Reducing operating expenses with energy-smart equipment
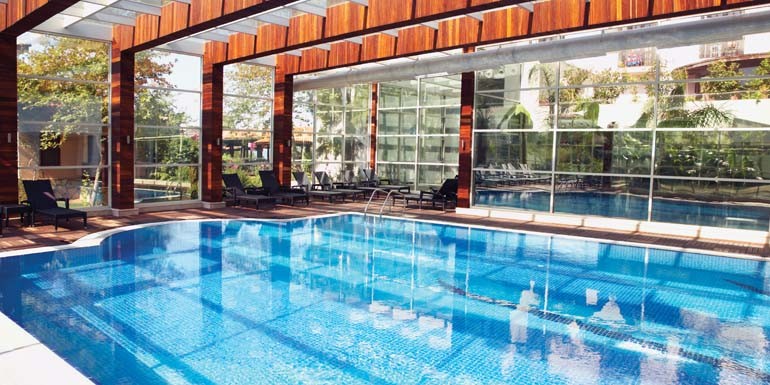
By Mike Fowler
Facility managers have learned over the past few years that going ‘green’ can significantly lower an aquatic facility’s operating costs. Pumps and filters are among the items most scrutinized due to the vast amount of energy they consume. To reduce costs associated with water circulation and filtration it is important to understand why pumps and filters consume large amounts of energy and what options are available to lower consumption. This article will look at various ways an aquatic facility can save energy and money with green options for pumps and filters.
Extracting costs from filtration
The type of filter used (e.g. cartridge, sand or diatomaceous earth [D.E.]) can have a significant impact on energy consumption, as each one places different levels of resistance on the circulation system.
Although sand and D.E. filters function more effectively as dirt accumulates, a dirty filter can increase the pump’s workload. In fact, the difference between a clean and dirty filter can nearly double the pump’s energy consumption. If friction loss can be decreased in the facility’s plumbing design and equipment sizing, less horsepower (hp) is required to achieve the desired flow rate. While the type of filter installed is often a personal preference, the energy savings realized when using an oversized cartridge filter to reduce overall system head loss is well documented.
Finally, by simply keeping the pool’s filter clean and skimmer basket free of leaves and other debris, energy savings can be quite significant.
Circulate savings by selecting the right pump
Proper pump selection (sizing) and optimal flow rates (as mentioned above) are additional ways an aquatic facility can increase energy savings. Affinity laws indicate the power demanded by a pump is proportional to the cube of the flow rate. For example, if the pump’s flow rate is doubled, then its power demand is increased by a factor of eight. Therefore, it is important to utilize the smallest pump that is capable of completely turning over the pool water in an acceptable amount of time.
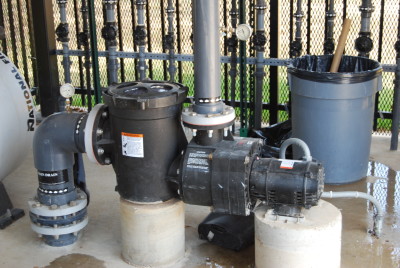
Furthermore, during the pump selection phase, the facility’s auxiliary features (e.g. spray pads, fountains and waterfalls) should also be considered, as it is common for them to use the pool’s main pump. Some building codes, however, require the use of a multi-speed pump, or in some cases, a separate pump for each auxiliary pool load.
“Pumps for aquatic facilities are oversized by design, sometimes more than 20 to 40 per cent bigger than they need to be,” says Mark Caldwell, president and CEO of Pool Services Corp, a commerical pool service company in Myrtle Beach, S.C. “This happens because many architects and engineers look at what is required, then pick the next size up to be sure the pump can handle the job.”