Dosing the drums with glass flake
The glass flake is added to the resin in a staggered fashion for complete integration and dispersion. A special type of mixer is used. In general, mixing coatings is more scientific than one may think. The mixer must have the correct mixing blade for proper dispersion of the glass fibre, and the mixer must have enough torque to move the material around in the drum. Failure to mix the coating properly can cause the compound to clog the gun and result in other quality issues.
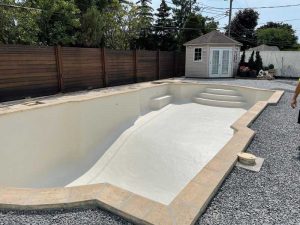
Application
Once the pool is prepared and masked off, the high-performance primer is applied to marbelite pools. First, the walls are sprayed, then the floor, in a specific spraying pattern. Applicators must observe proper spraying techniques as this will determine the correct deposition of the material. If improper techniques are used, runs, sags, and other defects can appear. Proper techniques will also improve the cosmetics and esthetics of the coating. That said, applicators must be mindful of how they use the gun. Among other things, speed of moving the gun and distance from the substrate are a few examples of proper techniques. Maintaining good form (ergonomics) is always important.
In brief, the compound is applied 1.3 to 2 mm (50 to 80 mils) thick. The correct resin temperature must always be maintained as resin heaters are used in conditions under 15 C (60 F). The resin temperature determines cure levels and flowability off the resin through the gun.
Cure time
Cure time is determined by ambient and resin temperature, though cure times of under 10 hours can be achieved. Cure times can be accelerated by increasing the resin temperature and adding more catalyst. Higher ambient temperatures expedite the curing process. Cures are stunted by low catalyst levels, cold resin, and low ambient temperatures.