Reviving a troublesome heater
By Eliatt Di Lieto Jr.
Crystal clear, perfectly heated water has an appeal all its own. Lounging by a tepid, community pool offers bathers a great way to relax and unwind after a long day.
However, it is very unpleasant to anticipate this relaxation only to dip a toe in and find the water is frigid. This unpleasantness can easily spiral into frustration when maintenance is unable to provide a timeline as to when the issue may be resolved.
The scenario
Tom Soukup is a specialist in hydronic heating across a wide variety of applications and owns and operates Pennsylvania-based Patriot Water Heater Co. Soukup received a call from a local homeowners’ association (HOA) regarding a 719,228-L (190,000-gal) outdoor pool. The heater had been installed four years earlier when the pool underwent significant expansion and renovation, but the facilities manager informed him it had not worked correctly since the install.
Symptoms included the unit going into lock-out, substandard heat, and the continual need to be reset. Several repair companies had examined the unit, but were unable to find a suitable fix.
Observations
Soukup and his team were called in to do a site survey. One aspect of the survey was to perform some forensic research on the chain of events leading up to the repair calls.
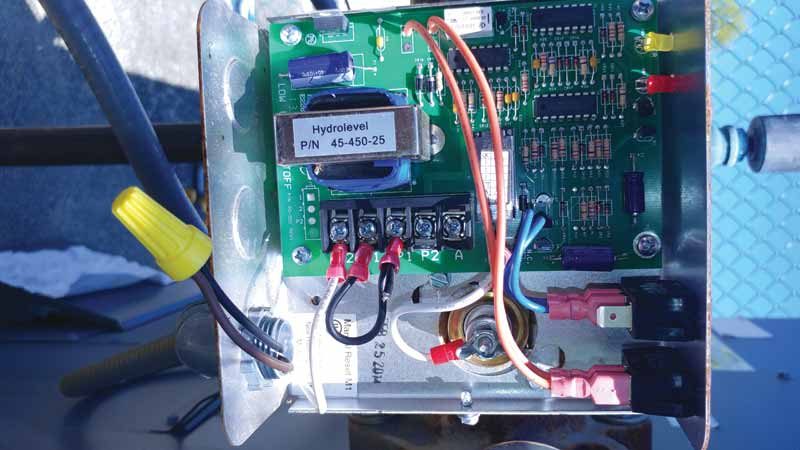
Soukup spoke to the facility manager to clear up some of the specifics in regard to the repair efforts:
- How many companies had made service calls?
- What did they do?
- When was the service performed?
Establishing a chronological order was important, as this would help develop a timeline of the noted issues and provide some insight as to why previous contractors were not asked back for further repairs. For example, Soukup discovered that when the first technician examined the unit, the heat exchanger was clogged with soot because of improper water flow. The unit fired and the service technician burned himself. In this instance, proper safety protocol was not followed.
The pump room was located beneath the water line of the pool. As the installation was a retrofit, there was not enough room to install an outdoor heater. The initial contractor opted for an outdoor heater installed above the pump room, as this was the only logical location.
The contractor relied on the heater’s internally installed circulation pump to move water from the filter to the heater. They also opted to go with 1.825-million British thermal unit (Btu) pool heater.
When starting the pumps, Soukup found a tremendous amount of air being circulated through the system, which was causing the pumps to cavitate. This observation prompted him to request a walkthrough with a facility manager.
The original contractor installed a float style air eliminator at the heater. With Soukup’s experience in hydronic heating, he understood float type eliminators let air out, but also let it back in.
Given the unit was above the pump, whenever the main pump went off, it sucked air back in the system. This caused lack of flow and a low water condition. The issue was brought up to a previous contractor, who bypassed the low water cutoff safety device. In turn, the unit could dry fire—which is certainly not advised.