The intricacies of automated chemical controllers
Primary disinfection and pH control
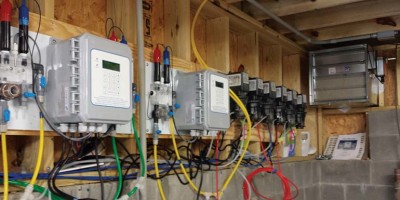
Primary disinfection using sodium hypochlorite (NaClO), calcium hypochlorite (Ca[ClO]2), bromine (Br), dichloroisocyanuric acid (C[O]NCl)2(C[O]NH), trichloroisocyanuric acid (C3Cl3N3O3), or chlorine generation (salt systems) have always been part of commercial pool and spa automation. However, chemical automation now goes beyond primary disinfection and pH control with methods for secondary disinfection, as recommended by the Centers for Disease Control and Prevention’s (CDC’s) Model Aquatic Health Code (MAHC).
Secondary disinfection support
More often than not, the industry is now seeing the need for a secondary disinfection system as a backup to the primary unit. As a result, today’s chemical controllers are now capable of automating, managing, and supporting the use of substitute sanitizing systems, which is mandatory for saltwater pools.
Enzymes and shock treatments
Some controllers can also be set-up to add enzymes and shock treatments. This treatment can be scheduled to start automatically at a specific time and date, when bathers are not in the pool. However, facility operators should note, non-chlorine shock will cause a temporary increase in ORP and a false DPD reading.
Choosing the best chemical controller
All of the above should be taken into account when selecting the type of measurement system for a chemical controller. The cost of this equipment is often a hurdle in the decision-making process; however, the needs of the facility should be first and foremost, and then balanced with any possible monetary limitations.
The initial expense of most chemical controllers can be justified by operational cost savings as well as the increased longevity of equipment and pool/spa surfaces. Facility operator’s must also keep in mind the type of chemical controller selected should reflect the other equipment used at the facility.
For example, ORP is affected by pH and cyanuric acid, while colourimetric ppm measurements are the least susceptible. ORP chemical controllers will require the lowest investment and will tell a facility operator how much sanitizer is available for use. On the other hand, selective membrane sensor measurements tell the facility operator how much sanitizer is in the water. Therefore, a chemical controller capable of measuring both can help identify and solve problems when combined chlorine is present in the water. Further, both systems require less maintenance. Colourimetric units require minimal power, but require reagents and, thus, use more water for testing.
Further, for outdoor pools using cyanuric acid, facility operators should note actual chlorine levels (ppm) will fluctuate when there is ORP control due to the variables affecting these types of automatic chemical controllers. This fluctuation will occur during sunrise and dusk due to the chlorine molecules associating and disassociating from the cyanuric acid. Ideally, a facility will have ORP and ppm control to ensure the proper sanitizer levels required by local health authorities remain constant, while also measuring the true water quality.
Lance Fitzsimmons handles pool and spa chemical automation sales and support for ControlOMatic in Grass Valley, Calif. He has been in the pool industry since 1984 and has worked directly in the servicing of chemical automation products since 1991 with Acu-Trol, Ecolab, and Leslie’s in multiple roles—from technical support to sales. Fitzsimmons is a Certified Pool/Spa Operator® (CPO®) instructor and has a degree in sales management. He can be reached via e-mail at lance@controlomatic.com.