Energy
The lost pressure energy is easily measured by reading pressure gauges at various points in the plumbing system. The gages will show the pressure drops throughout the system, except across the pump where it increases. In fact, the increase in pressure across the pump exactly matches the total decrease throughout the rest of the circulating system. The sum of all pressure losses, plus the difference in elevation between the surface water level of the suction ports and the surface water level of the discharge ports, is commonly called TDH.
TDH is important because it is a direct measurement of the system’s efficiency and is used to select the pump. A properly sized pool filtration system will have a TDH of less than 12 m (40 ft) of head. Poorly designed systems may be twice that number.
TDH is directly related to the approximate square of the velocity—in other words, if the velocity is doubled, the TDH will almost quadruple. Thinking about it the other way, to cut TDH in half, velocity need only be reduced by about 25 per cent.
Velocity
How are velocities reduced to get the TDH to a reasonable level? First, reduce flow rates by moving only the minimal amount of water necessary. If the volumetric flow rate requirement is 114 lpm (30 gpm), do not pump 151 lpm (40 gpm). Second, properly size the pipes to handle the flow rate. Do not necessarily oversize—this might imply a careless and wasteful use of PVC. Sound engineering should be used to select the proper diameter.
To keep things simple, follow these guidelines:
- Minimum scouring velocity = 0.15 m/sec (0.5 ft/sec)
- Maximum suction-side velocity = 1.4 m/sec (4.5 ft/sec)
- Maximum discharge-side velocity = 2 m/sec (6.5 ft/sec)
Table 1: Maximum flow rates for ASTM D1785-06 Sch 40 PVC | ||
Nominal | Maximum suction flow at 1.4 m/sec | Maximum discharge flow at 2.0 m/sec |
Size (OD) | (4.5 ft/sec) | (6.5 ft/sec) |
25 mm (3/4″) | 26 lpm (7 gpm) | 42 lpm (11 gpm) |
32 mm (1″) | 45 lpm (12 gpm) | 68 lpm (18 gpm) |
40 mm (1-1/4″) | 79 lpm (21 gpm) | 114 lpm (30 gpm) |
50 mm (1-1/2″) | 110 lpm (29 gpm) | 155 lpm (41 gpm) |
63 mm (2″) | 178 lpm (47 gpm) | 257 lpm (68 gpm) |
75 mm (2-1/2″) | 254 lpm (67 gpm) | 367 lpm (97 gpm) |
90 mm (3″) | 394 lpm (104 gpm) | 568 lpm (150 gpm) |
110 mm (4″) | 678 lpm (179 gpm) | 977 lpm (258 gpm) |
160 mm (6″) | 1,533 lpm (405 gpm) | 2,214 lpm (585 gpm) |
225 mm (8″) | 2,657 lpm (702 gpm) | 3,838 lpm (1,014 gpm) |
280 mm (10″) | 4,187 lpm (1,106 gpm) | 6,049 lpm (1,598 gpm) |
315 mm (12″) | 5,943 lpm (1,570 gpm) | 8,585 lpm (2,268 gpm) |
For example, if a 75,708-l (20,000-gal) pool requires a 360-minute turnover, the flow rate is 210 lpm (56 gpm). On the suction side of the pump, you will need a 75-mm (2.5-in.) outside diameter line; on the discharge side of the pump, you will need a 63-mm (2-in.) outside diameter Sch 40 PVC line.
Keep in mind this is a quick and easy way to initially size up all the lines. Long runs or numerous fittings may require the plumbing to be up-sized, thus reducing velocity and head loss even further.
It is also important to note there are only discrete sizes of pipe and fittings. This means that if, for example, the flow rate is 182 lpm (48 gpm), the suction-side diameter selected from the previous table is 75 mm (2.5 in.) This will have an actual velocity of only 1 m/sec (3.2 ft/sec). In other words, the 1.4 and 2 m/sec (4.5 and 6.5 ft/sec) suction and discharge velocity limits in this table occur at specific flow rates. However, most line size selections made with this table result in even lower velocities by design.
These criteria are what I would term a best-practices approach to line size selection. In fact, one of the benefits of our 1.4 and 2 m/sec (4.5 and 6.5 ft/sec) design limits is that if something changes, and the flow rate exceeds the design flow rate, there is a bit of headroom before the velocity exceeds the code limit.
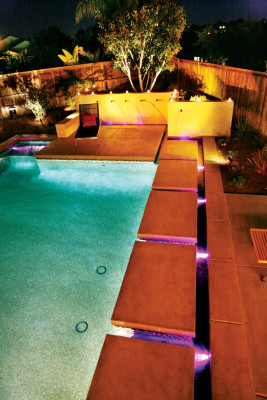
So, actual velocities may be less than these recommended limits, but line sizes might need to be increased anyway—how is that determination made? The answer is in the TDH analysis, which is too complicated to explain in this article. If you want to learn it, a detailed electronic worksheet—where pipe diameters, lengths, flow rates, fittings and equipment are all tallied and the TDH is calculated—is available. It’s all part of the Genesis 3 Advanced Fluid Engineering Design School package, which also includes software training.
How do we apply these criteria to size split-suction outlets? The easiest way is to size the primary suction line for the 1.4 m/sec (4.5 ft/sec) maximum, as selected in the table above, then maintain the same size pipe for all split outlets. This way, if one outlet is blocked, the other(s) can handle 100 per cent of the flow without a significant head loss in the branch piping. (This results in a dangerous vacuum force on the blocked cover.)
If all the branch plumbing on split-suction outlets is the same size as the primary suction line and sized for the 1.4 m/sec (4.5 ft/sec) maximum, during normal operation the flow rate and velocity will be halved to 0.7 m/sec (2.25 ft/sec), until one cover is blocked and the other handles 100 per cent of the flow at 1.4 m/sec (4.5 ft/sec) maximum. In the example of a triple-split set of suction outlets, each is expected to operate at a maximum of 0.47 m/sec (1.5 ft/sec), one-third of the 1.4 m/sec (4.5 ft/sec) design, until one cover is blocked and the other two roughly split the total flow for a velocity of 0.7 m/sec (2.25 ft/sec) in each line. When designing spas, a two-pump system, at minimum, is always used. Aerated venturi jets are never used with the filtration system. Spa jets are always on their own dedicated pump(s). The filtration system’s split suction outlets are usually located on the floor, separated by 0.9 m (3 ft) clear. The jet pump suction outlets are located in the footwell at the face of the bench, separated by 0.9 m (3 ft) or on different planes.
The next question becomes how to handle skimmer equalizer lines. Installion of skimmer equalizers is rarely recommended; existing ones should be plugged wherever possible. Skimmer equalizers are merely bandages for another problem: inadequate autofill mechanisms. Builders began installing equalizers when the water level dropped below the skimmer throat, causing the filter pump to run dry and be damaged. Now, we have reliable autofills; the risk of any suction entrapment hazard is much worse than a pump seal failure, or even an entire pump replacement. Builders are actively splitting these skimmer equalizers to comply with the code requirements—but elimination trumps mitigation every time.