Monitoring and controlling indoor air quality using a web browser-based software interface
By Ralph Kittler
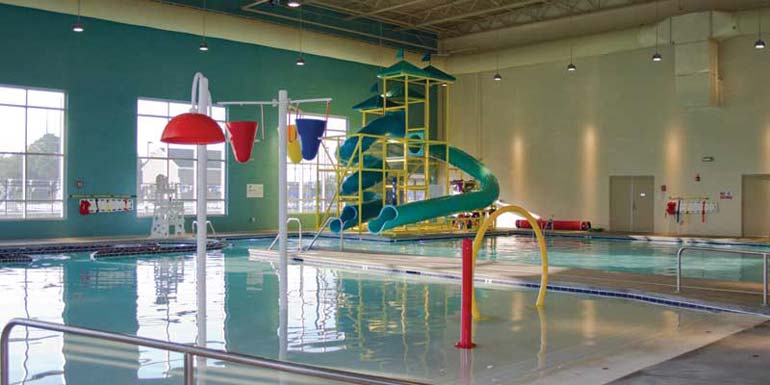
Imagine the following scenario: an aquatic facility manager is vacationing with their family in Europe and suddenly receives an e-mail alert on his/her smartphone regarding a problem with the indoor air quality at the commercial pool he/she manages. Unfortunately, the on-duty maintenance staffers are not able to diagnose or respond, but the problem needs to be fixed immediately. Thanks to today’s dehumidification system technology, this scenario might unfold (chronologically) as such:
9:42 a.m. (EDT)
Apparently, the 929-m2 (10,000-sf) natatorium he/she manages in a Toronto recreation centre just developed an operational problem needing immediate attention. The dehumidifier’s on-board micro-processor-based command centre, which maintains indoor air quality (IAQ) and energy-efficiency in the facility, just sent an emergency notification to his/her smartphone via the computer interface’s category-5 Ethernet connection to the Internet.
Calling the facility’s maintenance staff at this early juncture is not an option. In some cases, while maintenance staff might be able to fix the problem, they would likely need expert troubleshooting diagnosis and coaching. Instead, the facility manager uses his/her smartphone to log-in and connect to the dehumidifier’s on-board command and communication centre via Internet from the hotel where he/she is staying.
The dehumidifier’s command centre is accessed through a web browser-based software interface program for monitoring and controlling the natatorium’s environmental conditions and dehumidifier operations. The software program also e-mails alarm situations to the facility manager, his/her preferred local heating, ventilating, and air conditioning (HVAC) contractor, the manufacturer’s representative, the dehumidifier manufacturer, or any other user that is granted access.
9:45 a.m. (EDT)
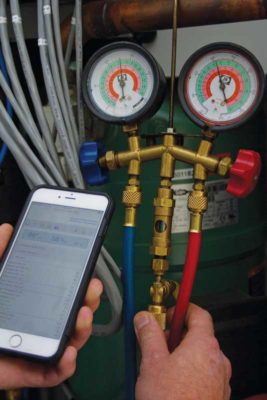
After connecting to the dehumidifier, the web browser-based software interface displays the natatorium’s vital signs of relative humidity (RH), the space temperature, and the pool water temperature. Hundreds of other parameters vital to a comfortable and well-operating natatorium environment can also be viewed, depending on the access level granted by the manufacturer.
Besides the natatorium’s operating statistics, the alarm in question reads “HP1-TD” on the facility manager’s smartphone. The ‘HP’ stands for high pressure, the ‘1’ indicates compressor number one, and the ‘TD’ means a transducer sensed the high pressure and deactivated the dehumidifier.
9:50 a.m. (EDT)
Depending on the facility manager’s previous experience, if any, with this type of alarm, and his/her training on dehumidifier and natatorium fundamentals provided by the manufacturer, the facility manager can either instruct the maintenance staff to remedy the situation, or call the manufacturer.
In this scenario, the manufacturer’s factory technicians are able to troubleshoot the unit via the same Internet connection and the unit’s web browser-based software interface.
9:54 a.m. (EDT)
The factory’s diagnosis is a shutdown of an outdoor air cooled heat-exchanger fan, the part of the system that ejects heat to the outdoors when it is not needed inside the facility. The shutdown fan caused a high-
pressure reading and the high-pressure switch shutdown the entire system. Since it is not a reoccurring problem, the prognosis speculates a possible voltage spike from the utility might have shutdown the condenser fan.