Storage and handling best practices
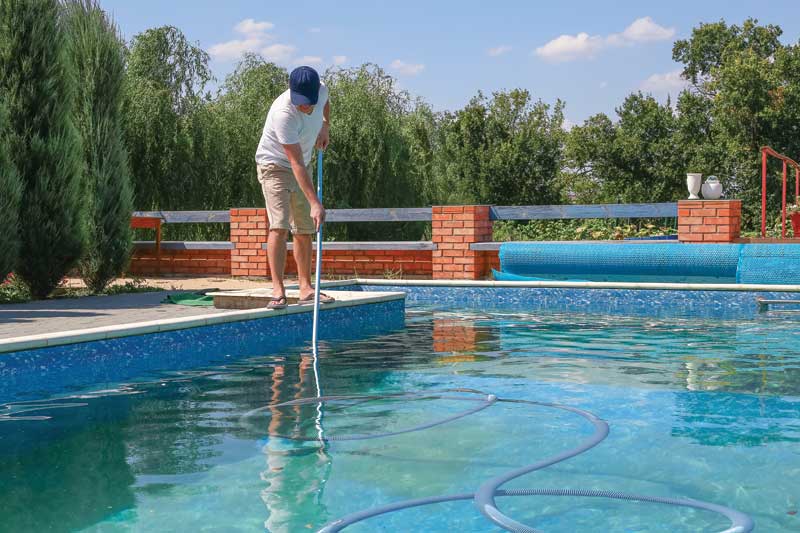
With the use of liquid chlorine likely being more common for the upcoming pool season due to limited availability of other sanitizers and oxidizers, certain modifications to routines and practices should be made to maximize the effectiveness of the product being used. This should be done safely with proper storage and handling of products.
One of the larger differences between sodium hypochlorite and other solid chlorinating compounds, such as calcium hypochlorite, trichlor, and dichlor, is how storage conditions can impact product degradation. Bleach concentration and storage temperature play a large role in the loss of product strength. Generally, increased temperatures will accelerate the process for all strengths, and higher concentrations will degrade at a faster rate. It is recommended to store liquid bleach in tightly closed containers out of direct sunlight in a dark cool place. Further, in warehouses, liquid bleach should never be stored over solids. It is a good practice to store inert materials, such as hoses or handhelds, in-between liquid bleach storage and other chemicals.
When adding liquid chlorine to the pool, service technicians should pour slowly to avoid splashing. It is strongly recommended for one to wear gloves and goggles when handling and applying the product. Liquid chlorine is corrosive, so it may cause skin and eye irritation as well as damage clothing. Finally, before a service technician discards any used containers, it is a good practice for one to rinse the containers out before discarding them in the trash.
Transporting large quantities of liquid chlorine on service trucks also requires a modification to the normal routine. It should never be transported in the passenger compartment and, to protect against incompatibilities, use of an approved secondary container is recommended as a safeguard in the case of spills or leaks.
It is also important to note sodium hypochlorite should never come into direct contact with acids or ammonia-containing compounds. Mixing them could result in the formation of harmful gases, which could lead to breathing difficulties.
Transport Canada/U.S. Department of Transportation (DOT) regulations may be different for each province/state, sometimes even for individual municipalities/counties. Therefore, it is the responsibility of the vehicle driver to know and comply with all transportation regulations. This also means following the proper requirements for signage on service vehicles. Service technicians must be sure to follow all pertinent regulations for the placarding of hazardous materials for transport. Service technicians should refer to Transport Canada/U.S. Department of Transportation (DOT) regulations as it pertains to proper placarding procedures and exemptions.
General guidelines include:
- Carry safety data sheets (SDS) for all chemicals.
- Separate and secure all chemicals.
- Separate liquids from solids;
- Separate oxidizers (dichlor and trichlor from cal hypo, lithium hypo, and bleach); and
- Separate muriatic acid from everything including salt.
- No hydrocarbons.
- Gasoline;
- Diesel;
- Brake fluid; and
- Motor oil.
- Respond to pool chemical spills immediately.
- Never put spilled chemicals back in the original container because they might be contaminated with substances such as dirt or grease;
- Use separate, dedicated materials including clean and dry brooms, shovels, and containers to clean up and appropriately dispose of each spilled chemical. (Refer to the SDS for appropriate absorbents for liquid spills); and
- Do not pour spilled chemicals down the drain or sewer.
- Do not store chemicals on a service vehicle for long periods of time—unload and use them or store them in an appropriate storage area.
From a chemical standpoint, liquid chlorine can be an effective element of the weekly pool care maintenance program and is a capable weekly sanitizer. However, since it must be added frequently to maintain the proper chlorine residual, anything that can be done to extend the life or enhance the effectiveness of liquid chlorine is a valuable addition to the program.
Balanced water, preventative algaecides, enzymes, and phosphate removers all contribute to creating the ideal environment for liquid chlorine to be successful. In addition, proper physical maintenance, as well as storage and handling, are necessary to maximize the pool maintenance program and minimize the work necessary to protect swimmers and provide the expected environment. An all-inclusive pool maintenance program is the key to success.
Alicia Stephens is the education and training manager for Biolab Inc. In her 20 years with the company, she has focused primarily on education, training, and development, as well as technical support and new product research and integration. Currently, Stephens supports all education and training initiatives for the Biolab Pro Dealer division. She can be reached via email at alicia.stephens@biolabinc.com.
Brian Trenck is the technical services team lead for Biolab’s research and development (R&D) group. With more than 23 years with the company, he provides product application expertise and product troubleshooting for new product development. Trenck is dedicated to technical training and problem-solving for internal and external customers. He also serves as the subject matter expert for water testing software and hardware. Trenck can be reached via email at brian.trenck@biolabinc.com.