Phase 2: The initial review
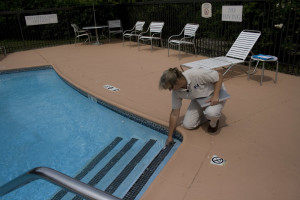
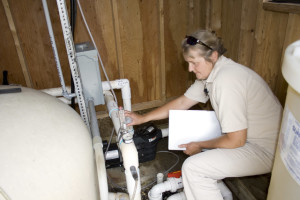
Create an audit checklist that includes the location, pool volume (litres/gallons), and manufacturer’s equipment information (e.g. pump performance curves and flow rates, filter size and media rate, and current heating appliance and efficiency ratings). It is also important to assess all of the old equipment as well as the amount of energy used to operate it. Ask the homeowner to provide at least six months of utility bill information (e.g. electrical and gas) as this data will assist in calculating the energy savings during the recommendation phase. An on-site visual inspection is also vital to the recommendation phase as it provides the audit team with the information necessary to make appropriate recommendations. The following are some key areas to watch for when performing an on-site visual inspection:
Swimming pool structure
The swimming pool structure is sometimes overlooked as being a large contributor to added energy costs. Heating costs represent a large expense in swimming pool operation. If there is a leak in the concrete structure, plumbing, or through the vinyl liner, the homeowner is spending wasteful dollars to heat their pool due to the addition of replacement water, which is also an added expense.
With the cost of fossil fuel climbing in every region, it makes good sense to recommend pool owners spend the money necessary to correct these leaks. For example, if a pool is losing 25.4 mm (1 in.) of water per week, this amounts to 2,366 L (625 gal) in 93 m2 (1,000 sf) of surface area. Over the course of a year, even a small 4.8- x 9.7-m (16- x 32-ft) pool will waste 62,080 L (16,400 gal). This is not only an added expense when considering water consumption, but also loss of chemicals and heating. By showing these figures to the pool owner, it will be easier to impress upon them the value of fixing the leak.
Filtration
Sand filtration systems require water usage during the backwashing cycle. Part of the energy audit should be an inspection of the filters, including age of the system, sand replacement intervals, and the time required to clean (i.e. backwash) the system.
The litres/gallons backwashed to the waste system can be calculated based on flow rates. Backwashing filter dirt and debris (along with pool chemicals) into lakes and streams can impact the environment as well as create a hazard to aquatic ecosystems downstream.
In this case, the audit team may suggest the pool owner use a different filter media (e.g. zeolite, cartridge, etc.).
Lighting
The quantity and condition of pool and spa lights, wattages, amps and volts all influence energy draw. The energy auditor can have a discussion with the owner to help them understand the overall lighting cost, and when they would like the lights on. This can be calculated using Ohm’s Law: Amps x Volts = Watts and converting to kilowatt hour (kWh) usages, which is the same way electrical utilities calculate charges.
Inspecting all connections and conditions of the lighting is also important. The industry offers an array of energy-efficient, light-emitting diode (LED) lighting systems that can be retrofitted to traditional halogen fixtures.