Wood composite decking
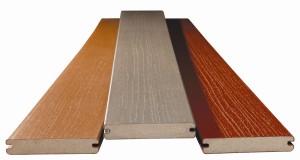
Wood composite decking products are often synonymous with green building. They gain LEED points through their manufacturing processes and recycled content. Traditional wood composite decking are typically made from high-density polyethylene (HDPE) and comprise 50 per cent less reclaimed wood byproducts, and 50 per cent recycled plastics, e.g. trash bags, plastic milk jugs, and shampoo/laundry detergent bottles.
These plastics have a higher tensile strength and are chosen to contribute to the density, structure, and durability of the composite deck boards. The wood component incorporated into composite decking is often referred to as wood flour, which can come from many different sources ranging from lumber mill byproducts, recycled/reclaimed door and window trim, recycled wood framing material, cabinets, or any other natural wood product. These accumulated wood products are then ground into a powder, similar in consistency to ‘flour,’ then combined with the plastic mix and a urea-formaldehyde free binding agent, before being formed into deck boards. The plastic then encapsulates the wood flour to provide a barrier resistant to harsh weather, splintering, mould, and decay. The majority of composites are then wrapped with a vinyl coat, which gives the surface of the product its durability, as well as the colour of each deck board.
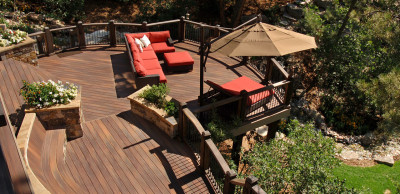
In addition to using recycled and reclaimed materials in the construction of the boards, wood composite decking companies pride themselves in their efficient, waste-free manufacturing processes. For example, after the boards are compressed and formed, water is used to cool them. As the water washes over the boards, it comes in contact with the multiple chemicals used during the manufacturing process. This water is contained in a closed loop system, which is recycled and used over and over again. The system does not release any water back into the environment.
Nearly all composite companies pull their recycled content from areas immediately surrounding their manufacturing plants, thus relieving their local landfill sites of thousands of tons of recyclable waste annually. Due to the recycled content, and environmentally responsible manufacturing process, the majority of composite decking products are even recyclable after they have reached their use.
Plastic composite
Plastic composite decking products, specifically cellular polyvinyl chloride (PVC) decking, differ greatly from traditional wood-flour composite deck materials. Primarily, plastic composites do not use recycled materials during the manufacturing process, and there is no wood or wood flour incorporated into the construction of the board.
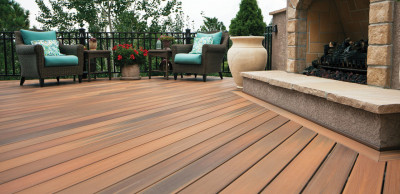
The PVC resin component of these boards is derived from abundant, naturally occurring salt, and combined with natural gas. Colour is added to the resin mixture; the boards are then moulded and embossed with the chosen texture or grain pattern.
Only sustainable virgin materials are used during the manufacturing process of cellular PVC decking products. That said, these decking materials achieve their ‘green’ designation via product packaging, transportation, product longevity, and no maintenance.
These companies use recycled packaging containers to protect their product during transportation. Whether the packaging is plastic wrap, cardboard, or wood crates, all of these protective barriers can be made from recycled product. Also, protective packaging shields the product from damage, making more of the product useable, and reducing the amount of damaged product entering landfill sites. Lessening the amount of non-biodegradable waste products entering landfill sites is always better for the environment.
PVC decking is significantly lighter than its wood composite cousin. Being a lighter product means more of it can fit on trucks, trains, or any other mode of transport, which results in fewer vehicles needed to move this material to its retail destinations and, therefore, reducing the carbon footprint generated during transportation from the manufacturer.
One significant advantage to PVC/plastic composite decking is its extreme durability. These deck boards are scratch and dent resistant, and they do not chip, cup, or warp. The durability of PVC decking contributes to the product’s lifespan, which is typically 25 years. The durability and longevity of PVC decking, combined with its minimal maintenance requirements, means a deck that looks great for many years without having to sand, stain, or paint, thus minimizing the use of products containing harmful volatile organic compounds (VOCs).