Winter pool construction: Tips for builders when working in sub-zero temperatures
Erecting temporary construction tenting
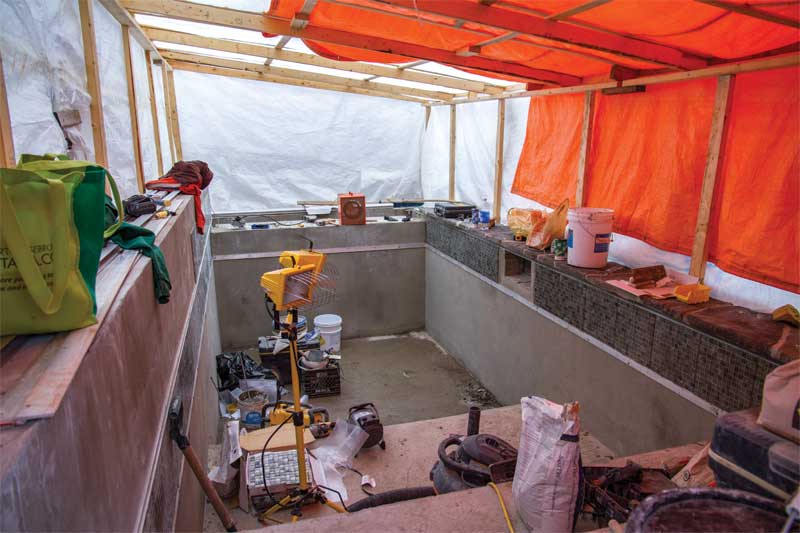
Temporary tenting or hoarding is commonplace for any type of construction being completed during the colder months. These structures need to be built to handle all types of weather conditions, such as rain, snow, ice, and wind. The tenting should also allow workers to perform their tasks in comfort to ensure maximum quality and productivity.
Many temporary tenting variations are available for use. Determining what type of tent to use will depend on the specific work that is being completed. For instance, inflatable tents, which are inflated by large blower fans, are ideal for temporary work that can be completed quickly. Pre-fabricated truss structures with light gauge steel or aluminum trusses are well-suited for long-term construction often spanning several months. These structures are covered with plastic or tarpaulins that can be heated.
On-site fabricated structures, using dimensional lumber, is also a cost-effective form of tenting and can be customized to a project’s unique requirements. Tenting not only benefits a builder by sheltering work areas and crew members from the elements, but also allows a builder to essentially create their own weather. Temperature and humidity can be set to ideal levels, which allows for the proper curing of products such as concrete.
Concrete in the winter
Attempting to complete certain construction tasks during the winter can be more difficult to perform than if they were done during the summer. Pouring concrete is one of these tasks; however, by following the proper guidelines and taking the appropriate precautions, concrete can still be placed in the coldest of temperatures.
To successfully pour concrete to form the pool structure, proper site preparation must take place beforehand. Any area where the concrete is being placed should be thawed and free of ice or snow. It should never be poured onto frozen ground, as settlement may occur once it thaws. It may take several days to warm the ground to the appropriate temperature. However, this can be achieved using hydronic surface heaters. These heaters are the ideal method to make sure the ground is free of ice and is warmed to the appropriate temperature.
These heaters use diesel, propane, or natural gas and are capable of thawing and heating 232 to 557 m2 (2500 to 6000 sf) of ground up to 0.3 m (1 ft) in depth per day. These systems comprise a boiler unit which heats fluid passing through a heat exchanger. Lines run from the heating unit along the surface of the ground which is then covered by lightweight, flexible insulated blankets or tarpaulins, which lay flat in sub-zero temperatures.
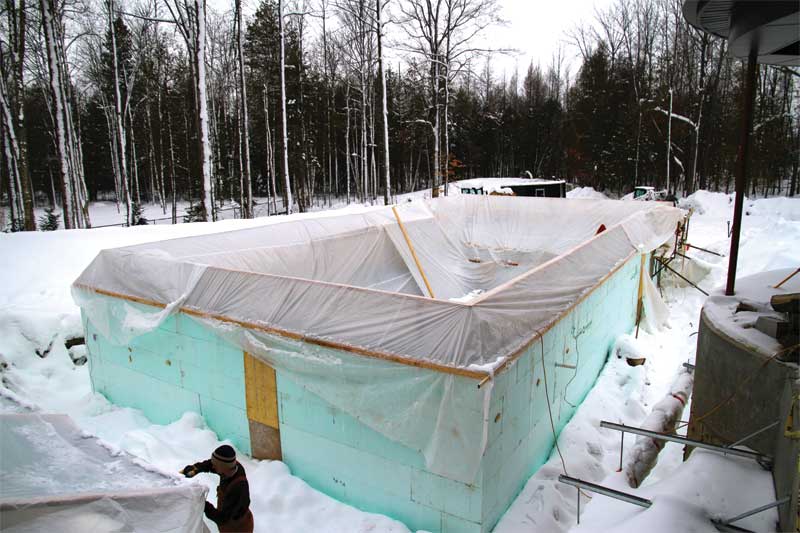
These blankets are typically orange and have two layers of tarpaulin material covering an inner layer of closed-cell foam insulation. The ground below the blankets is thawed and remains warm until concrete is ready to be poured. Special measures should be taken when placing concrete at temperatures below 5 C (41 F). When below-freezing temperatures are expected, it is essential to protect concrete during its placement and curing stage. Concrete suppliers prepare special ‘winter condition’ blends by adjusting the concrete mix to the expected weather conditions.
If the concrete is being poured outside, or in a controlled environment, transporting it to the site in cold weather also requires the concrete supply company to take additional steps. The concrete mix comprising coarse (stone) and fine (sand) aggregates, cement powder, and water should be heated and free of any frozen materials.
Special additives or admixes such as setting accelerators may be added to aid in the chemical reaction of the setting concrete and to increase the rate of early strength development. This essentially speeds up the concrete’s curing process. Water reducing admixes are also commonly added to the concrete so it remains workable (in a fluid state). By using a reduced amount of water in the mix, the cured concrete will have a higher strength.
Before leaving the concrete plant, the temperature of the mix should be adjusted taking into account the time needed for loading the truck, transportation to the site, unloading and placement, and the time it will take before the concrete is finished and protected. If concrete is being placed using a line pump or standard boom pump, pre-heating the lines will also be required.
Pouring concrete is far easier in a tented enclosure, as the temperature and humidity levels can be controlled. This can actually lead to a higher strength and quality of concrete than what may be poured in the summer. Concrete should always be protected in the initial curing stage until it reaches at least 3447 kPa (500 psi). Once it has gained the sufficient strength, the concrete should still be heated and protected from freezing for a few days. Afterwards, the enclosure’s heat can be gradually decreased. Sudden cooling should be avoided to mitigate the possibility of thermal cracking of the concrete. Pouring pool components in the winter will allow ample curing time for the structure. This eliminates the crew from sitting idle as they wait for concrete to cure when the weather is warmer and more co-operative.