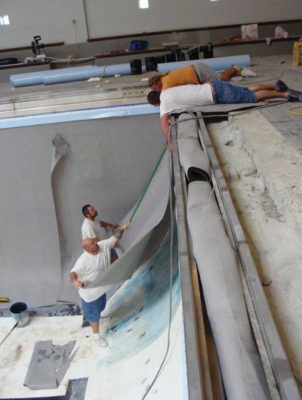
One of the initial complaints by the facility managers of these pools was regarding water maintenance. In addition to repainting and patching the pool surfaces, they were also having a difficult time with water chemistry. The plaster surface of the pools appeared to be suffering from calcium leaching out of the substrate, especially as the surface became rougher over the years. The rough surfaces also allowed more dirt to collect in the pools which meant more chemicals were required to keep the water clean and clear.
It is important to understand before a PVC membrane can be installed, several steps must take place first to prep the pool to ensure the long-term success of the liner. To start, a series of PVC strips need to be fastened along the perimeter under the stainless steel gutter, which is attached to the turndown flange. Next, the pool’s surface is prepared by smoothening rough spots, patching divots, and bridging gaps using an acrylonitrile butadiene styrene (ABS) thermoplastic polymer plate. Then, the walls and floors are washed with an algaecide to prevent any algae growth behind the PVC membrane.
Once the surface has been treated, a layer of adhesive is applied to the pool’s perimeter walls and floor to adhere a felt lining. The felt acts as a barrier to smoothen any remaining rough surfaces within the old pool. Even though the PVC membrane is a reflective material, the felt liner covers any surface imperfections and ensures the liner material has a smooth appearance—it also provides a cushioned feel for bathers. The felt lining is attached to the substrate using a solvent-based contact adhesive to ensure a strong, permanent bond.
Lining the pool surface
After applying the felt on each of these projects, the 2.05- x 25-m (6- ft 9- in. x 82-ft) PVC rolls were brought in. In many cases, these rolls had to be manoeuvred through standard-sized doorways and brought into the pool area one by one using hand trucks, rather than by the pallet.
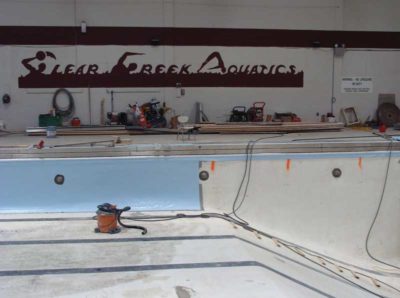
The PVC membrane was then rolled out and positioned within the pools. The material is essentially tailored to the pool on-site. Once the pieces were measured, cut, and positioned, a tack weld or pre-weld was used to hold it in place. Using a heat gun, each seam is heat welded on-site by melting them together. In doing this, the PVC seams should overlap approximately 51 to 76.2 mm (2 to 3 in.). The membrane that comes up the pool wall is ultimately terminated by welding it directly to the PVC band, or attaching it mechanically, which was the case for these three projects.
To add another waterproofing measure, a sealer was applied along the seam edges to ensure water would not seep into the scrim of the material over time. This procedure also rounds out the seams and adds an extra layer of waterproofing to the liner at critical areas.
In the case of these three pools, in addition to the base blue material, the racing lanes, targets, safety line, and other pool markings also had to be welded on using a black PVC material. This material is placed on top of the first PVC membrane layer (blue) using precise skill to ensure proper location and sizes during installation.