Monitoring and controlling indoor air quality using a web browser-based software interface
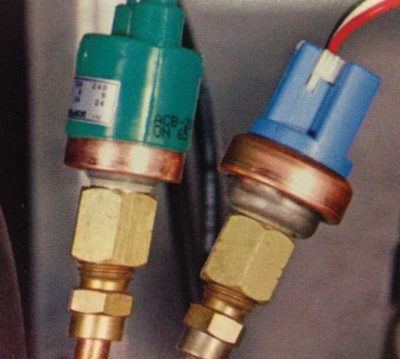
It might seem inconceivable for maintenance staff to not routinely change air filters on mechanical equipment, but it happens frequently, especially in schools, according to an article on outdoor air dehumidification in the June issue of the RSES Journal, a trade magazine for air conditioning and service technicians. The author, Len Kobylus, notes school maintenance staff (which are not too unlike aquatic facility maintenance staff or could possibly be the same personnel at high school indoor pools shared by the local community) do not frequently change mechanical equipment air filters because they are understaffed or not properly trained.
In addition to a service call, another cost associated with dirty air filters is the additional fan energy consumed during operation. Air cannot flow as easily through the media filter that is clogged with debris; therefore, the fan must work harder, which increases utility costs.
Detecting a dirty filter, via an insufficient airflow alarm e-mailed by the web browser-based software interface, will save operational costs if the filter is then replaced. Some software also allows authorized personnel to adjust the sensitivity of the sensor which detects insufficient airflow. The more sensitive these sensors are, notifications will be sent more frequently.
Further, operating a dehumidifier with clogged air filters will eventually lead to dirty coils that must be cleaned more frequently. A dirty coil also leads to poor heat transfer, which is another drain on energy in the system that will eventually raise operational costs, many times unbeknownst to the facility manager. Cleaning a dirty coil requires a much more expensive service call with respect to time and materials, which can amount to hundreds of dollars per visit, but can be avoided with a low airflow alarm.
Water flow issues
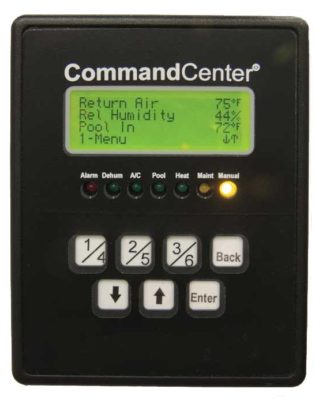
A water flow issue is another common alert a facility manager may receive. Most modern dehumidifiers are designed with an energy-recovery feature that uses the refrigeration circuit’s compressor(s) waste heat to provide up to 100 per cent pool water heating. Essentially, this is free heat for the pool as the facility has already paid the utility for the cost of running the compressor(s) for dehumidification and cooling.
Many times an insufficient water flow alarm is activated because a valve to the dehumidifier was turned off. For example, valves are commonly forgotten after backwashing the filter. Without an alert, the system will continue dehumidifying, but pool water heating is automatically segued to the pool’s backup duty conventional gas-fired or electric water heater. Since pool heaters are not energy-recovery components, it is an unnecessary and wasteful cost for the facility.
While an error of this nature might seem inconceivable, there have been dozens, maybe hundreds of instances where manufacturer technicians have arrived at a site only to discover the pool water flow valve to the dehumidifier had been turned off. There are also many instances where the installing contractor never piped
the pool water to an energy-recovery dehumidifier at the facility inauguration many years prior. In both cases, the facility had been losing thousands of dollars annually in pool heating costs that could have been provided free by the dehumidifier.
Excessive water flow can also be an expensive problem. Besides being a waste of circulation pump energy, the higher water flow can actually erode piping and the pool heater. Pinpointing high water flow via web browser-based software interface communication will save the facility operating costs and prevent premature failure of water loop components.
By calibrating the software to send alerts to the facility manager, this wasteful scenario would not last more than a day. The facility manager can call the factory technicians to investigate, which will eventually be diagnosed as a closed valve.