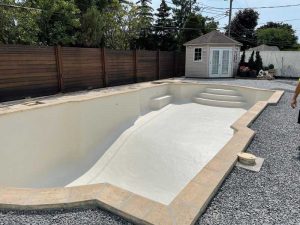
The use of micro-glass-reinforced coatings is a novel way to refinish pools and spas. These coatings are unlike conventional pool paints currently used in the pool industry, as durability and performance of traditional polymers remain an ongoing issue where long-term performance is desired.
Glass flake coatings address these shortcomings. They are also an excellent alternative to cementitious materials, especially in the waterpark and commercial pool arena where operational costs are a concern. Micro-glass coatings are a workhorse product for large bodies of water as they can be applied fast with minimal labour.
Although other forms of composite coatings have been used before, this method is different because glass is added into the resin, thus allowing the resin and glass compound to be sprayed as one homogenous material, thereby eliminating fibreglass mat.
Disbondment was a common problem with mat-type methods. With the glass addition into the resin, this has had a positive influence on bond promotion, and prevents undercutting of the coating because of the elimination of tensile stresses built up in mat-type applications. High shrinkage of thermoset resins is one of the primary causes of disbondment from concrete substrates. During the polymer polymerization (i.e. cross-linking process, there is a volumetric change in the coating. This change can cause the coating to lose bond. (As an aside, thermoset resins have an eight per cent shrinkage coefficient.) These shrinkage stresses can cause the resin to heave off the concrete.
Glass flake coatings
Glass flake coatings were developed in the United States in the early ’60s. They were first used for heavy-duty industrial protective coatings for steel and concrete corrosion protection. As all organic coatings will, to some extent, convey moisture vapour and allow gas diffusion, preventing or resisting this is key. It is here glass flakes initially found their niche before being used in the pool industry. With decades of service in immersion conditions, some 20-year-old sea water applications have been inspected and put back into service.
Glass flakes are platelets or flakes of varying particle size and thickness. They overlap each other and extend the path distance in a coating film, providing a barrier to the passage of moisture and gas diffusion by creating a tortuous path through it. There are different glass types, but in the corrosion coatings sector, electronic corrosion resistant (ECR) glass offers the highest levels of chemical resistance and is inert for corrosive chemical environments.
Resin binder selection is just as important as the glass type, so the glass/resin compound delivers the best outcome. Several thermoset resin types are used depending on the cargo. Further, the level of glass flake also has a bearing on coating thickness and flexibility.
It is evident there are many benefits to using glass flake, particularly for coatings. This is not a new concept for pools; base resins have been used in California for 30 years and micro-glass coatings are being used across the United States and Canada.