Legal issues and concerns involving chemical-related accidents at public swimming pools
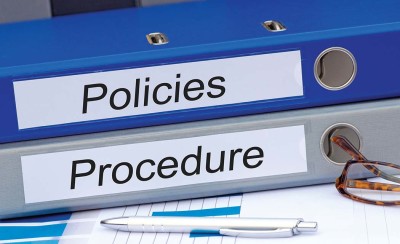
Protecting workers
Employers must provide proper personal protective equipment (PPE) for workers around chlorine. The PPE will depend on the type of chlorine application and the worker’s duties. The law mandates the strictest PPE requirements for gas chlorination systems, but all chlorine handling requires some level of protection.
When it comes to gas chlorinators, employers are obligated to provide full-face, self-contained, air-supplied breathing equipment. The breathing equipment must allow a person to withstand 15 minutes in a chlorine-filled environment and be kept in a dust-proof cabinet outside a possible chlorine contamination area. In the event that someone is trapped in a chlorine contaminated area, breathing equipment provides a better chance of survival and is mandated by law. Breathing equipment also provides more time for trained personnel to rescue victims.
Granulated and liquid chlorine applications have different PPE requirements. The employer must provide safety goggles to protect a worker’s eyes from chemical splashes and dust, and chemical-proof gloves and aprons to protect the worker’s skin and body.
In the aftermath of an accident, the pool company will need to show that functional PPE was readily available to the workers and they were properly trained to use it. Even minor chlorine contact, such as a worker using their bare hands to toss chlorine pucks into the pool, could create liability for the employer. Long-term contact with chlorine can cause chloracne, a form of dermatitis. Pool companies do not want a worker developing these preventable conditions and suing years later for failing to provide gloves.
Training
The law also requires that only properly trained workers operate chlorination equipment. Workers need to have ongoing training and reinforcement to show they are following the rules and observing best practices. Employee training is not a one-time affair. Proper training is part of an employer’s due diligence; in the event of a worker accidently mixing improper chemicals, courts will look to the employer to determine what standards the worker was held to and the rules they were instructed to follow.
Material safety data sheets (MSDS) must be provided to workers and be easily accessible. These documents highlight the safety precautions required around each chemical, the correct PPE to wear, and first aid measures.
The employer has a duty to regularly monitor and supervise an employee’s work to ensure they are following proper chlorine handling practices. Workers can take shortcuts and, over time, they can become accepted practices. From a legal standpoint, safety shortcuts are unacceptable and, in the context of a lawsuit, could be seen as carelessness that makes the operator/company liable for the claims made against it.
In the workplace, the employer should foster a culture of safety and respect for chlorine and other pool chemicals. Pool workers need to understand the consequences of mishandling chlorine. If workers are aware of the potential harm from taking safety shortcuts, it is harder for them to justify taking the shortcut in the event of an accident.
Building code requirements
The law further imposes standards for pool chlorine storage facilities. In Ontario, for example, gas chlorination systems require a fire separation barrier between the chlorine storage area and the rest of the building. Gas chlorine storage also requires emergency air ventilation capable of exchanging the room’s air 30 times per hour. Building code requirements are unique to every region, so it is important to ensure pool areas are built to the applicable code.
Most building codes require the pool’s plumbing system to be clearly labelled. Pipes containing chlorine must be painted yellow, while pipes containing potable water must be painted green. A labelled plumbing system is important in the event that maintenance is being performed on the system, and the wrong pipe is accidently opened.
Best practice requires chlorine canisters, whether full or empty, to be securely anchored to prevent their accidental movement. When chlorine canisters are not attached to the chlorinator, a valve protection hood must be in place, and a wrench must be attached to each canister. These precautions are taken to avoid rupturing canisters and breaking valves. Providing the correct wrench, within arm’s-reach, gives operators a chance to quickly tighten loose, leaky fittings.
Granulated and liquid chlorine do not require the stringent engineering controls of gas chlorination systems, but precautions still need to be taken. Ventilation is important anytime pool chemicals are stored indoors. Pool houses can trap heat and cause chemicals to give off harmful vapours. Protecting workers can be as simple as letting a storage area air-out before entering, or providing respiratory equipment for workers.
Chlorine containers can be heavy; pool companies need to be considerate of the ergonomics in pool houses or chemical storage areas. Workers need proper ways to lift and pour chemicals to prevent spilling and splashing.
Employers can require two workers must lift heavy containers or provide special tools for lifting and administering chemicals. The appropriate measures an employer needs to take will depend on the specific storage area and its layout. In many instances, the pool company and its workers need to employ common sense when constructing areas where pool chemicals are going to be stored.