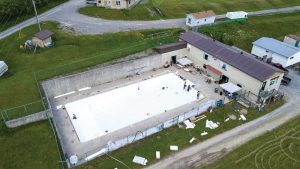
The average installation of a commercial membrane takes four to five days, making the short-term shutdown well worth the expense as the facility will no longer need to frequently replace the pool liner. This is also why PVC liner membranes are popular for aquatic facilities that are also interested in eliminating the yearly plastering and painting procedures which are commonly needed before the pools reopen every summer.
On this project, the timing seemed a little tight because the liner membrane needed to be installed, and the pool needed to be inspected well in advance of the camp’s opening over the Canada Day long weekend. The only part which required extra time and scheduling co-ordination was the replacement of an old set of fibreglass stairs that were being replaced with new, larger, poured concrete steps.
“By working together with the PVC liner membrane manufacturer and Jonathan Easton, the camp’s facility manager, we were able to complete the entire welding of the membrane on the pool with four installers in just a week,” says Ruben Cuevas, owner of RECA Vinyl Works.
Track challenge
The pool had to be converted from a traditional residential style liner, with a bead and track, to a weld in place membrane. One of the key areas was at the membrane termination area at the top of the pool wall.
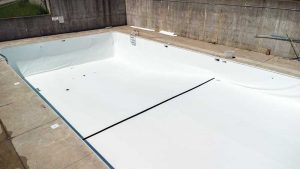
“We came up with a PVC laminated stainless steel, 2 in. [50 mm] strip in which we placed stainless steel rivets every 8-in. [203-mm]. This was a tedious process to ensure it all aligned properly, but it was necessary to properly terminate the PVC membrane,” says Cuevas. “In addition, we used a product that turns rock solid and bonds to everything to ensure against any water getting behind the PVC membrane.”