Membrane-lined pools: The increasing popularity of weld-in-place membranes
Offering a membrane pool finish
Weld-in-place membranes provide a pool finish with unique benefits not provided by marbelite, stone-coloured quartz finishes, or thermoplastic coating.
“One of the main advantages of the membrane pool finish is it doesn’t crack regardless of freeze-thaw conditions or earthquakes,” says Rintoul.
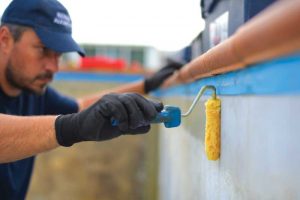
The membrane completely seals the structure of the pool and keeps it watertight. This makes it ideal for both renovating existing pools and building new pools.
“Once you have a crew of installers who know how to apply these membranes, you can fit them into your pool offering, whether you are using the membrane to finish off a new concrete wall or stainless-steel pool wall construction, or you are covering a cracked, peeling, or leaking gunite pool.”
Rintoul suggests weld-in-place membranes to clients looking for a higher-end project with unique features. He recently built a pool with a vanishing edge, full width steps, a full-length sitting bench, and some deep end stairs.
“We recommended the 2 mm membrane because we knew it would be particularly well-suited to sealing the reservoir of the vanishing edge to make it watertight and fit perfectly over all the special features in the pool,” he explains.
The client was also immediately attracted to the dark slate colour and texture.
“It really blended beautifully with the surrounding stone deck and coping she selected for the pool, and the project was a great success.”
A growing number of pool professionals consider weld-in-place membranes a lucrative addition to their business and are taking the time to train their staff on proper installation. Not only do they offer a unique and truly attractive finish, but they also have a set of skills to keep crews busy through the winter.
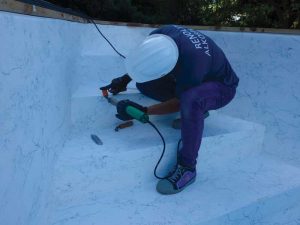
Training and retaining crews
Since proper training is the first order of business, some membrane suppliers offer assisted installations to builders and installers.
“What we are seeing is pool pros don’t realize how easy it is to install this product, and there are very low barriers to entry, as you don’t need to invest large amounts of money for equipment and you don’t need to have the material in stock, as we simply order rolls of material for each job,” says Solmundson.
“There is a learning curve, obviously, like anything else. But compared to other types of equipment repairs, it is a much faster learning curve.”
Solmundson explains the main welding component is the easiest to learn, while the more intricate parts like stairs and corners are more complicated. As such, they are the focus during the assisted training.
Professional installers like Solmundson also train companies interested in learning these skills and are happy to travel to their location.
“I have installed and trained crews in Brazil, Turkey, China, and more, teaching the methods I originally learned in Germany,” he says.