Tips and tricks for installing automatic pool guides on fiberglass pools
Elevation challenge
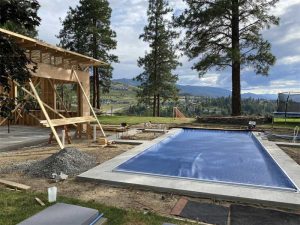
By nature, an automatic pool cover requires it be installed on a level plane. The track cannot be sloped or the cover mechanism will not operate properly. This can be a challenge for those installers that are working with different deck treatments or tile additions that might raise the elevation of the top of the pool from the shallow end to the deep end.
“On one recent installation, the builder had added some tiles around the built-in spa in the shallow end of the pool,” says Horwood. “The tiles were beautiful, but it changed the elevation significantly at the top of the pool in the shallow end versus the height of the top of the pool in the deep end. As a result, this made placing the ‘polybox’ for the automatic cover challenging to install.”
The solution Horwood used in this case was to use the automatic cover components designed for a vinyl liner pool and adjust them to work in this particular situation.
“We applied several ‘MacGyvered’ techniques including using a vinyl liner retainer as it has a higher profile to accommodate the increased height created by the tiles used in the spa at the shallow end of the fibreglass pool,” says Horwood.
This not only applies to tiles used for a built-in spa in the shallow end, but also to various deck treatments used around the pool perimeter. For instance, builders need to consider the height of the stone, travertine, and mortar being used around the pool perimeter because this added elevation must match the elevation in the deep end where the automatic cover enters and exits the housing. Manufacturers provide risers to make up for the increased elevation, but there is a limit to the height accommodation. Matching the height of the lid to the different coping and retainers is crucial to ensure the successful operation of the cover. Builders need to plan this in advance of the installation. This is not unique to fibreglass pools, but more common as many come with built-in features such as spas, tanning ledges, and steps that span the full width of
the pool.
Housing challenge
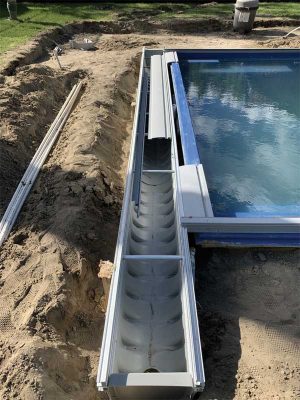
Before completing the backfilling of the pool, the automatic cover kit is attached at the deep end. The process begins with a one-piece encapsulated coping with a wall cap that supports a pre-made, slide-on ‘polybox’ housing.
The housing is screwed into the wall in a ‘tongue-and-groove’ style that is easily attached to the fibreglass pool wall. This does not come with a pre-designed solution, however.
“We have been using the vinyl liner retainer and treat it like a steel wall structure,” says Horwood. “Once again, we do a little ‘MacGyvering’ to be able to support the housing by free-staking into the ground, which works pretty well.”
As part of this process, it is very important the housing is levelled for the automatic cover to function properly. The cover housing as well as the lid covering the top of the housing must be perfectly level. This entire process needs to take place in the pre-pour stage of the cover installation.
“There is always a bit of a dance to make the timing work—as automatic cover installers want to get the housing attached before the concrete is poured, and builders are anxious to get the concrete poured quickly,” says Horwood.
Corner challenge
Installing the track around the corners of a fibreglass pool can present another unexpected challenge.
“Because the corners of most fibreglass pools have a radius, we notch out the lip in the coping that was originally designed for a vinyl liner bead receiver,” says Horwood.
The manufacturer can provide these corners pre-built for the builder to make them ready to screw down the corner for the installer. Providing these pre-built corners makes the track sit flush on the wall in the corner to ensure the coping remains level.