Success
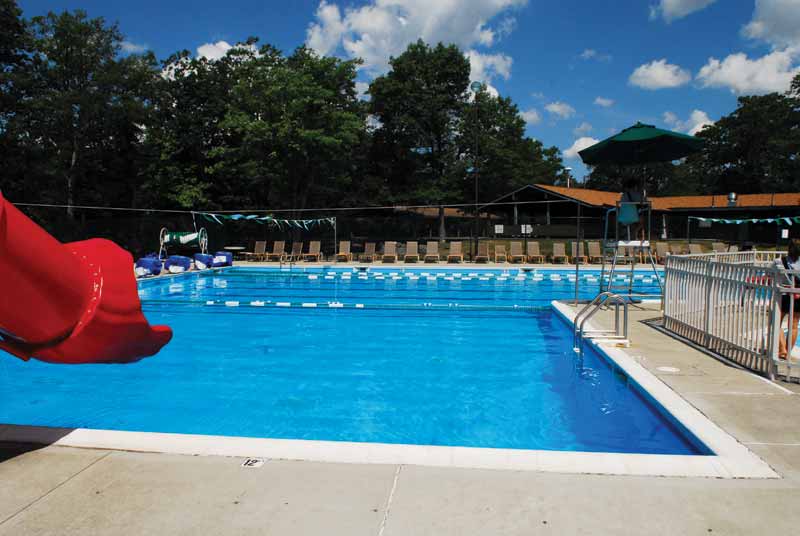
At this point, all piping had been completed and the heater was in. Thermometers were installed on the supply and return of the heater to display the Delta T, or temperature difference, of the heater.
For safety devices, Soukup added a manual reset, high temperature limit, as required per code in the site’s locale. A flow switch was installed in the booster pump loop, which meant the heater would not be able to fire unless the booster pump was running. This precaution would prevent dry fire and avert the disaster the client had previously experienced. Upon installing these devices and performing the correct electrical and safety device wiring, they were able to push water through the system and check the flowrate.
According to the flow meter, the flow on the main filter loop increased by approximately 15 per cent, which was within the provided specifications. The meter on the booster pump loop said the mathematics worked out correctly and was getting 681 lpm (180 gpm) across the face of the heater.
Next, the installation team turned on the internal pump to remove all the air from the system. This meant no more cavitation.
The team then turned on the heater with ignition systems disabled to ensure all safety devices were working properly. The unit attempted to fire but, with the ignition system disabled, it could not. They turned off the booster pump and the heater went into lock-out, as expected. This was the proper chain of events.
Soukup and his team felt confident to re-enable the ignition system. Right as rain, the heater turned on. The company’s standard procedure dictates its employees perform a proper start-up as if the system had never been installed before. This procedure meant checking gas pressure, all safety devices, and the overall safety and functionality of the unit.
Conclusion
This case study is an example of the successful reinstallation of a malfunctioning heater. It is challenging to understand and gather all the information available from manufacturers, sales representatives, and technical support, and then successfully execute such a task. More than anything, it is invaluable to understand the craft; installing a piece of equipment is not as simple as dropping stuff into place, attaching pipes, and walking away.
The customer was pleased by the work and asked Soukup and his team to look at another heater in the community that had been installed by the same contractor which was beginning to exhibit the same problems.
When hiring contractors for various pool needs, clients should not always choose the lowest bidder. The saying is true: “the bitterness of low quality outlasts the sweetness of a good price.” When a contractor truly understands and cares about the result, a customer will end up with a better install and better support to follow.
Eliatt Di Lieto Jr., works as a content writer for Patriot Water Heater Co., and reports on its interesting and unique hydronic projects. With 15 years in information technology he aims to bring into focus the impact of new technology into the hydronic field. He studied journalism and electronic media at L.I.U. Post and runs an IT consulting company on Long Island, NY. He can be reached via e-mail at eliattd@patriotwaterheater.com.