flexibilization products. How these materials react to heat will determine what category they fit into.
Thermoplastics will melt under high heat, while thermoset materials will not melt and retain their form and stay solid under heat once cured.