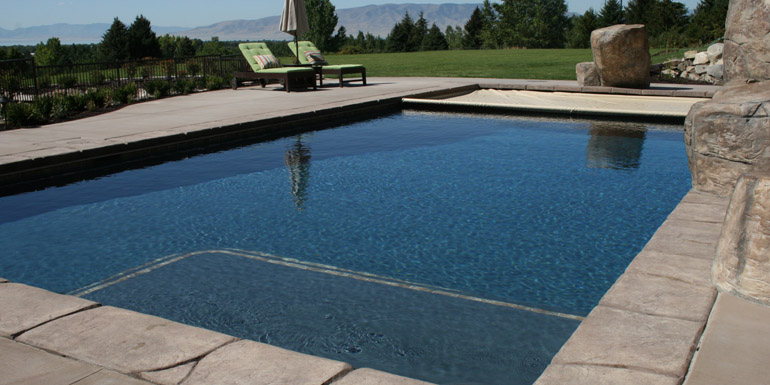
By Kevin Losee
Automatic safety covers have seen a number of innovations in recent years which have not only increased their reliability and performance, but have also opened the door to allow them to be installed on pools of all different shapes and sizes. Some of these innovations provide the flexibility needed for automatic covers to be installed during the construction of new pools, while other options allow the cover system to be installed on existing pools. This article will explore a number of different options and systems that are available, as well as explain how they are used in different applications.
First things first
At the outset, knowing the main components of an automatic cover system is important. The first component is the drive mechanism. This is the motorized portion of the automatic cover system that physically moves the cover back and forth across the pool. When the motor for the drive mechanism turns in one direction the rope reels turn. As the ropes wind around the reel, the cover is pulled across the pool until it is completely closed. When the motor turns in the opposite direction, the gears to the mechanism shift, allowing the rope reels to be free-spinning, while at the same time, the roll up tube is able to turn, pulling the cover off of the pool.
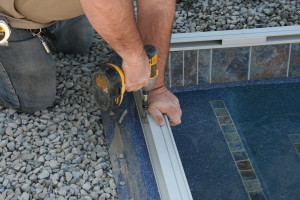
The second component group is the extrusions. This includes the aluminum track, which guides the cover back and forth as it travels across the pool. Also part of this group is the leading edge tube, which runs across the front of the cover to provide strength and rigidity, keeping the front of the cover out of the pool, and finally, the roll up tube, which the cover rolls up on.
The cover is the third component. It comprises the cover fabric, webbing (the material attached to the sides of the cover), and the rope.
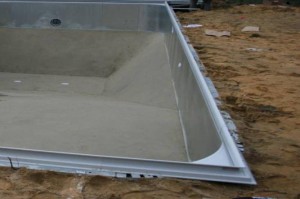
In addition to these main components, there are a number of optional components that can be used. Some are specific to the type of pool the cover is being installed on. For example, some components are made specifically for gunite pools, while others are made solely for vinyl liner or fibreglass pools.
What cover system is required?
Automatic covers are manufactured and ordered in three different system types: under guide, recessed-top guide, and deck mount. The pool’s shape, cover track location, and type of installation (i.e. a new project or existing pool) will determine what cover system is used. The following is a quick look at each system:
Under guide
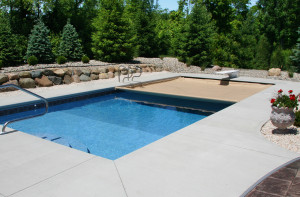
An under guide automatic cover system is generally installed on rectangular pools. With this system, the cover’s drive mechanism is mounted below grade in a cover box, while the cover track is installed under the coping. By mounting the track under the coping, it is less visible, providing a clean look for the pool. The under-guide track can be mounted in two ways. First, the cover track can be drilled and anchored to the bottom side of the coping. This was the standard method used for many years.
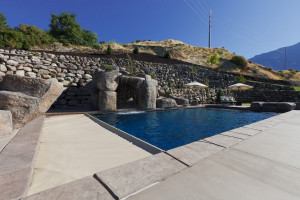
The second method, which has become the current standard, is to use encapsulation. This involves mounting the aluminum encapsulation directly to the top of the pool wall during construction. After it has been secured to the pool wall, the concrete coping (or stone, brick, etc.) is poured directly on top to lock it in place. The side of the encapsulation that faces the water will remain visible after the coping has been installed. It includes an open channel where the cover track will be positioned during the installation of the cover system. The cover track can be installed or removed from the encapsulation as needed.
This method allows the cover track to be built into the pool’s side wall. It is largely hidden from view to provide an integrated look around the pool. Encapsulation is available in different options to accommodate different pool types (e.g. fibreglass, vinyl liner, or gunite).