Monitoring and controlling indoor air quality using a web browser-based software interface
9:57 a.m. (EDT)
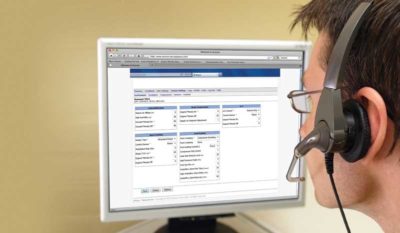
Meanwhile, the facility manager is told to continue enjoying his/her family vacation because factory technicians will attempt to instruct the natatorium’s on-site maintenance staffer to scroll through the command centre’s on-board LED readout prompts to reset the system.
10:10 a.m. (EDT)
The system resumes operation, no further alarms are triggered, and the dehumidifier does not shutdown again while factory technicians monitor its many operating parameters via the web browser-based software interface. Factory technicians monitor the unit for a few days and the alarm does not reoccur, indicating the voltage spike speculation may have been correct.
While it might have taken 15 minutes of the facility manager’s vacation time, solving the problem helped keep the facility open. Equally important is the facility saved hundreds of dollars because the local HVAC contractor was not needed to troubleshoot and solve the alarm.
This scenario may seem unrealistic; however, this technology is, in fact, being used today. Thanks to the advancements in micro-processors, the Internet, and smartphones over the last 10 years, an aquatic facility manager can monitor and possibly control a natatorium’s environment from anywhere in the world.
How can this technology reduce service costs?
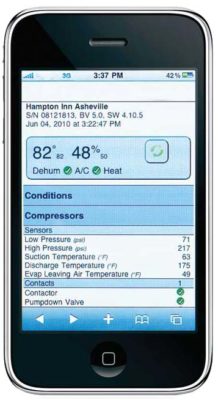
Indoor pool dehumidifiers are complex mechanical machines designed with many safeguards that automatically trigger when operating conditions deviate from their set points or ideal operating ranges. These safeguards can react to low or no water flow, insufficient airflow, excessively high or low pressures in the refrigeration circuit, or any other operating abnormality. While a unit can conceivably run if operating conditions are not optimal, the dehumidifier’s vast number of switches, sensors, and transducers are designed to prevent the unit from internal damage and protect the facility’s investment.
Low airflow, for example, is another common alarm that occurs when an electronic air switch amid the dehumidifier’s airstream senses insufficient airflow. The notification is e-mailed to the facility manager or any other authorized personnel via the unit’s software system.
A dirty filter causing restricted airflow will commonly trigger a dehumidifier’s airflow switch, which signals the need for maintenance. Thus, ensuring the correct amount of conditioned air is supplied as well as return air brought back to the unit for proper dehumidification, cooling, and/or heating.
Prior to the influx of micro-processor technology on mechanical systems, an insufficient airflow event could also shutdown the dehumidifier by triggering the low-pressure (low-refrigerant) switch. As the malfunction (trip) was related to refrigerant pressure, it could have staff members and contractors troubleshooting the wrong thing. An HVAC service contractor would be called and after an hour or two of troubleshooting, the dirty air filter is discovered. The facility is billed a few hundred dollars for the service call which could have been avoided if the system was equipped with today’s software technology, which sends an alarm identifying the specific problem.