New building options for above-ground pools
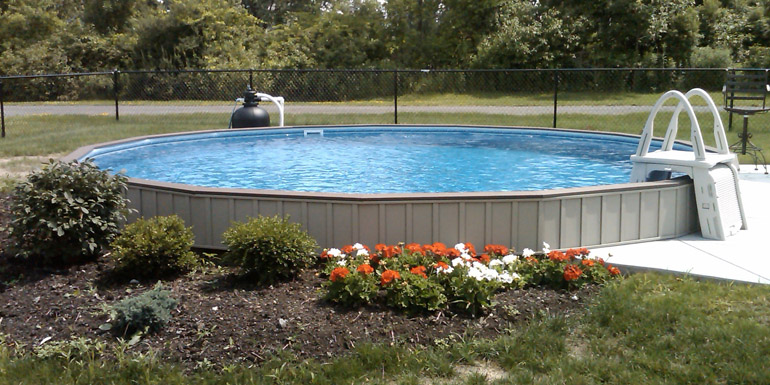
By Eric Gohn
When it comes to selling and installing above-ground swimming pools, today’s builders are no longer limited by the traditional installation methods concerning these pools, which are typically built ‘above’ or ‘on’ the ground. Thanks to product development by various manufacturers, new options are available to homeowners that allow these pools to be installed above-ground, semi-inground, or even completely inground. Further, these options provide both retailers and builders a variety of selling options to meet a number of consumer price points and backyard configurations.
Meeting a market need
In recent years, several above-ground pool manufacturers have introduced new, high-end hybrid models that are much stronger than the typical above-ground pool, thus enabling the different installation methods described above. Rather than using a single, rolled-wall sheet, these pools comprise heavier-grade steel panels.
This new generation of above-ground pool is designed to meet specific market needs that were not being met previously. For example, these pools can be installed in sloping backyards and provide a budget-friendly option for consumers looking for more than a traditional above-ground pool. Further, these hybrid pools provide better longevity, especially in extreme weather situations, more possibilities when it comes to backyard esthetics and landscaping, and more choices when it comes to the consumer’s price point.
Weather and terrain
One company that has had success in offering these hybrid pools is Blok Pools of Pembroke, Ont., which has been selling pools for more than 45 years.
“The traditional above-ground pool (if not winterized properly) has a hard time surviving an extremely cold winter,” says the company’s general manager, Dan Fraser. “If the liner gets damaged and starts to leak, even slightly, the pool walls get pulled in by the winter cover and are virtually impossible to repair.”
After the winter of 2006, which destroyed more than 5,000 above-ground pools in Ontario and Quebec, Fraser found consumers in his area were looking for a better onground option.
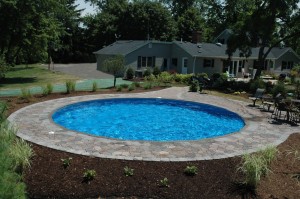
“In response to this, we started offering high-end onground and semi-inground pools three years ago,” he added. “These pools comprise 14-gauge steel walls and come with a full 20-mil, virgin-vinyl liner, which will provide the consumer many years of service.”
When it comes to terrain, many consumers have backyards that are sloped, which in many cases eliminates the option of installing a traditional above-ground pool. By comparison, hybrid pools were developed with a sloped backyard in mind as they are well-suited for these landscape configurations.
From an installer’s perspective, these pools can be easily set up as less time is required for ground preparation, and equalizing the distribution of water weight to ground is not required to keep the pool in place. Further, a sand/cement slurry mix also is not needed. Finally, if the installation requires excavating into a slope, the same dirt can be used as backfill against the pool.
For example, B Z Pools and Decks Inc., of Johnston, Pa., which started offering hybrid pools this past season, sold and installed six pools that were all semi-inground and mostly on slopes.
“We use ‘cap blocks’ below each panel joint,” explains the company’s Brian Zettle. “After excavation, we mark the ground with paint every 1.2 m (4 ft) and place a 203- x 406-mm (8- x 16-in.) solid ‘cap block’ down, set via a transit level. A small level is also placed on each block to ensure they are all level. Then we assemble the panels on top of these caps without the need to worry about levelling the panels after assembly.”
According to Zettle, it takes more time to level the entire pool if the panels are bolted together first—especially when dealing with a sloped terrain.