Acapulco Pools drives positive workplace behaviour and practices to improve performance
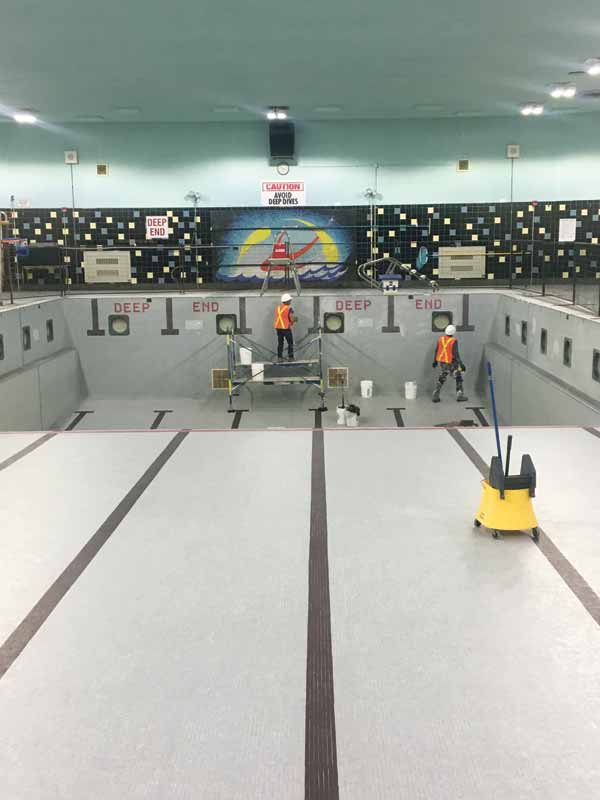
Since the COR audit tool has 19 separate elements, the first order of business after the initial assessment was determining how to organize the entire program. Acapulco has more than 60 crewmembers covering over five trades, working on more than 65 jobs every year, which can range in length from two weeks to two years. Being able to monitor and easily access the right documents, inspections, and reports was going to be critical to the company’s success in an audit situation.
After a fair amount of research and a couple of different demos, management agreed on a web-based construction safety software program that would not only house all of the company’s safety documentation, but also allow management and supervisors to complete his/her paperwork on a smartphone. Going digital was a major turning point, as all crew leads were provided tablets so he/she could complete their paperwork on an app that could be reviewed in real-time. This largely increased reporting and communication from the field to the office, as well as overall organization of the safety program framework.
One of the other major reasons for this decision, with this particular software, was its structure is actually meant to mimic the way the COR audit tool is set out. Acapulco was able to load all of its existing documentation and then update the status of each audit question to either non-compliant, in progress, compliant, or not started. As a result, the company was able to use its annual action plans in conjunction with this real-time feedback for each section of the audit to keep plugging away and updating the program to meet the COR standards.
What changes were made to each aspect of the business?
Acapulco started with a shift in safety culture, which meant all aspects of the business were adapted in to reach the end goal. The most visible changes happened on-site, but the changes made in the background were equally significant.
This was the first time the company had a full-time health and safety manager to oversee the entire safety program and provide support to the workplace. A budget was also allotted to the safety department to carry out the items in its action plan. Planning appropriately, sales and estimating started to carry numbers in their bids that would support a health and safety support system.
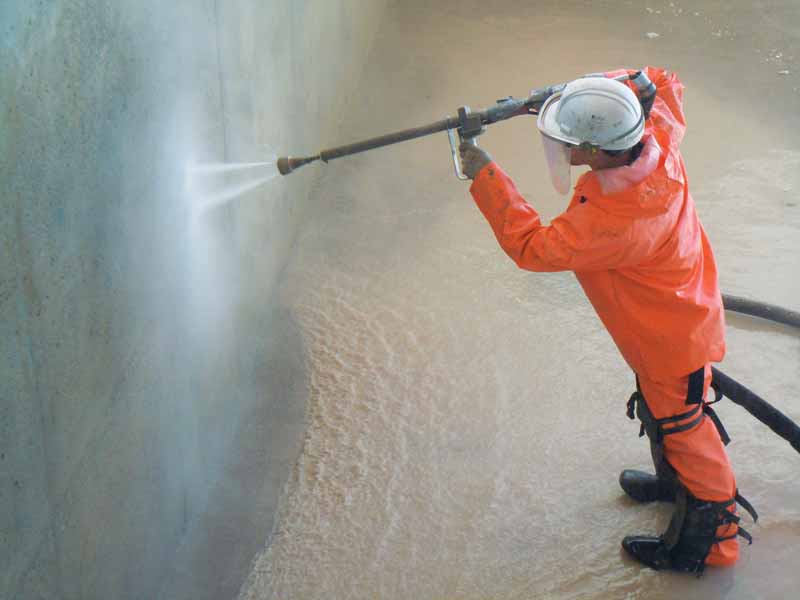
In terms of project planning, the company started to standardize the safety items and documents that were required at each jobsite, which set the tone for workers and their responsibilities on-site.
In the field, Acapulco started to identify critical tasks, as well as all of the other activities involved with building pools, and identify all of the risks and controls that were needed to carry out the work safely. As mentioned earlier, the change in how on-site paperwork was completed meant feedback on daily reports could be provided in real-time, instead of receiving daily paperwork weeks at a time.
At the labourer level, the company focused on investing in its employees and affording them the resources to attain goals set out on an annual basis. As a result, the company improved its job-specific training, as well as made its new worker orientation much more comprehensive. Personal protective equipment (PPE) was made more obtainable by using a vending machine system that all workers were given codes to access and chose from a range of PPE that best suited them and the work at hand for the day.